The design of a pyrolysis reactor is a complex process that involves several critical components and considerations to ensure efficient and safe operation. Key features include the use of high-quality materials like boiler steel Q345R for durability and heat transfer efficiency, advanced insulation techniques, and specialized welding technologies to prevent defects. The reactor system typically consists of a feeding system, pyrolysis reactor, discharging system, syn-gas recycling system, and de-dusting system, each playing a vital role in the overall process. Additionally, factors such as the type of biomass, pyrolysis temperature, and heating rate significantly influence the yield and composition of pyrolysis products. The design also incorporates safety measures like ultrasonic flaw detection and dynamic balance tests to ensure long-term stability and reliability.
Key Points Explained:
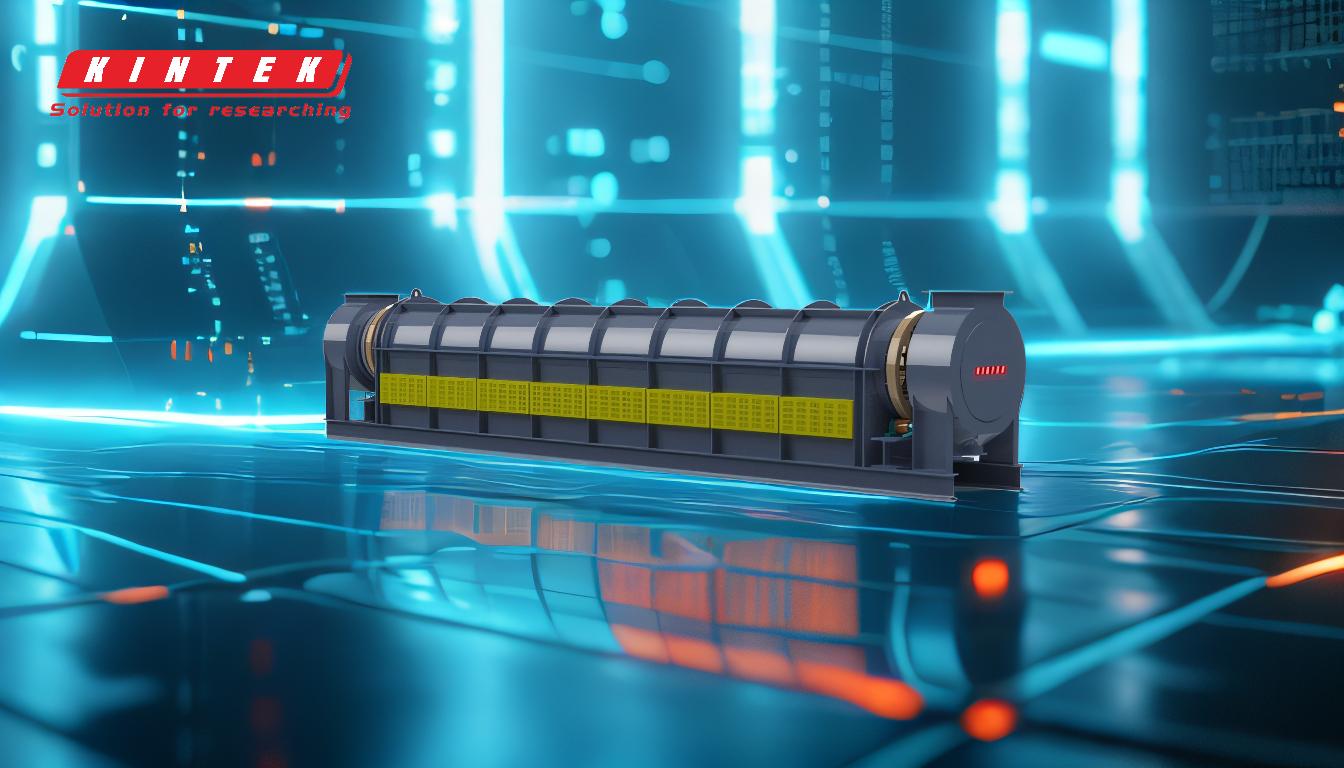
-
Material Selection and Insulation:
- The reactor is constructed using special boiler steel Q345R, known for its excellent heat transfer efficiency and longevity.
- Insulation is enhanced with a 16mm thick reactor body and door, a 12mm thick inner spiral plate, and 80mm thick aluminum silicate refractory fiber cotton, ensuring minimal heat loss and maintaining high internal temperatures.
-
Welding and Safety Measures:
- Special welding technology is employed to ensure full and neat welds, avoiding defects that could compromise the reactor's integrity.
- Ultrasonic flaw detection tests are conducted to identify any potential weaknesses or defects in the welding, ensuring the reactor's safety and durability.
-
High-Temperature Resistance and Durability:
- The reactor is designed with high-temperature resistant rollers to withstand the extreme conditions of pyrolysis.
- An inverter motor combined with a frequency converter allows for adjustable speed, improving efficiency and control over the pyrolysis process.
-
Structural Stability and Precision:
- A large ring gear structure is incorporated to provide stability and precision during operation.
- Dynamic balance tests are performed on the reducer to ensure longevity and stability, reducing vibrations and wear over time.
-
System Components:
- The pyrolysis system includes a feeding system, pyrolysis reactor, discharging system, syn-gas recycling system, and de-dusting system.
- The feeding system delivers raw materials to the reactor automatically in a fully sealed manner, preventing contamination and ensuring consistent operation.
- The discharging system transports carbon black into a tank with a water-cooling pipe, facilitating safe and efficient removal of by-products.
- The syn-gas recycling system recycles combustible gas from the reactor, which can be used to heat the reactor directly, improving energy efficiency.
- The de-dusting system purifies the emission gas to meet stringent EU emission standards, ensuring environmental compliance.
-
Influencing Factors on Pyrolysis Products:
- The yield and composition of pyrolysis products are influenced by factors such as the type of biomass, pretreatment conditions, pyrolysis temperature, heating rate, and reactor type.
- These factors must be carefully controlled and optimized to achieve the desired product quality and yield.
-
Fluidised Bed Reactor Design:
- Key design considerations for the fluidised bed reactor include the operating velocity, height, diameter, wall thickness, and distributor plate design.
- These parameters are determined based on the density and viscosity of the components at the specified temperature and pressure of 101,325 kPa.
- The design assumes that char particles react immediately to form flue gases in the combustor and that wood chips instantly pyrolyse to form non-condensable gases (NCG).
-
Semi-Batch Reactor Design:
- A semi-batch pyrolysis reactor allows for the substrate or reactants to be fed into the vessel in batches at intervals during the pyrolysis process.
- This design provides flexibility in controlling the reaction conditions and can be beneficial for processing materials that require gradual feeding or specific reaction times.
In summary, the design of a pyrolysis reactor is a multifaceted process that requires careful consideration of materials, insulation, welding techniques, safety measures, and system components. The reactor must be capable of withstanding high temperatures, ensuring structural stability, and efficiently managing the pyrolysis process to produce high-quality products while meeting environmental standards.
Summary Table:
Key Component | Description |
---|---|
Material Selection | Boiler steel Q345R for durability and heat transfer efficiency. |
Insulation | 16mm thick reactor body, 12mm inner spiral plate, 80mm refractory fiber cotton. |
Welding & Safety | Special welding technology, ultrasonic flaw detection for durability. |
System Components | Feeding, discharging, syn-gas recycling, and de-dusting systems. |
High-Temperature Design | High-temperature resistant rollers, inverter motor for adjustable speed. |
Structural Stability | Large ring gear structure, dynamic balance tests for longevity. |
Influencing Factors | Biomass type, pyrolysis temperature, heating rate, and reactor type. |
Need a custom pyrolysis reactor design? Contact our experts today for tailored solutions!