Sputtered low-E (low emissivity) coating is a type of thin film applied to glass surfaces to improve energy efficiency by reducing heat transfer. This coating is created using a process called sputtering, where energetic ions bombard a target material, causing atoms to be ejected and deposited onto a substrate. The result is a highly reflective and durable layer that minimizes the amount of infrared and ultraviolet light passing through the glass while allowing visible light to transmit. This technology is widely used in energy-efficient windows for buildings, helping to reduce heating and cooling costs.
Key Points Explained:
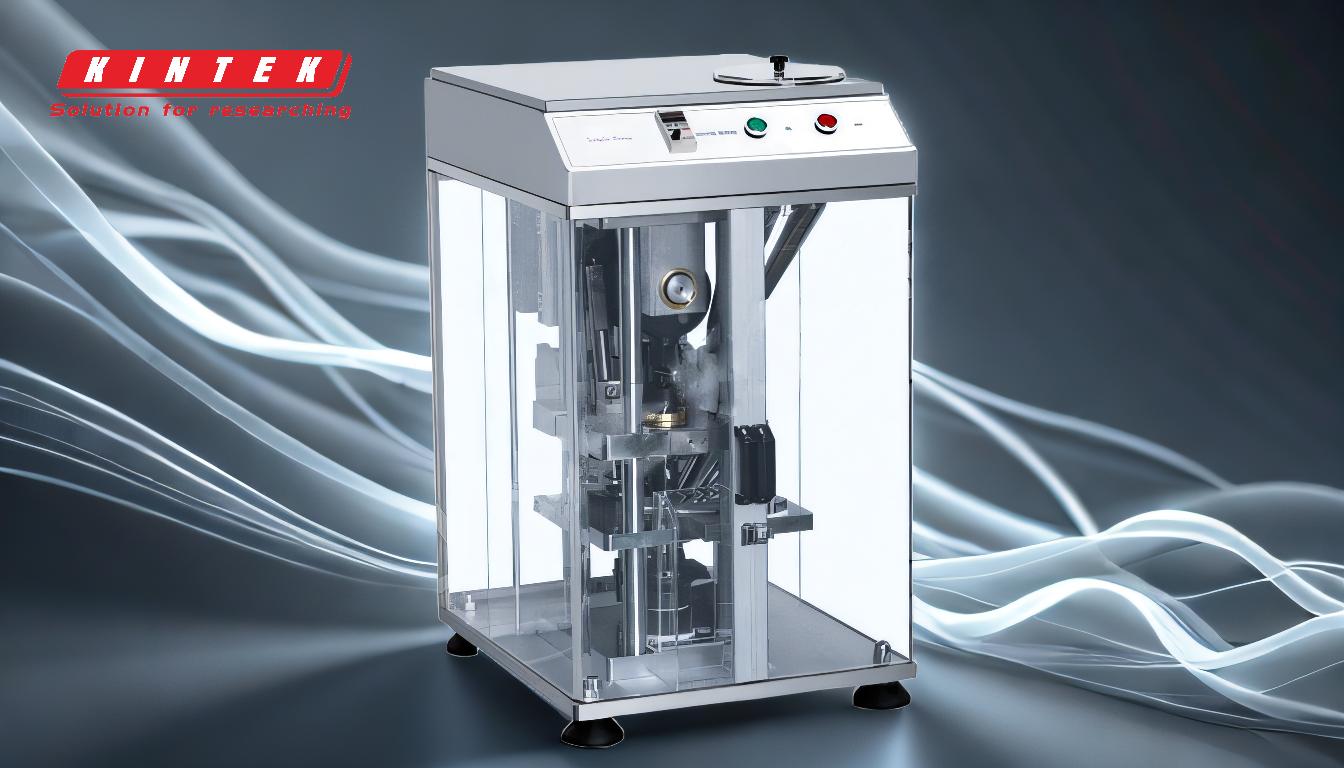
-
What is Sputtering?
- Sputtering is a physical vapor deposition (PVD) process where energetic ions, typically argon ions, bombard a target material (cathode) in a vacuum chamber. The impact ejects atoms from the target, which then deposit onto a substrate (anode) to form a thin film. This process is highly controlled, allowing for precise and uniform coatings.
-
Low-E Coating Definition
- Low-E coatings are designed to reduce the emissivity of a surface, meaning they minimize the amount of thermal energy (heat) that is radiated or transferred through the material. In the context of glass, low-E coatings help regulate indoor temperatures by reflecting infrared light while allowing visible light to pass through.
-
How Sputtered Low-E Coatings Work
- Sputtered low-E coatings are applied to glass surfaces in multiple ultra-thin layers, often consisting of metals like silver, gold, or other conductive materials. These layers are sandwiched between dielectric layers (e.g., metal oxides) to enhance durability and optical performance. The result is a coating that reflects infrared radiation (heat) while maintaining high visible light transmittance.
-
Benefits of Sputtered Low-E Coatings
- Energy Efficiency: By reflecting infrared radiation, sputtered low-E coatings reduce heat loss in winter and heat gain in summer, improving the energy efficiency of buildings.
- UV Protection: These coatings block a significant portion of ultraviolet light, which can fade furniture and fabrics.
- Durability: Sputtered coatings are highly durable and resistant to environmental factors, making them suitable for long-term use.
- Aesthetic Appeal: The coatings maintain high clarity and do not significantly alter the appearance of the glass.
-
Applications of Sputtered Low-E Coatings
- Architectural Glass: Widely used in windows, skylights, and facades of residential and commercial buildings to improve energy efficiency.
- Automotive Glass: Applied to car windows to reduce heat buildup inside vehicles.
- Specialized Glass: Used in greenhouses, museums, and other environments where controlled light and heat transmission are critical.
-
Comparison to Other Low-E Coating Methods
- Sputtered low-E coatings are often compared to pyrolytic low-E coatings, which are applied during the glass manufacturing process. While pyrolytic coatings are durable and can be used in single-pane applications, sputtered coatings offer superior optical performance and are typically used in double- or triple-pane insulating glass units.
-
Challenges and Considerations
- Cost: Sputtered low-E coatings can be more expensive than other types of coatings due to the complexity of the sputtering process.
- Handling: The coated glass requires careful handling during installation to avoid damaging the delicate layers.
- Maintenance: While durable, the coatings may require specific cleaning methods to prevent scratches or degradation.
By understanding the sputtering process and the properties of low-E coatings, it becomes clear why this technology is a cornerstone of modern energy-efficient building design. Its ability to balance thermal performance, durability, and aesthetics makes it an ideal choice for a wide range of applications.
Summary Table:
Aspect | Details |
---|---|
Process | Sputtering: Physical vapor deposition using energetic ions in a vacuum. |
Function | Reduces emissivity, reflecting infrared radiation while allowing visible light. |
Key Benefits | Energy efficiency, UV protection, durability, and aesthetic appeal. |
Applications | Architectural glass, automotive glass, greenhouses, museums, and more. |
Comparison | Superior optical performance compared to pyrolytic low-E coatings. |
Challenges | Higher cost, delicate handling, and specific maintenance requirements. |
Ready to enhance your building's energy efficiency? Contact us today to learn more about sputtered low-E coatings!