Ball mills and bead mills are both grinding machines used to reduce particle size, but they differ significantly in their design, operation, and applications. A ball mill uses steel balls or rods as grinding media and relies on impact and attrition forces to grind materials into fine powders, typically used for materials like ore, ceramics, and paint. In contrast, a bead mill uses small beads as grinding media and operates by agitating these beads in a slurry, creating strong shear forces and collisions to disperse or grind particles. Bead mills are preferred in industries requiring high production efficiency and fine particle sizes, such as paints, inks, and pharmaceuticals. While ball mills are more suited for coarse grinding, bead mills excel in producing ultra-fine particles and are more efficient for continuous operations.
Key Points Explained:
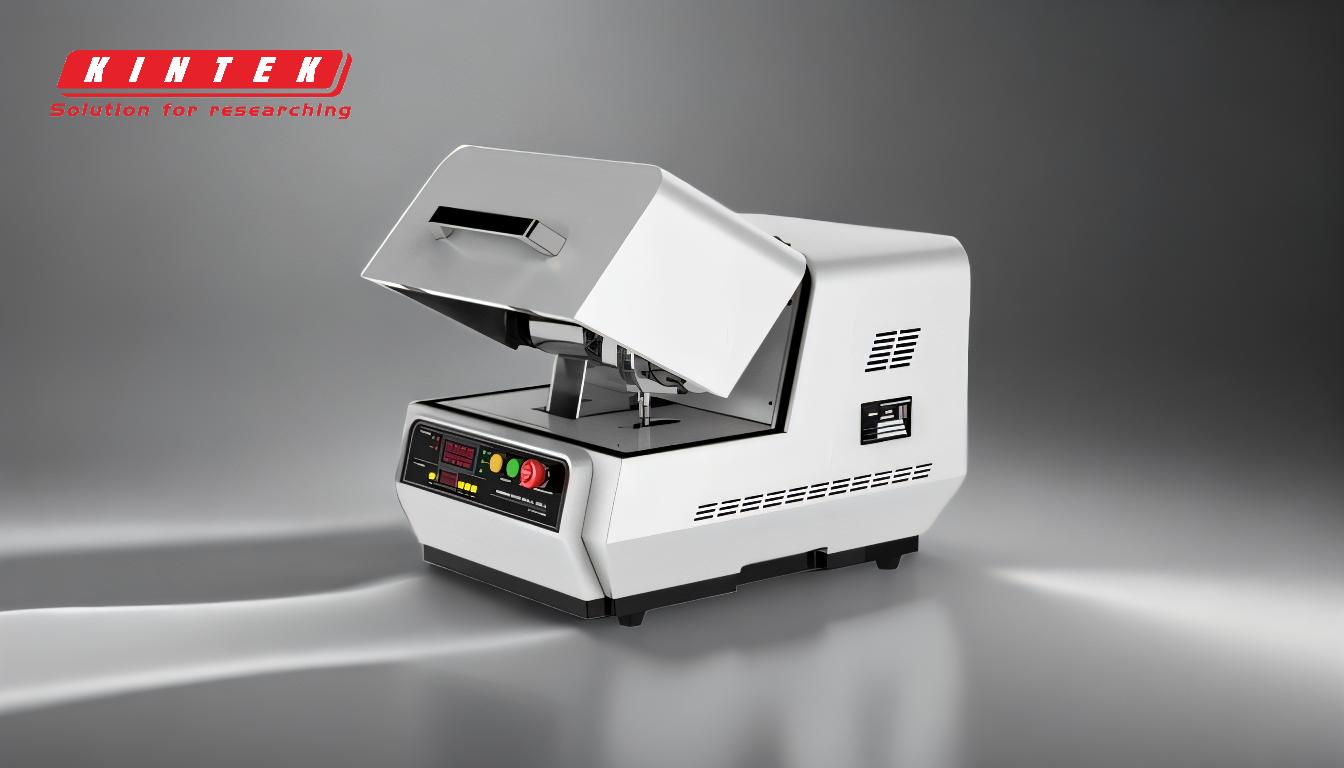
-
Grinding Mechanism:
- Ball Mill: Uses steel balls or rods as grinding media. The grinding process relies on the impact and attrition forces generated by the rotating drum, which causes the balls to collide with the material, breaking it down into finer particles.
- Bead Mill: Uses small beads (often made of glass, ceramic, or steel) as grinding media. The beads are agitated by a rotor, creating strong shear forces and collisions that grind or disperse particles in a slurry.
-
Design and Operation:
- Ball Mill: Typically consists of a rotating cylindrical drum partially filled with grinding media. The material is fed into the drum, and the rotation causes the balls to cascade and grind the material.
- Bead Mill: Features a cylindrical vessel filled with beads and a rotor that agitates the beads. The slurry is pumped through the vessel, and the rotor's motion causes the beads to grind or disperse the particles.
-
Applications:
- Ball Mill: Commonly used for grinding materials like ore, ceramics, and paint into a fine powder. It is suitable for coarse grinding and batch operations.
- Bead Mill: Preferred in industries requiring fine particle sizes and high production efficiency, such as paints, inks, and pharmaceuticals. It is ideal for continuous operations and producing ultra-fine particles.
-
Efficiency and Particle Size:
- Ball Mill: More suited for coarse grinding and larger particle sizes. It is less efficient for producing ultra-fine particles compared to bead mills.
- Bead Mill: Highly efficient for producing ultra-fine particles and dispersing particles in a slurry. It is more effective for continuous operations and achieving uniform particle sizes.
-
Installation and Maintenance:
- Ball Mill: Requires a relatively simple setup and maintenance. The grinding media (balls or rods) need periodic replacement, but the overall maintenance is straightforward.
- Bead Mill: Installation and maintenance can vary depending on the design (horizontal or vertical). Horizontal bead mills require more space and effort for slurry and bead recovery, while vertical bead mills are more compact but may require more power and effort for part replacement.
-
Industry Preferences:
- Ball Mill: Widely used in mining, ceramics, and construction industries for grinding raw materials and producing coarse powders.
- Bead Mill: Favored in industries like paints, inks, and pharmaceuticals, where high production efficiency, fine particle sizes, and continuous operations are critical.
By understanding these key differences, equipment and consumable purchasers can make informed decisions based on their specific grinding needs, material characteristics, and industry requirements.
Summary Table:
Aspect | Ball Mill | Bead Mill |
---|---|---|
Grinding Mechanism | Uses steel balls/rods; relies on impact and attrition forces. | Uses small beads; relies on shear forces and collisions in a slurry. |
Design & Operation | Rotating drum with grinding media; suitable for batch operations. | Cylindrical vessel with beads and rotor; ideal for continuous operations. |
Applications | Coarse grinding (ore, ceramics, paint). | Fine particle sizes (paints, inks, pharmaceuticals). |
Efficiency | Less efficient for ultra-fine particles. | Highly efficient for ultra-fine particles and dispersions. |
Maintenance | Simple setup; periodic replacement of grinding media. | Varies by design; horizontal mills require more space, vertical mills more power. |
Industry Preferences | Mining, ceramics, construction. | Paints, inks, pharmaceuticals. |
Need help choosing the right grinding solution? Contact our experts today for personalized advice!