The capacity of a ball mill refers to the amount of material it can process in a given time, typically measured in tons per hour (t/h) or cubic meters per hour (m³/h). The capacity depends on several factors, including the mill's dimensions, rotational speed, grinding media size, material properties, and the desired fineness of the product. Ball mills are used in various industries, such as mining, cement, and ceramics, to grind materials into fine powders. Understanding the capacity is crucial for selecting the right mill for specific applications, ensuring efficiency, and optimizing production processes.
Key Points Explained:
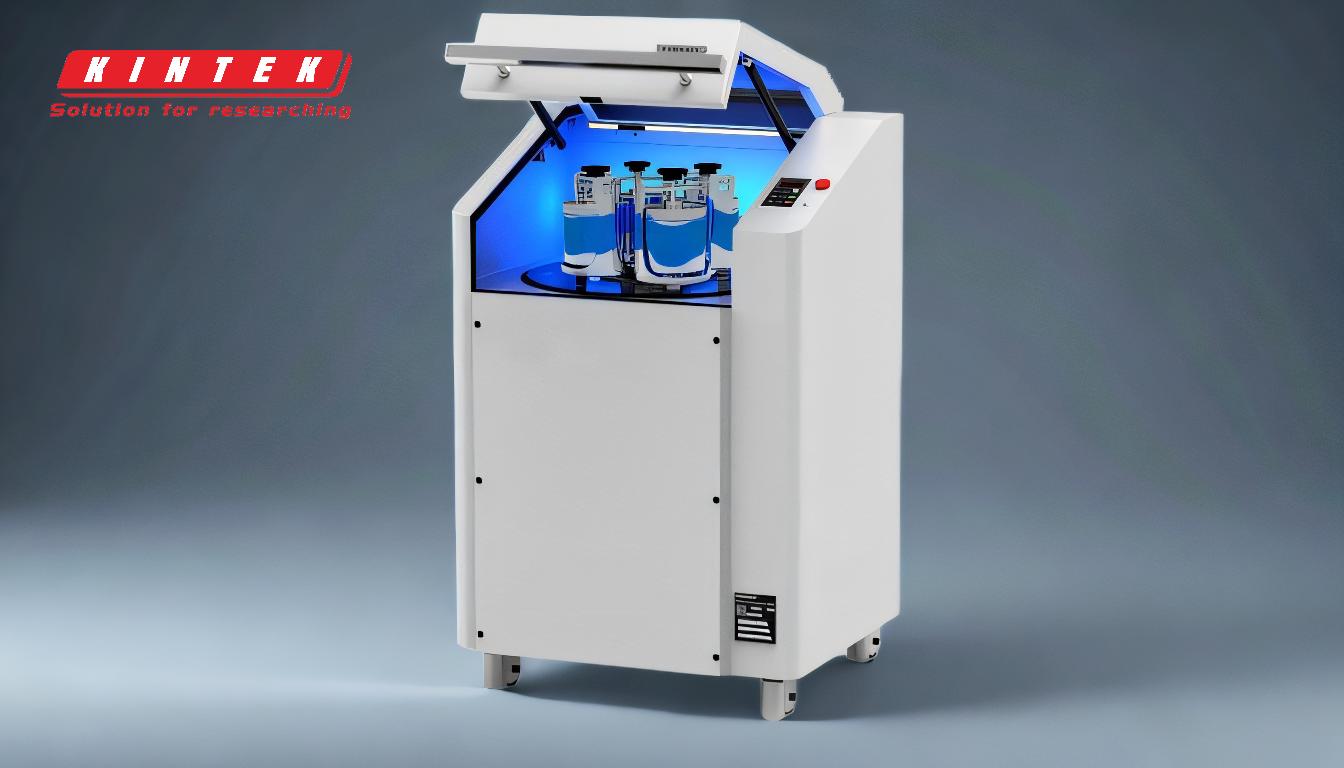
-
Definition of Ball Mill Capacity
- The capacity of a ball mill is the maximum amount of material it can grind in a specific time frame.
- It is influenced by factors such as mill size, speed, grinding media, and material characteristics.
- Capacity is typically expressed in tons per hour (t/h) or cubic meters per hour (m³/h).
-
Factors Affecting Ball Mill Capacity
- Mill Dimensions: Larger mills with greater diameters and lengths can handle more material.
- Rotational Speed: Optimal speed ensures efficient grinding; too slow or too fast can reduce capacity.
- Grinding Media: The size, density, and composition of grinding balls or rods impact grinding efficiency.
- Material Properties: Hardness, moisture content, and feed size of the material affect grinding performance.
- Desired Fineness: Finer grinding requires more time and reduces throughput.
-
Types of Ball Mills and Their Capacities
- Batch Ball Mills: Used for small-scale operations, with capacities ranging from a few kilograms to several tons per batch.
- Continuous Ball Mills: Designed for large-scale production, with capacities ranging from 1 t/h to over 100 t/h.
- Planetary Ball Mills: Used for ultra-fine grinding, with smaller capacities but high precision.
-
Calculating Ball Mill Capacity
- Empirical formulas are often used to estimate capacity based on mill dimensions, speed, and grinding media.
- For example, the formula:
[ Q = 0.104 \times D^2 \times L \times n \times \eta ]
Where:- ( Q ) = Capacity (t/h)
- ( D ) = Mill diameter (m)
- ( L ) = Mill length (m)
- ( n ) = Rotational speed (rpm)
- ( \eta ) = Efficiency factor (typically 0.6–0.8).
-
Practical Considerations for Purchasers
- Application Requirements: Match the mill capacity to the production needs of the industry (e.g., mining, cement, ceramics).
- Energy Efficiency: Higher-capacity mills may consume more power; balance capacity with energy costs.
- Maintenance and Durability: Ensure the mill can handle the required capacity without excessive wear or downtime.
- Cost-Effectiveness: Evaluate the total cost of ownership, including purchase price, operating costs, and maintenance.
-
Industry Examples
- Mining: Ball mills with capacities of 50–100 t/h are common for grinding ores.
- Cement Production: Large ball mills with capacities exceeding 200 t/h are used for clinker grinding.
- Ceramics: Smaller ball mills with capacities of 1–10 t/h are used for fine grinding of raw materials.
By understanding these key points, purchasers can make informed decisions when selecting a ball mill, ensuring it meets their production requirements while optimizing efficiency and cost-effectiveness.
Summary Table:
Factor | Impact on Capacity |
---|---|
Mill Dimensions | Larger mills handle more material. |
Rotational Speed | Optimal speed ensures efficient grinding. |
Grinding Media | Size, density, and composition affect grinding efficiency. |
Material Properties | Hardness, moisture, and feed size influence performance. |
Desired Fineness | Finer grinding reduces throughput. |
Types of Ball Mills | Capacity Range |
Batch Ball Mills | Few kg to several tons per batch. |
Continuous Ball Mills | 1 t/h to over 100 t/h. |
Planetary Ball Mills | Smaller capacities, high precision. |
Ready to optimize your grinding process? Contact us today to find the perfect ball mill for your needs!