Pyrolysis oil, also known as bio-oil, is a complex liquid product derived from the pyrolysis of biomass. Unlike conventional petroleum-based fuels, pyrolysis oil has unique properties such as high oxygen content, low volatility, and thermal instability, which make its boiling behavior distinct. The boiling point of pyrolysis oil is not a single value but rather a range due to its complex mixture of oxygenated organic compounds, water, and polymers. The oil's composition, which includes low molecular weight compounds like acetic acid and high molecular weight compounds like phenols, contributes to a wide boiling range. Additionally, the high water content (20-30 wt-%) and tendency for polymerization further complicate its boiling characteristics. Understanding these properties is crucial for equipment design and applications involving pyrolysis oil.
Key Points Explained:
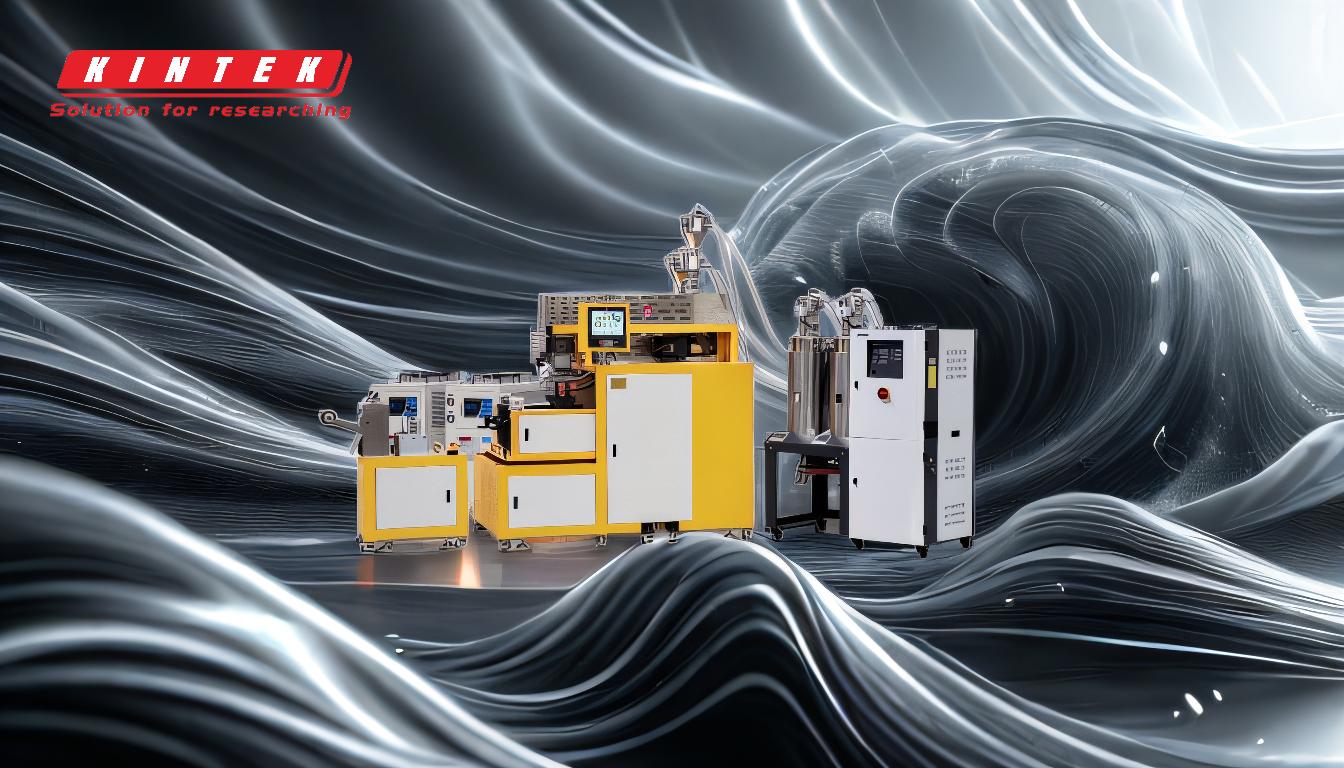
-
Complex Composition of Pyrolysis Oil
- Pyrolysis oil is a mixture of oxygenated organic compounds, polymers, and water.
- It contains up to 40% oxygen by weight, which significantly impacts its physical and chemical properties.
- The oil includes low molecular weight compounds (e.g., formaldehyde, acetic acid) and high molecular weight compounds (e.g., phenols, anhydrosugars), leading to a wide range of boiling points.
-
Boiling Point Range
- Unlike pure substances, pyrolysis oil does not have a single boiling point. Instead, it exhibits a boiling range due to its complex composition.
- The presence of water (20-30 wt-%) lowers the initial boiling point, as water boils at 100°C (212°F) under standard conditions.
- The oxygenated organic compounds and polymers contribute to higher boiling points, with some components boiling at temperatures well above 200°C (392°F).
-
Thermal Instability and Polymerization
- Pyrolysis oil is thermally unstable, meaning it can degrade or polymerize when heated.
- This instability makes it difficult to define a precise boiling point, as the oil may undergo chemical changes before fully vaporizing.
- Polymerization reactions can increase the viscosity and molecular weight of the oil, further altering its boiling behavior.
-
Impact of High Oxygen Content
- The high oxygen content in pyrolysis oil reduces its volatility compared to conventional fossil fuels.
- This low volatility means that pyrolysis oil does not vaporize easily, contributing to its wide boiling range.
-
Practical Implications for Equipment Design
- The wide boiling range and thermal instability of pyrolysis oil require specialized equipment for handling and processing.
- For example, pumps and atomizers must be designed to accommodate the oil's high viscosity and potential for polymerization.
- The presence of corrosive compounds (e.g., acetic acid) also necessitates the use of corrosion-resistant materials in equipment.
-
Comparison to Conventional Fuels
- Unlike diesel or light fuel oil, which have relatively narrow boiling ranges, pyrolysis oil's boiling behavior is less predictable.
- The oil's high density (1.2 g/ml) and lower energy content on a weight basis further differentiate it from traditional fuels.
-
Applications and Handling
- Pyrolysis oil is used as a fuel in boilers and furnaces, but its unique properties require careful handling to avoid issues like clogging or equipment damage.
- The oil's tendency to polymerize over time means it must be used or processed relatively quickly after production.
In summary, the boiling point of pyrolysis oil is not a fixed value but rather a range influenced by its complex composition, high water content, and thermal instability. Understanding these factors is essential for effectively utilizing pyrolysis oil in various applications and designing equipment to handle its unique properties.
Summary Table:
Key Aspect | Details |
---|---|
Composition | Mixture of oxygenated compounds, polymers, and water (20-30 wt-%). |
Boiling Range | 100°C (212°F) to above 200°C (392°F) due to water and organic compounds. |
Thermal Instability | Prone to degradation and polymerization when heated. |
Oxygen Content | Up to 40% by weight, reducing volatility and increasing boiling range. |
Equipment Design | Requires corrosion-resistant materials and specialized handling. |
Applications | Used in boilers and furnaces, but requires careful handling and processing. |
Need help with pyrolysis oil applications or equipment design? Contact our experts today!