Sputtering in physics is a process where high-energy particles or ions bombard a solid target, causing atoms or molecules from the target's surface to be ejected. This phenomenon occurs naturally in space, contributing to cosmic dust formation and spacecraft corrosion. On Earth, sputtering is harnessed in industrial and scientific applications to deposit or remove thin films of materials at the nano- or micrometer scale. These films are critical in fields like optics, electronics, and materials science. The process requires a vacuum environment to ensure controlled and precise deposition, making it a cornerstone of modern manufacturing and research.
Key Points Explained:
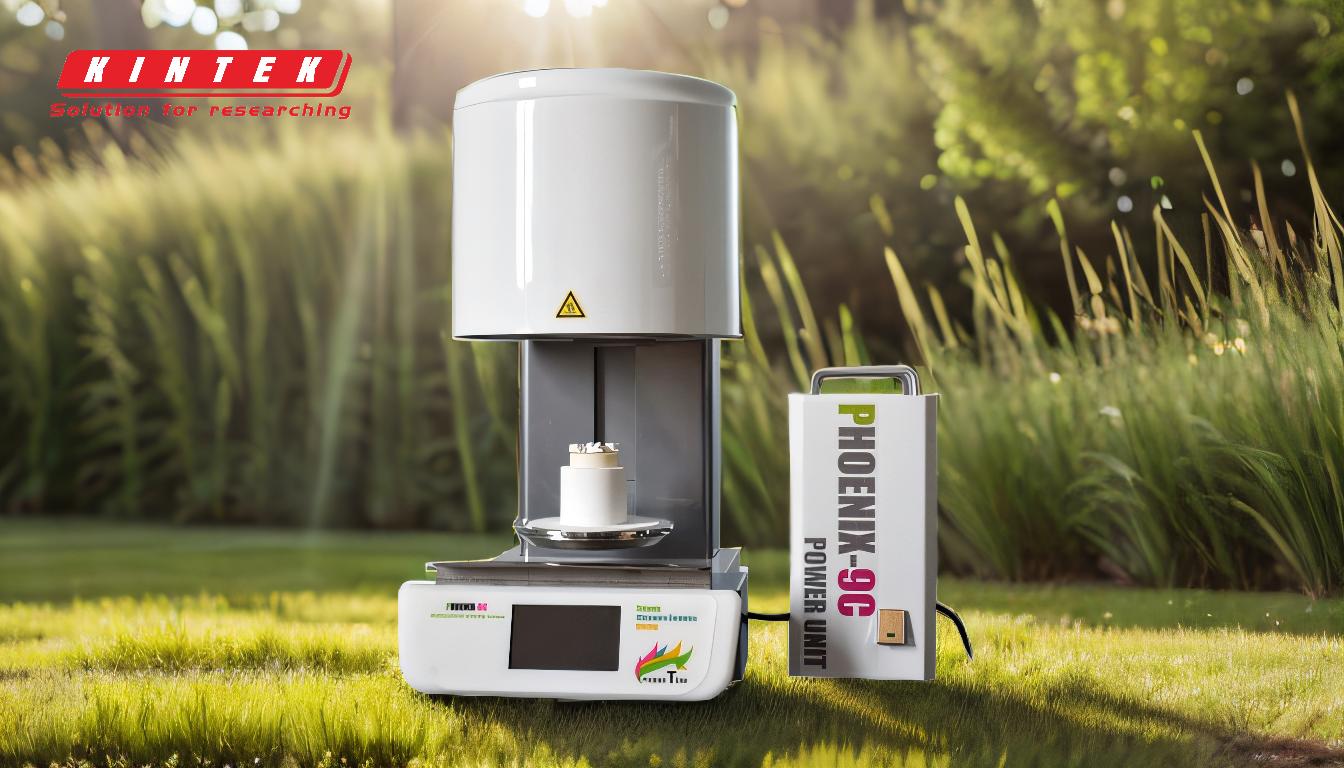
-
Definition of Sputtering:
- Sputtering is a physical process where high-energy particles, typically ions from a plasma, collide with a solid target material. This collision transfers energy to the target's surface atoms, causing them to be ejected.
- The ejected material can be deposited onto a substrate, forming a thin film, or removed entirely, depending on the application.
-
Mechanism of Sputtering:
- The process begins with the bombardment of a target material by ions, often derived from an inert gas like argon.
- When these ions strike the target, they transfer kinetic energy to the surface atoms, enabling them to overcome the binding forces of the solid.
- The ejected atoms or molecules are neutral and travel through the vacuum environment before condensing onto a substrate.
-
Natural Occurrence of Sputtering:
- In space, sputtering occurs naturally due to the interaction of cosmic rays and solar wind with solid surfaces, such as asteroids, moons, and spacecraft.
- This process contributes to the formation of cosmic dust and can cause erosion or corrosion of spacecraft materials over time.
-
Industrial and Scientific Applications:
- Thin Film Deposition: Sputtering is widely used to deposit thin films of materials onto substrates. These films are essential in manufacturing semiconductors, optical coatings, and magnetic storage media.
- Surface Modification: The process can also be used to clean or etch surfaces by removing material at the atomic level, ensuring precision in microfabrication.
- Research and Development: Sputtering is a key tool in materials science, enabling the study of surface interactions and the creation of novel materials with tailored properties.
-
Vacuum Environment:
- Sputtering requires a vacuum to minimize interactions with air molecules, which could interfere with the process.
- The vacuum ensures that the ejected particles travel unimpeded to the substrate, allowing for precise control over film thickness and composition.
-
Types of Sputtering:
- DC Sputtering: Uses a direct current (DC) power source to generate ions for bombardment. Commonly used for conductive materials.
- RF Sputtering: Utilizes radio frequency (RF) power for non-conductive materials, as it avoids charge buildup on the target.
- Magnetron Sputtering: Employs magnetic fields to enhance the efficiency of ion bombardment, increasing deposition rates and improving film quality.
-
Advantages of Sputtering:
- Precision: Sputtering allows for the deposition of films with nanometer-scale accuracy, making it ideal for high-tech applications.
- Versatility: It can be used with a wide range of materials, including metals, ceramics, and polymers.
- Uniformity: The process produces highly uniform films, even over large areas or complex geometries.
-
Challenges and Considerations:
- Cost: The equipment and vacuum systems required for sputtering can be expensive.
- Complexity: The process requires careful control of parameters such as pressure, temperature, and ion energy to achieve desired results.
- Material Limitations: Some materials may be difficult to sputter due to their physical or chemical properties.
-
Future Trends:
- Green Sputtering: Research is ongoing to develop more environmentally friendly sputtering processes, such as using alternative gases or reducing energy consumption.
- Advanced Materials: Sputtering is being used to create next-generation materials, such as 2D materials (e.g., graphene) and nanocomposites, for applications in electronics, energy storage, and more.
By understanding the principles and applications of sputtering, scientists and engineers can harness this powerful technique to innovate and advance technology across various industries.
Summary Table:
Aspect | Details |
---|---|
Definition | High-energy particles bombard a target, ejecting atoms or molecules. |
Mechanism | Ions transfer kinetic energy to surface atoms, enabling ejection. |
Natural Occurrence | Occurs in space, contributing to cosmic dust and spacecraft corrosion. |
Applications | Thin film deposition, surface modification, and materials research. |
Vacuum Requirement | Ensures precise control over film deposition and composition. |
Types | DC, RF, and magnetron sputtering for different materials and applications. |
Advantages | Precision, versatility, and uniformity in film deposition. |
Challenges | High cost, complexity, and material limitations. |
Future Trends | Green sputtering and advanced materials like graphene and nanocomposites. |
Learn how sputtering can revolutionize your research or manufacturing process—contact us today for expert guidance!