Grinding mills and hammer mills are both essential equipment in material processing, but they differ significantly in their design, working principles, and applications. A grinding mill typically uses mechanical forces such as compression, impact, and shear to reduce the size of materials, often producing fine or ultrafine powders. In contrast, a hammer mill relies on high-speed rotating hammers to strike and shatter materials, making it ideal for coarse to medium grinding. While grinding mills are versatile and used in industries like mining and pharmaceuticals, hammer mills are commonly employed in agricultural and biomass processing. The choice between the two depends on the material properties and desired particle size.
Key Points Explained:
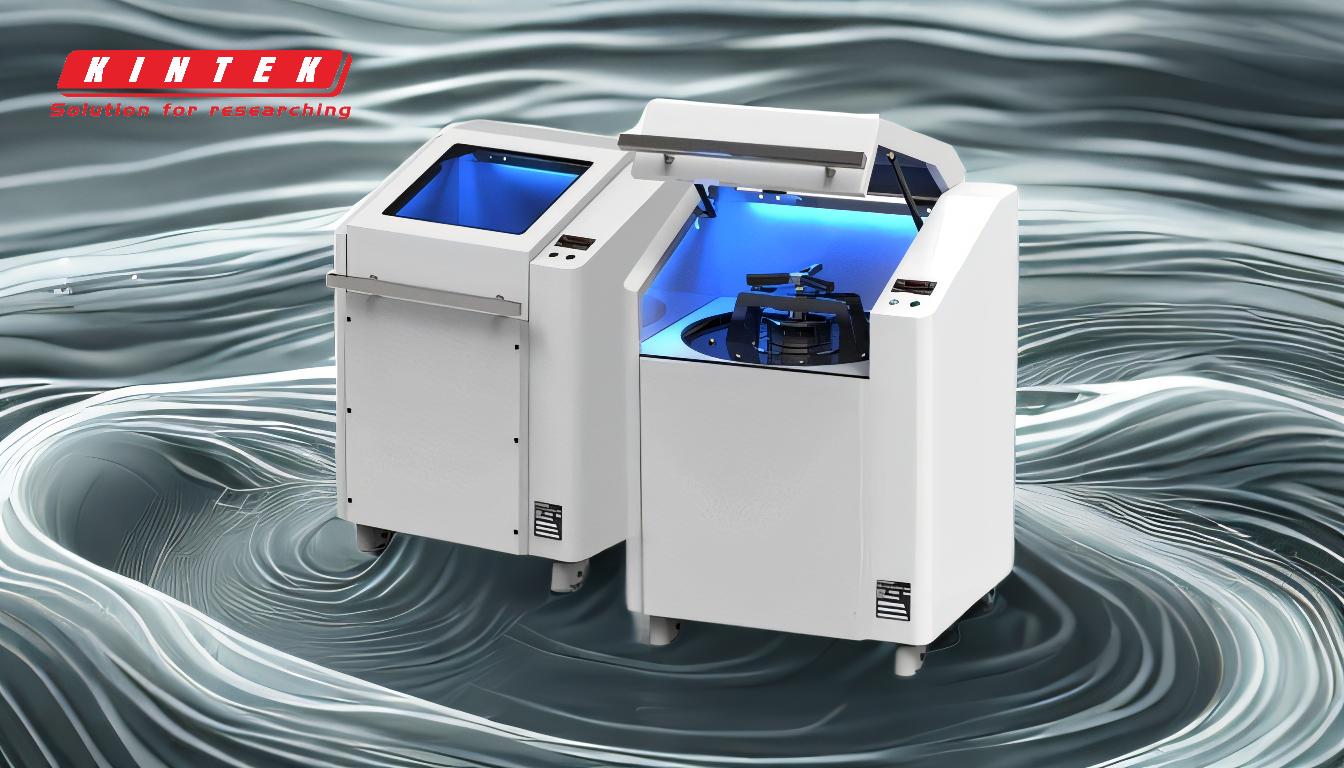
-
Working Principle:
- Grinding Mill: Utilizes mechanical forces such as compression, impact, and shear to break down materials. The grinding media (e.g., balls, rods) or grinding plates apply these forces to achieve size reduction.
- Hammer Mill: Operates by high-speed rotating hammers that strike and shatter materials upon impact. The particles are then forced through a screen to achieve the desired size.
-
Design and Components:
- Grinding Mill: Typically consists of a rotating drum or cylinder filled with grinding media. The design varies based on the type (e.g., ball mill, rod mill, or vertical roller mill).
- Hammer Mill: Features a series of hammers mounted on a rotor inside a grinding chamber. The hammers swing freely or are fixed, and the chamber includes a screen to control particle size.
-
Applications:
- Grinding Mill: Widely used in industries like mining, cement, and pharmaceuticals for producing fine or ultrafine powders. It is suitable for hard and abrasive materials.
- Hammer Mill: Commonly used in agricultural settings for grinding grains, biomass, and other organic materials. It is also used in recycling and food processing industries.
-
Particle Size Output:
- Grinding Mill: Capable of producing very fine particles, often in the micrometer range. The particle size distribution can be controlled more precisely.
- Hammer Mill: Produces coarser particles, typically in the millimeter to sub-millimeter range. The particle size is influenced by the screen size and hammer speed.
-
Energy Efficiency:
- Grinding Mill: Generally more energy-efficient for fine grinding tasks but may consume more power for coarse grinding.
- Hammer Mill: More energy-efficient for coarse grinding and can handle larger feed sizes with less energy consumption.
-
Maintenance and Durability:
- Grinding Mill: Requires regular maintenance of grinding media and liners. The wear and tear depend on the material hardness and grinding intensity.
- Hammer Mill: Hammers and screens are subject to wear and need frequent replacement, especially when processing abrasive materials.
-
Versatility:
- Grinding Mill: Highly versatile and can handle a wide range of materials, including hard and brittle substances.
- Hammer Mill: Best suited for softer materials like grains, biomass, and fibrous substances. It may struggle with very hard or dense materials.
-
Laboratory Applications:
- Grinding Mill: Often used in laboratories for sample preparation, especially when fine powders are required for analysis.
- Hammer Mill: A laboratory hammer mill is commonly used for small-scale grinding tasks, such as preparing samples for testing or research purposes.
By understanding these differences, purchasers can make informed decisions based on their specific material processing needs, desired particle size, and operational efficiency requirements.
Summary Table:
Aspect | Grinding Mill | Hammer Mill |
---|---|---|
Working Principle | Uses compression, impact, and shear for size reduction. | Relies on high-speed rotating hammers to shatter materials. |
Design | Rotating drum with grinding media (e.g., balls, rods). | Hammers mounted on a rotor inside a grinding chamber with a screen. |
Applications | Mining, cement, pharmaceuticals (fine/ultrafine powders). | Agriculture, biomass, recycling, and food processing (coarse to medium grinding). |
Particle Size | Produces fine or ultrafine particles (micrometer range). | Produces coarser particles (millimeter to sub-millimeter range). |
Energy Efficiency | Efficient for fine grinding; less so for coarse grinding. | Efficient for coarse grinding; handles larger feed sizes. |
Maintenance | Regular maintenance of grinding media and liners. | Frequent replacement of hammers and screens. |
Versatility | Handles a wide range of materials, including hard and brittle substances. | Best for softer materials like grains and biomass. |
Lab Applications | Used for sample preparation requiring fine powders. | Used for small-scale grinding tasks like sample testing. |
Need help choosing the right mill for your material processing needs? Contact our experts today!