Ball mills and attritors are both grinding equipment used in various industries, but they differ significantly in their design, operation, and applications. Ball mills are large, cylindrical devices that use grinding media (balls) to reduce particle size through impact and attrition. They are typically used for coarse grinding and are suitable for large-scale operations. Attritors, on the other hand, are smaller, high-energy grinding devices that use smaller grinding media and rely primarily on agitation and shear forces for particle size reduction. They are more efficient for fine grinding and are often used in laboratory or small-scale production settings. The choice between the two depends on factors like material properties, desired particle size, and production scale.
Key Points Explained:
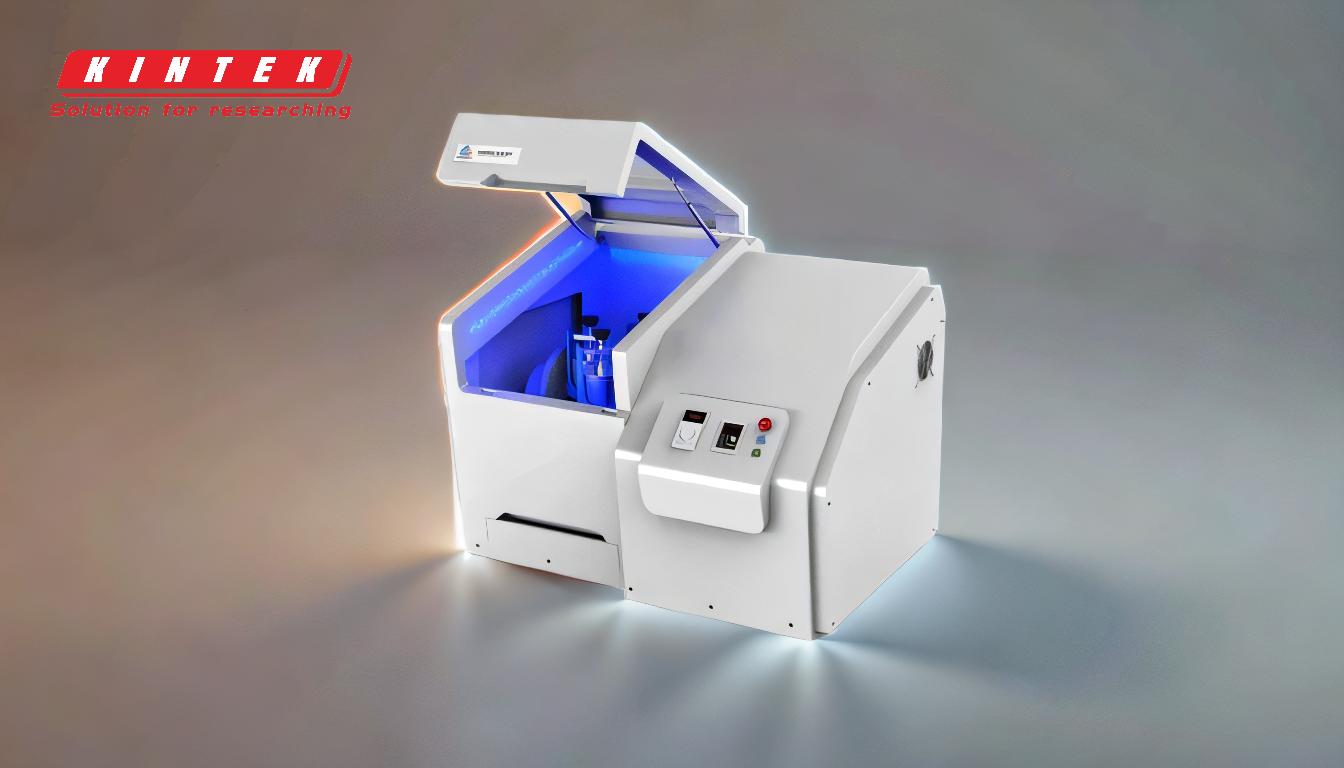
-
Design and Structure:
- Ball Mill: A ball mill consists of a large, rotating cylindrical shell partially filled with grinding media (steel or ceramic balls). The rotation of the shell causes the balls to cascade and impact the material, leading to size reduction.
- Attritor: An attritor is a vertical or horizontal vessel filled with grinding media (usually smaller balls or beads). It uses an agitator shaft with arms or discs to create high-energy agitation, resulting in intense grinding action.
-
Mechanism of Grinding:
- Ball Mill: Grinding in a ball mill occurs through a combination of impact (balls striking the material) and attrition (rubbing of particles against each other and the grinding media). The grinding efficiency depends on the rotational speed and the size of the grinding media.
- Attritor: In an attritor, grinding is primarily achieved through shear forces and high-energy collisions caused by the agitation of the grinding media. The agitator ensures uniform distribution of energy, leading to more efficient and finer grinding.
-
Scale of Operation:
- Ball Mill: Ball mills are designed for large-scale operations and are commonly used in industries like mining, cement, and ceramics. They can handle large volumes of material and are suitable for coarse to medium grinding.
- Attritor: Attritors are more suited for small-scale or laboratory applications. They are ideal for fine grinding and can achieve smaller particle sizes compared to ball mills. They are often used in industries like pharmaceuticals, paints, and coatings.
-
Energy Efficiency:
- Ball Mill: Ball mills are less energy-efficient compared to attritors, especially for fine grinding. A significant amount of energy is lost due to the friction between the grinding media and the mill shell.
- Attritor: Attritors are more energy-efficient due to their high-speed agitation and smaller grinding media. They can achieve finer particle sizes with less energy consumption.
-
Applications:
- Ball Mill: Ball mills are used for grinding a wide range of materials, including ores, minerals, ceramics, and pigments. They are particularly effective for materials that require coarse grinding.
- Attritor: Attritors are used for grinding materials that require fine or ultra-fine particle sizes, such as pharmaceuticals, paints, and nanomaterials. They are also used for mixing and dispersing materials in liquid suspensions.
-
Maintenance and Wear:
- Ball Mill: Ball mills require regular maintenance due to the wear and tear of the grinding media and the mill lining. The large size of the grinding media can also lead to higher wear rates.
- Attritor: Attritors generally have lower maintenance requirements due to the smaller size of the grinding media and the more controlled grinding environment. However, the agitator and media may still require periodic replacement.
-
Cost Considerations:
- Ball Mill: Ball mills are typically more expensive to purchase and operate due to their larger size and higher energy consumption. However, they are cost-effective for large-scale operations.
- Attritor: Attritors are generally more cost-effective for small-scale or specialized applications. They offer lower operating costs due to their higher energy efficiency and smaller size.
-
Flexibility and Control:
- Ball Mill: Ball mills offer less control over the grinding process, especially for fine grinding. The particle size distribution can be less uniform compared to attritors.
- Attritor: Attritors provide better control over the grinding process, allowing for more precise particle size distribution. They are also more flexible in terms of adjusting grinding parameters like speed and media size.
In summary, the choice between a ball mill and an attritor depends on the specific requirements of the application, including the desired particle size, production scale, and material properties. Ball mills are better suited for large-scale, coarse grinding operations, while attritors are ideal for fine grinding and small-scale applications.
Summary Table:
Feature | Ball Mill | Attritor |
---|---|---|
Design | Large cylindrical shell with grinding media (steel/ceramic balls) | Vertical/horizontal vessel with smaller grinding media and agitator shaft |
Grinding Mechanism | Impact and attrition | Shear forces and high-energy agitation |
Scale of Operation | Large-scale, coarse grinding | Small-scale, fine grinding |
Energy Efficiency | Less efficient for fine grinding | More energy-efficient for fine grinding |
Applications | Ores, minerals, ceramics, pigments | Pharmaceuticals, paints, nanomaterials |
Maintenance | Higher maintenance due to wear and tear | Lower maintenance, but agitator/media may need replacement |
Cost | Higher purchase and operating costs | More cost-effective for small-scale applications |
Control | Less control over fine grinding | Better control and precision in particle size distribution |
Still unsure which grinding equipment is right for you? Contact our experts today for personalized advice!