The conventional sputtering method is a widely used thin-film deposition technique in which atoms are ejected from a solid target material due to bombardment by high-energy ions. These ejected atoms then deposit onto a substrate, forming a thin film. The process typically involves creating a vacuum environment, introducing an inert gas like argon, ionizing the gas to form a plasma, and using the resulting ions to sputter the target material. This method is highly precise and is commonly used in industries such as semiconductors, optics, and coatings.
Key Points Explained:
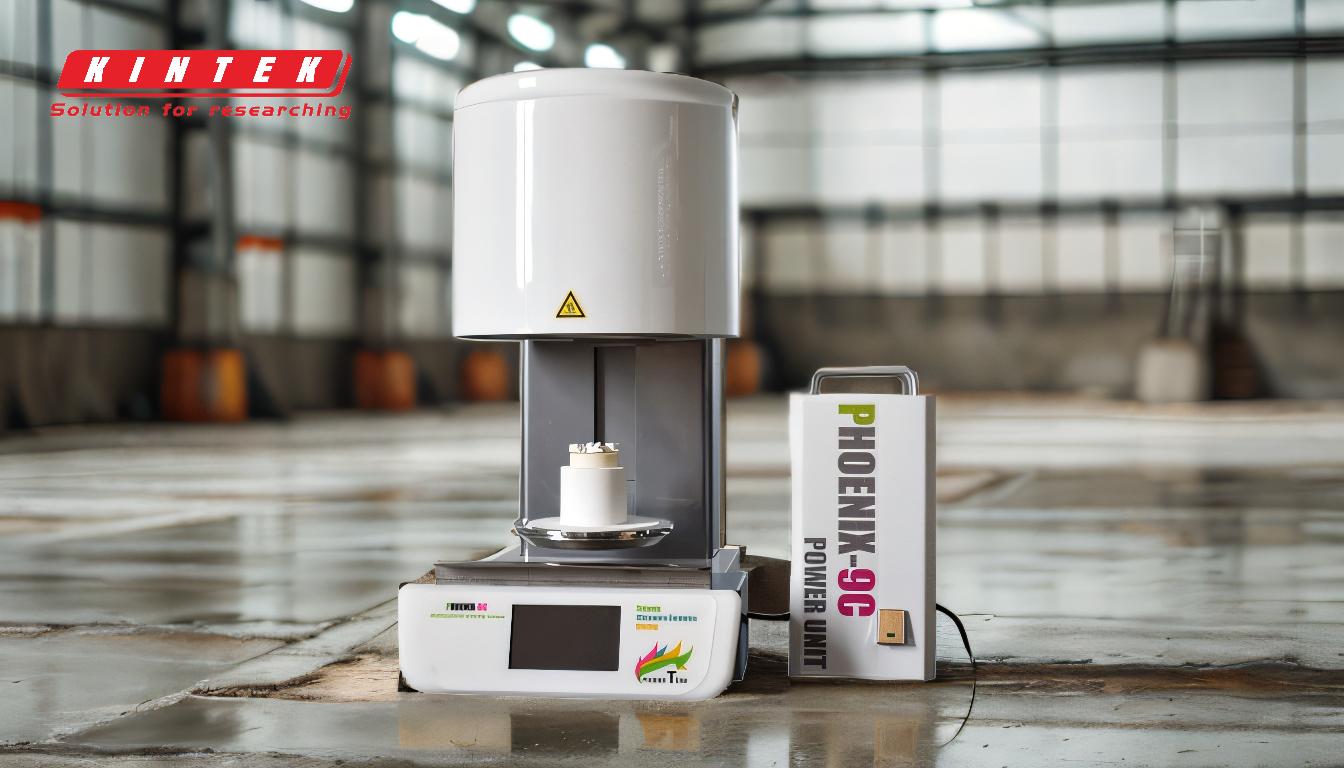
-
Vacuum Environment Creation:
- The process begins by creating a vacuum inside the reaction chamber to eliminate impurities and moisture. This ensures a controlled environment for uniform deposition.
- The pressure is typically reduced to around 1 Pa (0.0000145 psi).
-
Introduction of Inert Gas:
- An inert gas, usually argon, is introduced into the chamber at low pressure. This gas is chosen because it is chemically non-reactive, preventing contamination of the target material.
- The pressure range is typically between 10^-1 to 10^-3 mbar.
-
Plasma Generation:
- A high voltage (3-5 kV) is applied to ionize the argon gas, creating a plasma composed of Ar+ ions.
- The plasma is confined and accelerated around the target using a magnetic field, enhancing the efficiency of the sputtering process.
-
Ion Bombardment and Sputtering:
- The positively charged argon ions are accelerated towards the negatively charged target (cathode).
- When these high-energy ions strike the target, they transfer their energy, causing atoms to be ejected from the target's surface. This phenomenon is known as sputtering.
-
Transport of Sputtered Atoms:
- The ejected atoms travel through the low-pressure environment and deposit onto the substrate.
- This transport occurs in a region of reduced pressure, ensuring minimal interference and contamination.
-
Thin Film Formation:
- The sputtered atoms condense on the substrate, forming a thin film.
- The film's properties, such as thickness and uniformity, can be precisely controlled by adjusting parameters like gas pressure, voltage, and target-substrate distance.
-
Heating (Optional):
- In some cases, the chamber is heated to temperatures ranging from 150°C to 750°C (302°F to 1382°F) to improve the adhesion and quality of the deposited film.
-
Common Sputtering Techniques:
- Magnetron Sputtering: Uses a magnetic field to enhance plasma density and sputtering efficiency.
- DC Sputtering: Direct current is used to generate the plasma and sputter the target material.
- RF Sputtering: Radio frequency is used to ionize the gas, suitable for insulating materials.
- Reactive Sputtering: Involves introducing a reactive gas (e.g., oxygen or nitrogen) to form compound films.
-
Applications:
- The conventional sputtering method is used in various industries, including:
- Semiconductors: For depositing thin films in integrated circuits.
- Optics: For creating anti-reflective and reflective coatings.
- Coatings: For wear-resistant and decorative coatings on tools and components.
- The conventional sputtering method is used in various industries, including:
By following these steps, the conventional sputtering method ensures precise and high-quality thin film deposition, making it a cornerstone in modern manufacturing and material science.
Summary Table:
Key Steps | Details |
---|---|
Vacuum Environment | Pressure reduced to ~1 Pa for impurity-free, controlled deposition. |
Inert Gas Introduction | Argon gas introduced at 10^-1 to 10^-3 mbar for contamination prevention. |
Plasma Generation | 3-5 kV voltage ionizes argon, forming Ar+ plasma for efficient sputtering. |
Ion Bombardment | Ar+ ions strike the target, ejecting atoms onto the substrate. |
Thin Film Formation | Sputtered atoms condense, forming uniform films with precise control. |
Heating (Optional) | Chamber heated to 150°C–750°C for improved film adhesion and quality. |
Common Techniques | Magnetron, DC, RF, and reactive sputtering for various material needs. |
Applications | Semiconductors, optics, and wear-resistant coatings. |
Discover how the conventional sputtering method can elevate your manufacturing process—contact us today for expert guidance!