Three-plate molds are specialized tools used in injection molding to produce complex parts, particularly those that require precise gate locations or are difficult to fill from the outer edges. These molds are especially useful for round parts or components where traditional two-plate molds may not provide optimal filling or gate placement. The three-plate design allows for more flexibility in gate positioning, often resulting in better part quality and reduced post-processing. However, this comes at a higher cost due to the complexity of the mold and the potential need for hot runner systems to further optimize gate placement.
Key Points Explained:
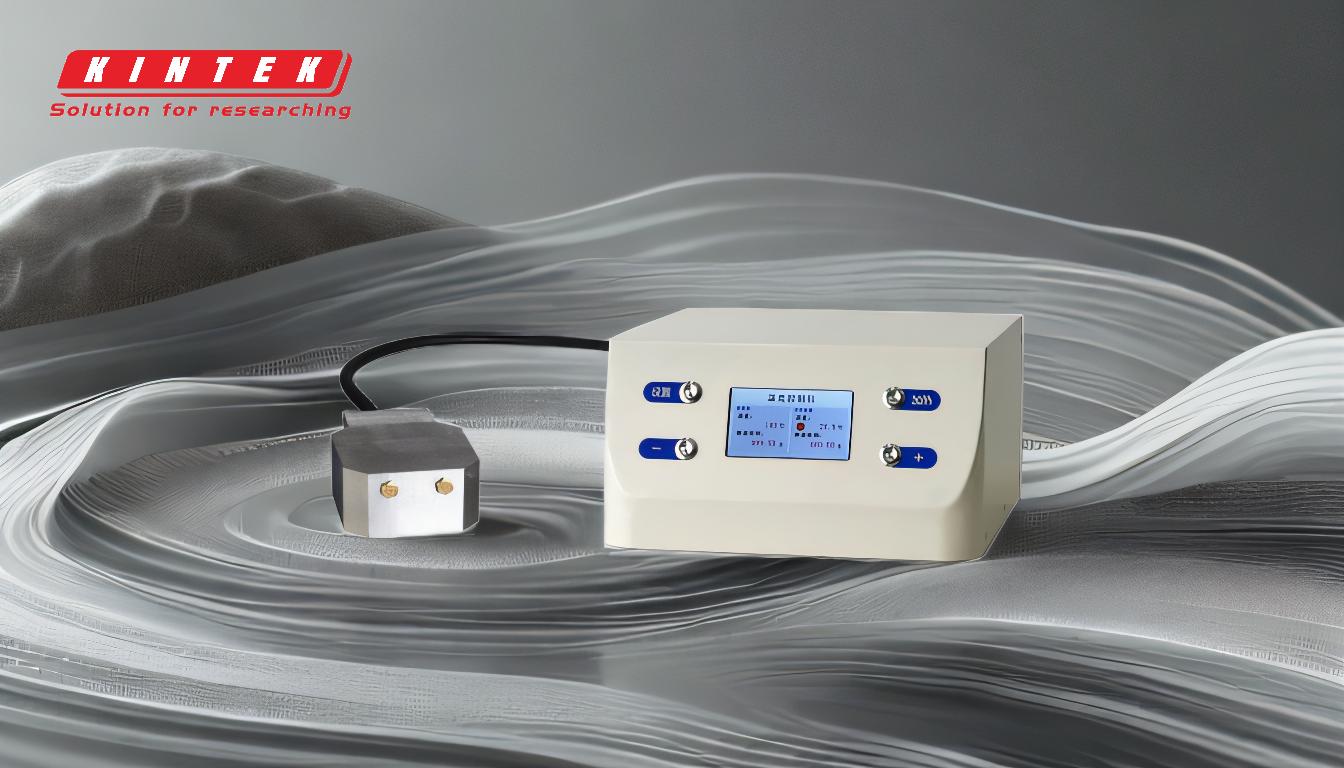
-
Definition and Structure of Three-Plate Molds:
- Three-plate molds consist of three main plates: the cavity plate, the runner plate, and the core plate. This design allows for the separation of the runner system from the part, enabling more precise control over the injection process.
- The additional plate provides space for the runner system, which can be ejected separately from the part, reducing waste and improving efficiency.
-
Applications in Round Parts:
- Three-plate molds are particularly well-suited for round parts, where gate placement on the outer edges may lead to uneven filling or cosmetic defects.
- The ability to place gates at optimal locations within the part ensures more uniform filling and better overall part quality.
-
Challenging Filling Scenarios:
- For parts that are difficult to fill from the outer edges, three-plate molds offer a solution by allowing gates to be placed in more strategic locations.
- This is especially important for parts with complex geometries or thin walls, where traditional gate placement might lead to incomplete filling or warping.
-
Optimal Gate Location:
- The three-plate design provides greater flexibility in gate placement, which can lead to improved part aesthetics and reduced need for secondary operations like trimming.
- Hot runner systems can be integrated with three-plate molds to further optimize gate location, although this increases the overall cost.
-
Cost Considerations:
- While three-plate molds offer significant advantages in terms of part quality and flexibility, they are more expensive to manufacture and maintain compared to two-plate molds.
- The complexity of the mold design and the potential need for hot runner systems contribute to the higher cost, which must be weighed against the benefits for each specific application.
-
Advantages Over Two-Plate Molds:
- Three-plate molds provide better control over the injection process, leading to higher-quality parts with fewer defects.
- The ability to separate the runner system from the part reduces waste and can lead to cost savings in material usage over time.
-
Disadvantages and Limitations:
- The increased complexity and cost of three-plate molds may not be justified for simpler parts or high-volume production where two-plate molds are sufficient.
- Maintenance and operation of three-plate molds can be more challenging, requiring skilled technicians and specialized equipment.
In summary, three-plate molds are a valuable tool in injection molding for producing complex parts, particularly those that are round or difficult to fill from the outer edges. They offer greater flexibility in gate placement and improved part quality, but these benefits come at a higher cost and increased complexity. For applications where precision and part quality are paramount, three-plate molds can be an excellent choice, provided the additional costs are justified.
Summary Table:
Key Aspect | Details |
---|---|
Structure | Consists of three plates: cavity, runner, and core plates. |
Applications | Ideal for round parts and challenging filling scenarios. |
Gate Placement | Allows flexible and optimal gate positioning for better part quality. |
Cost | Higher due to complexity and potential need for hot runner systems. |
Advantages | Better control, reduced waste, and improved part quality. |
Limitations | Higher cost and complexity, not ideal for simpler parts or high-volume use. |
Ready to optimize your injection molding process? Contact us today to learn more about three-plate molds!