Ball milling is a mechanical process used to grind materials into fine powders or nanoparticles. It involves the use of a rotating cylindrical shell filled with grinding media (balls) made of materials like steel, stainless steel, ceramic, or rubber. The chemical composition of ball milling primarily depends on the materials being milled and the composition of the grinding media and lining. The process can lead to phenomena such as particle flattening, welding, and the formation of layered structures or nanoparticles. The equipment's composition, including the lining and grinding media, plays a critical role in determining the outcome of the milling process.
Key Points Explained:
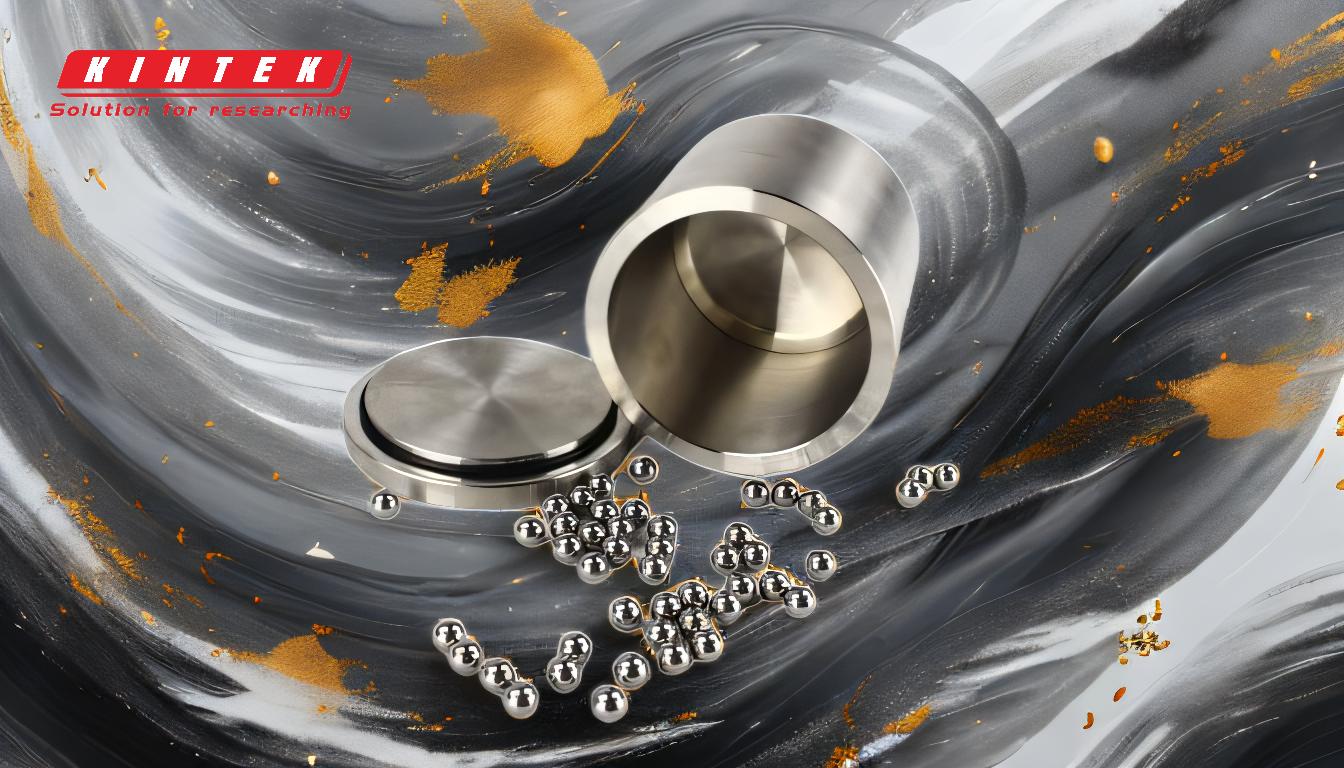
-
Components of a Ball Mill:
- Cylindrical Shell: Typically made of steel or other durable materials, the shell rotates to facilitate the grinding process.
- Grinding Media: Balls made of steel, stainless steel, ceramic, or rubber are used to grind the material. The choice of material depends on the application and the material being milled.
- Lining: The inner surface of the shell is often lined with abrasion-resistant materials like manganese steel or rubber to protect the shell and enhance grinding efficiency.
-
Chemical Composition of Grinding Media:
- Steel Balls: Composed primarily of iron with small amounts of carbon and other alloying elements like chromium or manganese for hardness and durability.
- Stainless Steel Balls: Contain iron, chromium (typically 10-30%), and nickel, providing corrosion resistance and strength.
- Ceramic Balls: Made from materials like alumina (Al₂O₃) or zirconia (ZrO₂), offering high hardness and wear resistance.
- Rubber Balls: Composed of synthetic or natural rubber, used in applications where contamination from metal is a concern.
-
Chemical Composition of Lining Materials:
- Manganese Steel: Contains high levels of manganese (11-14%) and carbon (1-1.4%), providing excellent abrasion resistance.
- Rubber Linings: Made from synthetic or natural rubber, often reinforced with additives for durability and resistance to wear.
-
Process Outcomes and Chemical Interactions:
- Particle Flattening and Welding: The mechanical forces during milling can cause particles to deform and weld together, altering their chemical structure.
- Formation of Layered Structures: Repeated impact and compression can lead to the formation of layered or composite structures.
- Nanoparticle Formation: Prolonged milling can reduce particle size to the nanoscale, potentially altering the material's chemical and physical properties.
-
Factors Influencing Chemical Composition:
- Material Being Milled: The composition of the powder being milled will influence the final product's chemical makeup.
- Grinding Media and Lining: The choice of grinding media and lining materials can introduce trace elements or contaminants into the milled product.
- Milling Environment: The presence of air, inert gases, or liquids can affect oxidation, contamination, or chemical reactions during milling.
By understanding the chemical composition of the ball mill components and the milling process, users can optimize the setup for specific applications, ensuring desired outcomes in terms of particle size, structure, and chemical properties.
Summary Table:
Component | Material | Key Properties |
---|---|---|
Cylindrical Shell | Steel or durable materials | Provides structural integrity and facilitates rotation for grinding. |
Grinding Media | Steel, stainless steel, ceramic, rubber | Determines grinding efficiency and contamination risks based on material choice. |
Lining | Manganese steel, rubber | Protects the shell, enhances abrasion resistance, and improves grinding efficiency. |
Process Outcomes | Particle flattening, welding, nanoparticle formation | Alters particle size, structure, and chemical properties during milling. |
Optimize your ball milling process—contact our experts today for tailored solutions!