The average particle size produced by a ball mill is not a fixed value but depends on several factors, including the size and density of the grinding balls, the grinding time, the hardness of the material being ground, the rotation speed of the mill, and the feed rate. Smaller grinding balls and longer grinding times generally result in smaller particle sizes. The final particle size is also influenced by the number of grinding cycles and the residence time of the material in the mill. Therefore, the average particle size can vary significantly based on the operational parameters and the material properties.
Key Points Explained:
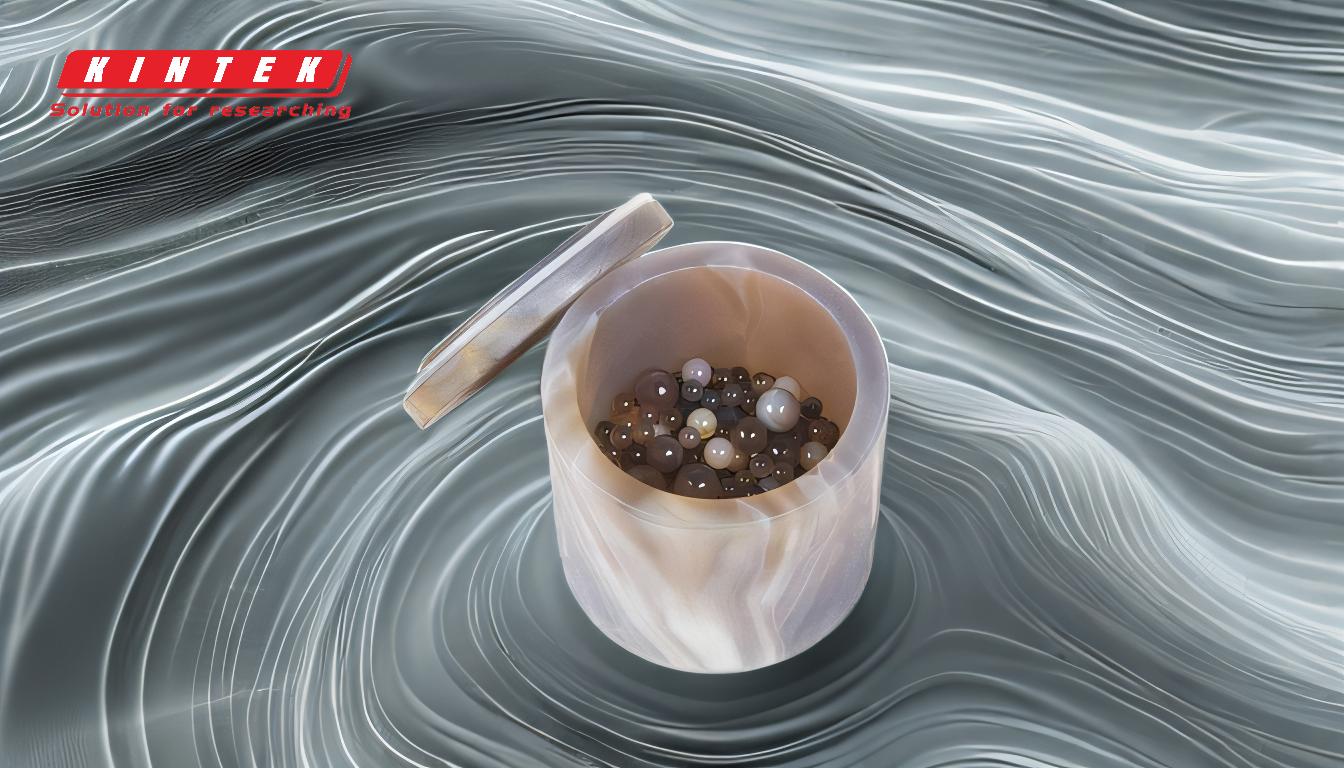
-
Dependence on Grinding Ball Size and Density:
- Smaller balls are more effective at producing finer particles because they have a higher surface area-to-volume ratio, allowing for more contact points with the material being ground.
- The density of the balls also plays a role; denser balls can impart more energy to the material, leading to more effective grinding.
-
Influence of Grinding Time:
- Longer grinding times allow for more collisions between the balls and the material, leading to greater size reduction.
- However, there is a point of diminishing returns where further grinding may not significantly reduce particle size but could lead to overheating or degradation of the material.
-
Material Hardness and Nature:
- Harder materials require more energy to grind, which can be achieved by using denser balls or increasing the grinding time.
- The nature of the material, such as its brittleness or plasticity, also affects how easily it can be ground down.
-
Rotation Speed of the Mill:
- The rotation speed determines the kinetic energy of the balls. Higher speeds can lead to more energetic collisions, which are more effective at breaking down particles.
- However, excessively high speeds can cause the balls to centrifuge, reducing their effectiveness.
-
Feed Rate and Level in the Vessel:
- A higher feed rate can lead to a coarser grind because there is less time for each particle to be ground.
- The level of material in the vessel also affects the grinding efficiency; too much material can cushion the impact of the balls, while too little can lead to inefficient grinding.
-
Residence Time and Grinding Cycles:
- The residence time of the material in the mill chamber is crucial; longer residence times generally result in finer particles.
- Multiple grinding cycles can further reduce particle size, but this must be balanced against the energy and time costs.
-
Specific Surface Area:
- The final particle size is often characterized by its specific surface area, which increases as the particle size decreases.
- This is particularly important in applications where surface area is critical, such as in catalysis or chemical reactions.
In summary, the average particle size from a ball mill is highly variable and depends on a complex interplay of factors. Understanding these factors allows for the optimization of the milling process to achieve the desired particle size for specific applications.
Summary Table:
Factor | Impact on Particle Size |
---|---|
Grinding Ball Size & Density | Smaller, denser balls produce finer particles due to higher surface area and energy transfer. |
Grinding Time | Longer grinding times reduce particle size but may reach diminishing returns. |
Material Hardness | Harder materials require more energy and time to achieve finer particles. |
Mill Rotation Speed | Higher speeds increase collision energy but may cause centrifuge effects at excessive levels. |
Feed Rate | Higher feed rates result in coarser particles due to reduced grinding time per particle. |
Residence Time & Cycles | Longer residence and multiple cycles yield finer particles but increase energy and time costs. |
Specific Surface Area | Smaller particles increase surface area, critical for applications like catalysis. |
Optimize your ball milling process for precise particle size—contact our experts today!