Ball mills and colloidal mills are both grinding equipment, but they differ significantly in their design, working principles, and applications. A ball mill uses rotating balls to grind materials into fine powders, making it suitable for materials like ores, ceramics, and paints. In contrast, a colloidal mill is designed for reducing particle size in suspensions or emulsions, often used in industries like food, pharmaceuticals, and cosmetics. The key differences lie in their mechanisms, operational parameters, and the types of materials they process.
Key Points Explained:
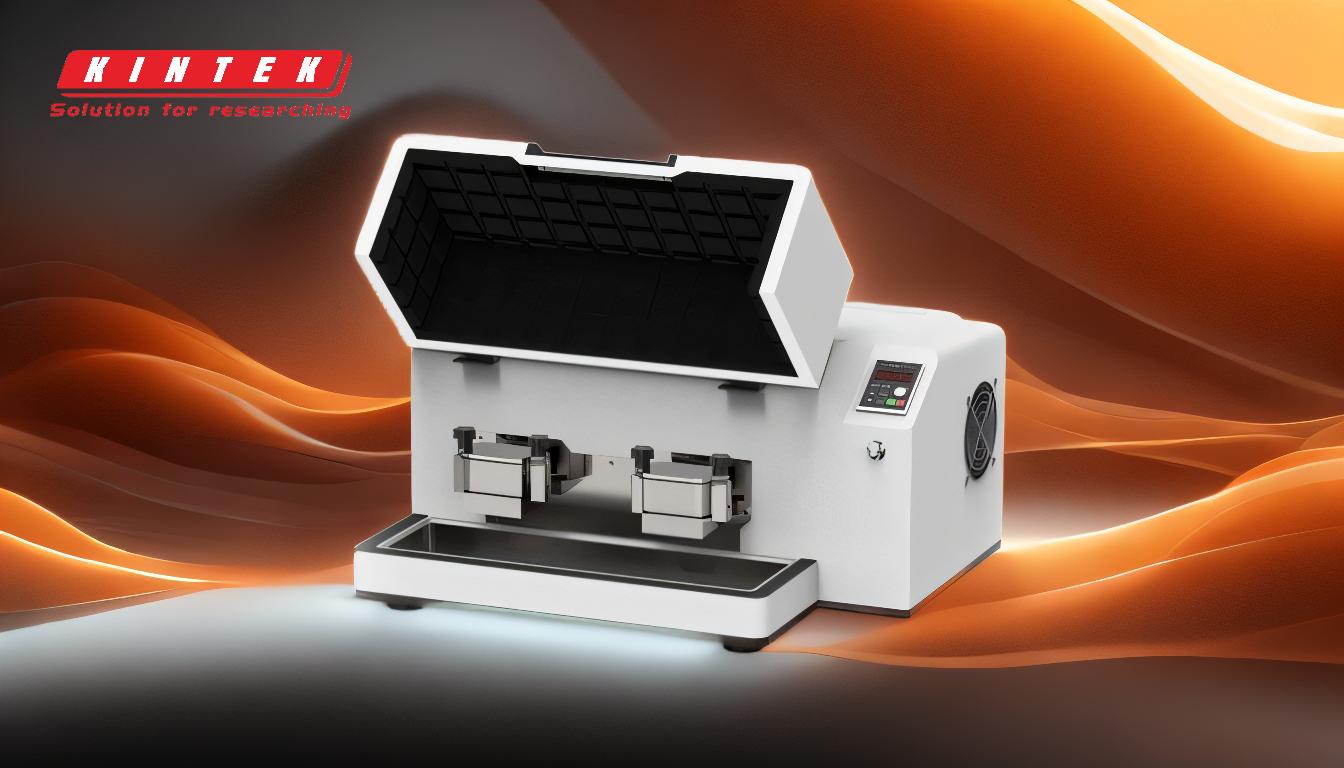
-
Mechanism of Operation:
- Ball Mill: Utilizes rotating balls to grind materials through impact and attrition. The balls cascade and collide with the material, breaking it down into finer particles.
- Colloidal Mill: Employs a rotor-stator mechanism where high shear forces are applied to the material, reducing particle size in suspensions or emulsions. The rotor spins at high speeds, creating a fine dispersion or homogenization.
-
Design and Structure:
- Ball Mill: Typically consists of a cylindrical shell rotating around its axis, partially filled with grinding media (balls). The shell can be horizontal or at a slight angle.
- Colloidal Mill: Features a rotor and stator with very narrow gaps between them. The design ensures high shear forces are applied to the material passing through the gap.
-
Applications:
- Ball Mill: Primarily used in industries like mining (for ore processing), ceramics, and paint manufacturing. It is ideal for grinding hard, brittle materials into fine powders.
- Colloidal Mill: Commonly used in the food industry (for making sauces, emulsions), pharmaceuticals (for drug formulations), and cosmetics (for creams and lotions). It is suitable for reducing particle size in liquid suspensions or emulsions.
-
Material Compatibility:
- Ball Mill: Best suited for dry or wet grinding of hard, brittle materials. It can handle materials like ores, ceramics, and certain chemicals.
- Colloidal Mill: Designed for processing liquid-based materials, including suspensions, emulsions, and pastes. It is not suitable for dry materials.
-
Operational Parameters:
- Ball Mill: Operates at relatively lower speeds compared to colloidal mills. The grinding efficiency depends on the size and density of the balls, as well as the rotational speed of the mill.
- Colloidal Mill: Operates at very high speeds to generate the necessary shear forces. The gap between the rotor and stator is adjustable, allowing control over the final particle size.
-
Final Product Characteristics:
- Ball Mill: Produces fine to ultra-fine powders with a relatively broad particle size distribution. The final product is typically dry or in a slurry form.
- Colloidal Mill: Produces a homogenous mixture with a very fine and uniform particle size distribution. The final product is usually a stable suspension or emulsion.
-
Maintenance and Wear:
- Ball Mill: High wear and tear due to the constant impact and friction between the balls and the material. Regular maintenance is required to replace worn-out balls and liners.
- Colloidal Mill: Lower wear compared to ball mills, but the rotor and stator may still wear over time, especially when processing abrasive materials. Maintenance involves checking and replacing these components as needed.
By understanding these key differences, a purchaser can make an informed decision based on the specific requirements of their application, whether it involves grinding solid materials or homogenizing liquid suspensions.
Summary Table:
Aspect | Ball Mill | Colloidal Mill |
---|---|---|
Mechanism | Rotating balls grind materials through impact and attrition. | Rotor-stator mechanism applies high shear forces for particle size reduction. |
Design | Cylindrical shell with grinding media (balls), horizontal or slightly angled. | Rotor and stator with narrow gaps for high shear force application. |
Applications | Mining, ceramics, paint manufacturing (dry or wet grinding). | Food, pharmaceuticals, cosmetics (liquid suspensions or emulsions). |
Material Compatibility | Hard, brittle materials like ores and ceramics. | Liquid-based materials like suspensions, emulsions, and pastes. |
Operational Parameters | Lower speeds, grinding efficiency depends on ball size and rotation speed. | High speeds, adjustable gap for precise particle size control. |
Final Product | Fine to ultra-fine powders with broad particle size distribution. | Homogeneous mixture with uniform particle size distribution. |
Maintenance | High wear due to impact; requires regular ball and liner replacement. | Lower wear; rotor and stator may need replacement over time. |
Need help choosing the right grinding equipment? Contact our experts today for personalized advice!