A ball mill and a colloid mill are both grinding machines, but they differ significantly in their design, working principles, and applications. A ball mill uses rotating cylinders filled with grinding media (such as steel balls) to crush and grind materials into fine powders, making it ideal for coarse and medium grinding in industries like mining and ceramics. In contrast, a colloid mill employs high shear forces generated by a rotor-stator mechanism to reduce particle sizes to a colloidal or micron level, making it suitable for emulsifying, homogenizing, and dispersing materials in industries like food, pharmaceuticals, and cosmetics. The key differences lie in their grinding mechanisms, particle size reduction capabilities, and industry-specific applications.
Key Points Explained:
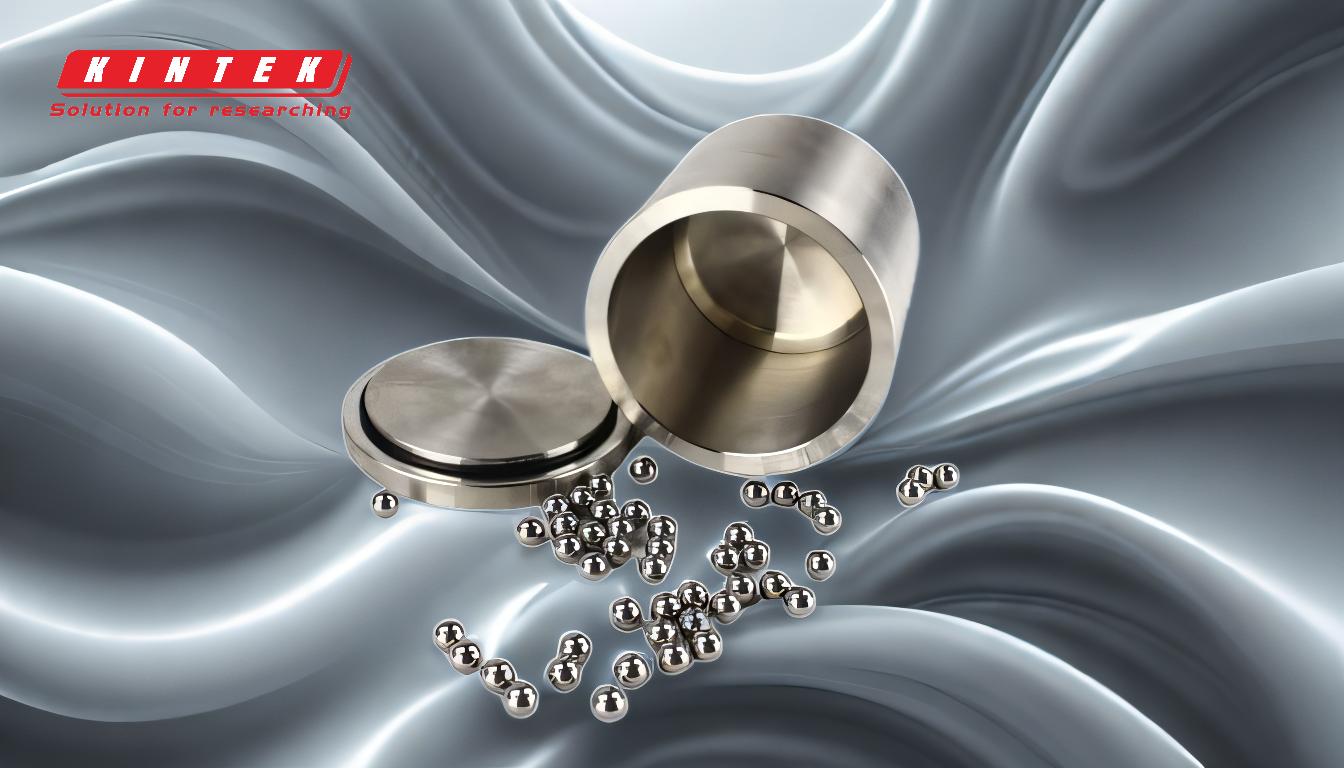
-
Design and Working Principle:
-
Ball Mill:
- Consists of a rotating cylindrical chamber filled with grinding media (e.g., steel balls).
- Materials are crushed and ground through impact and attrition as the cylinder rotates.
- Suitable for dry or wet grinding processes.
-
Colloid Mill:
- Comprises a rotor and stator that create high shear forces.
- Materials are subjected to intense mechanical forces, reducing particle sizes to a colloidal level.
- Primarily used for wet grinding, emulsifying, and homogenizing.
-
Ball Mill:
-
Particle Size Reduction:
-
Ball Mill:
- Produces relatively coarse to medium-sized particles (typically in the range of micrometers to millimeters).
- Ideal for grinding hard and brittle materials.
-
Colloid Mill:
- Capable of producing ultrafine particles, often in the nanometer to micrometer range.
- Designed for creating stable emulsions, suspensions, and dispersions.
-
Ball Mill:
-
Applications:
-
Ball Mill:
- Widely used in mining, cement, ceramics, and metallurgy industries.
- Suitable for grinding ores, minerals, and other hard materials.
-
Colloid Mill:
- Commonly used in food processing (e.g., mayonnaise, peanut butter), pharmaceuticals (e.g., ointments, creams), and cosmetics (e.g., lotions, pastes).
- Ideal for applications requiring fine particle size and uniform dispersion.
-
Ball Mill:
-
Operational Differences:
-
Ball Mill:
- Requires longer processing times to achieve desired particle sizes.
- Can handle larger quantities of material in a single batch.
-
Colloid Mill:
- Operates at high speeds, enabling rapid particle size reduction.
- Typically used for continuous or semi-continuous processes.
-
Ball Mill:
-
Maintenance and Cost:
-
Ball Mill:
- Requires regular maintenance due to wear and tear of grinding media and liners.
- Generally has a lower initial cost but higher operational costs over time.
-
Colloid Mill:
- Lower maintenance requirements due to fewer moving parts.
- Higher initial cost but more efficient for specific applications requiring fine grinding.
-
Ball Mill:
-
Energy Efficiency:
-
Ball Mill:
- Less energy-efficient for fine grinding due to the high energy consumption of rotating heavy cylinders.
-
Colloid Mill:
- More energy-efficient for producing fine and ultrafine particles due to its high shear mechanism.
-
Ball Mill:
By understanding these differences, equipment purchasers can make informed decisions based on their specific grinding or processing needs.
Summary Table:
Aspect | Ball Mill | Colloid Mill |
---|---|---|
Design | Rotating cylinder with grinding media (e.g., steel balls) | Rotor-stator mechanism generating high shear forces |
Particle Size | Coarse to medium (micrometers to millimeters) | Ultrafine (nanometers to micrometers) |
Applications | Mining, cement, ceramics, metallurgy | Food, pharmaceuticals, cosmetics (emulsifying, homogenizing, dispersing) |
Operational Speed | Slower, batch processing | Faster, continuous or semi-continuous processing |
Maintenance | Higher due to wear and tear | Lower due to fewer moving parts |
Energy Efficiency | Less efficient for fine grinding | More efficient for fine and ultrafine particles |
Need help choosing the right grinding machine for your needs? Contact our experts today for personalized advice!