The ball ratio for ball milling, often referred to as the ball-to-powder ratio (BPR), is a critical parameter that influences the efficiency and outcome of the milling process. The BPR is defined as the ratio of the mass of the grinding balls to the mass of the powder being milled. A common BPR used in mechanical milling processes is 7:1, meaning that for every 1 part of powder, 7 parts of grinding balls are used. This ratio can vary depending on the specific requirements of the milling process, such as the desired particle size, the nature of the grinding material, and the milling conditions. Factors like the size, density, and number of balls, as well as the hardness of the grinding material, also play significant roles in determining the optimal BPR.
Key Points Explained:
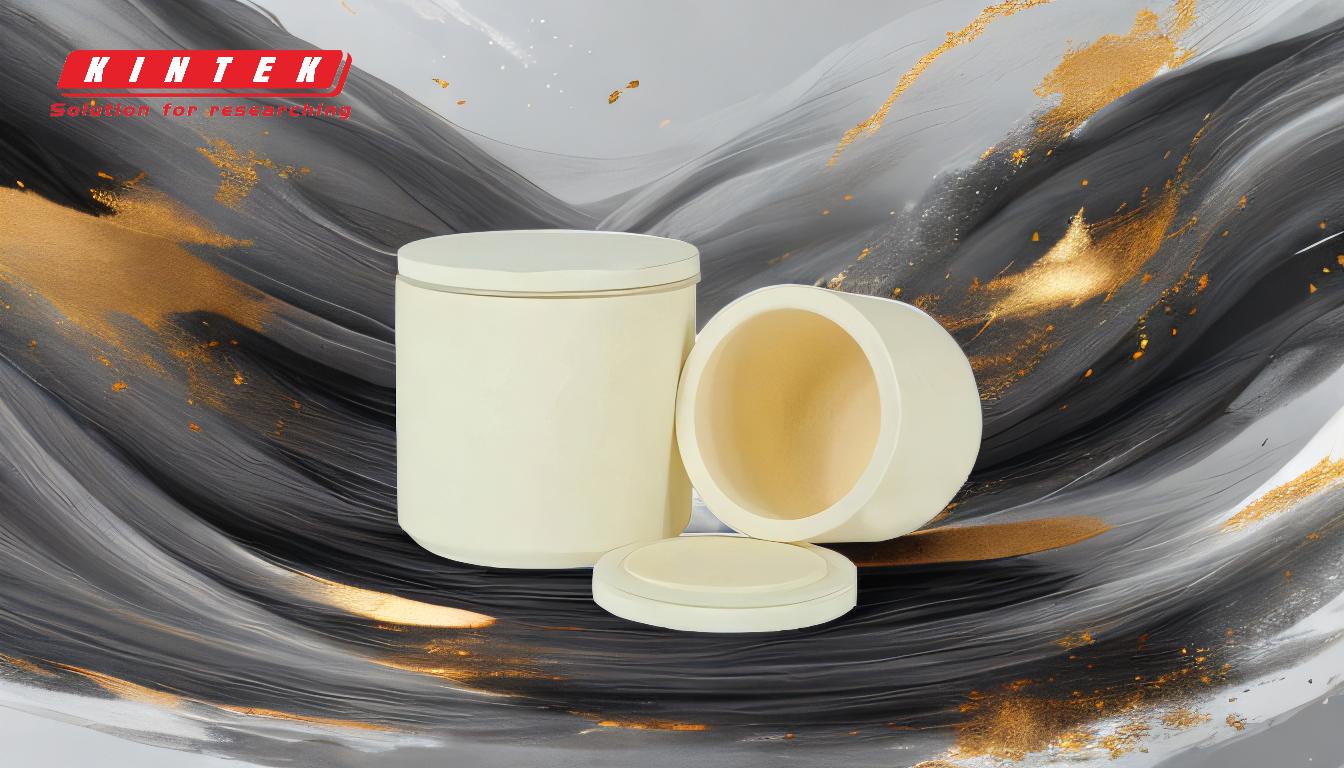
-
Definition of Ball-to-Powder Ratio (BPR):
- The BPR is the ratio of the mass of grinding balls to the mass of the powder being milled. It is a crucial parameter in ball milling as it directly affects the efficiency and outcome of the milling process.
-
Common BPR Values:
- A commonly used BPR in mechanical milling is 7:1. This means that for every 1 part of powder, 7 parts of grinding balls are used. This ratio is often chosen to achieve a balance between effective grinding and preventing excessive wear on the milling equipment.
-
Influence of BPR on Milling Efficiency:
- The BPR affects the degree of milling, which is influenced by several factors including the residence time of the material in the mill chamber, the size, density, and number of balls, the hardness of the grinding material, the feed rate, and the rotation speed of the cylinder. A higher BPR generally leads to more effective grinding but may also increase wear on the milling equipment.
-
Effect of Ball Size and Grinding Time:
- Smaller balls and longer grinding times are generally required to produce smaller particles. The size of the balls and the duration of milling are important considerations when determining the optimal BPR for a specific application.
-
Processes Involved in Ball Milling:
- Ball milling involves several processes such as the flattening of powder particles, welding of powder particles, formation of layered structures, deformation of the layered structure, and formation of nanoparticles. The BPR can influence these processes, affecting the final properties of the milled powder.
-
Considerations for Selecting BPR:
- When selecting the appropriate BPR, it is important to consider the specific requirements of the milling process, including the desired particle size, the nature of the grinding material, and the milling conditions. The optimal BPR may vary depending on these factors.
-
Impact of Material Properties:
- The hardness and other properties of the grinding material can influence the choice of BPR. Harder materials may require a higher BPR to achieve effective grinding, while softer materials may require a lower BPR to prevent excessive wear on the milling equipment.
-
Role of Rotation Speed and Feed Rate:
- The rotation speed of the cylinder and the feed rate of the material into the mill chamber also play significant roles in determining the optimal BPR. Higher rotation speeds and feed rates may require adjustments to the BPR to maintain effective grinding.
In summary, the ball-to-powder ratio is a critical parameter in ball milling that influences the efficiency and outcome of the milling process. A common BPR of 7:1 is often used, but the optimal ratio can vary depending on factors such as the desired particle size, the nature of the grinding material, and the milling conditions. Careful consideration of these factors is essential when selecting the appropriate BPR for a specific application.
Summary Table:
Key Factor | Description |
---|---|
Ball-to-Powder Ratio (BPR) | Ratio of grinding ball mass to powder mass. Common BPR is 7:1. |
Influencing Factors | Ball size, density, hardness, rotation speed, feed rate, and material properties. |
Optimal BPR | Varies based on desired particle size, material type, and milling conditions. |
Impact on Milling | Higher BPR improves grinding efficiency but may increase equipment wear. |
Particle Size Control | Smaller balls and longer grinding times produce finer particles. |
Need help determining the best ball-to-powder ratio for your milling process? Contact our experts today!