Homogenizers and colloid mills are both used in the processing of liquids and semi-liquids, but they differ significantly in their mechanisms, applications, and outcomes. A homogenizer typically uses high pressure to force a product through a narrow gap, breaking down particles and creating a uniform mixture. In contrast, a colloid mill relies on high shear forces generated by a rotor-stator system to achieve superfine grinding, emulsifying, homogenizing, and dispersing in a single process cycle. While both devices aim to create uniform mixtures, the colloid mill is particularly effective for achieving finer particle sizes and simultaneous multi-functional processing, making it suitable for industries requiring ultra-fine emulsions or dispersions.
Key Points Explained:
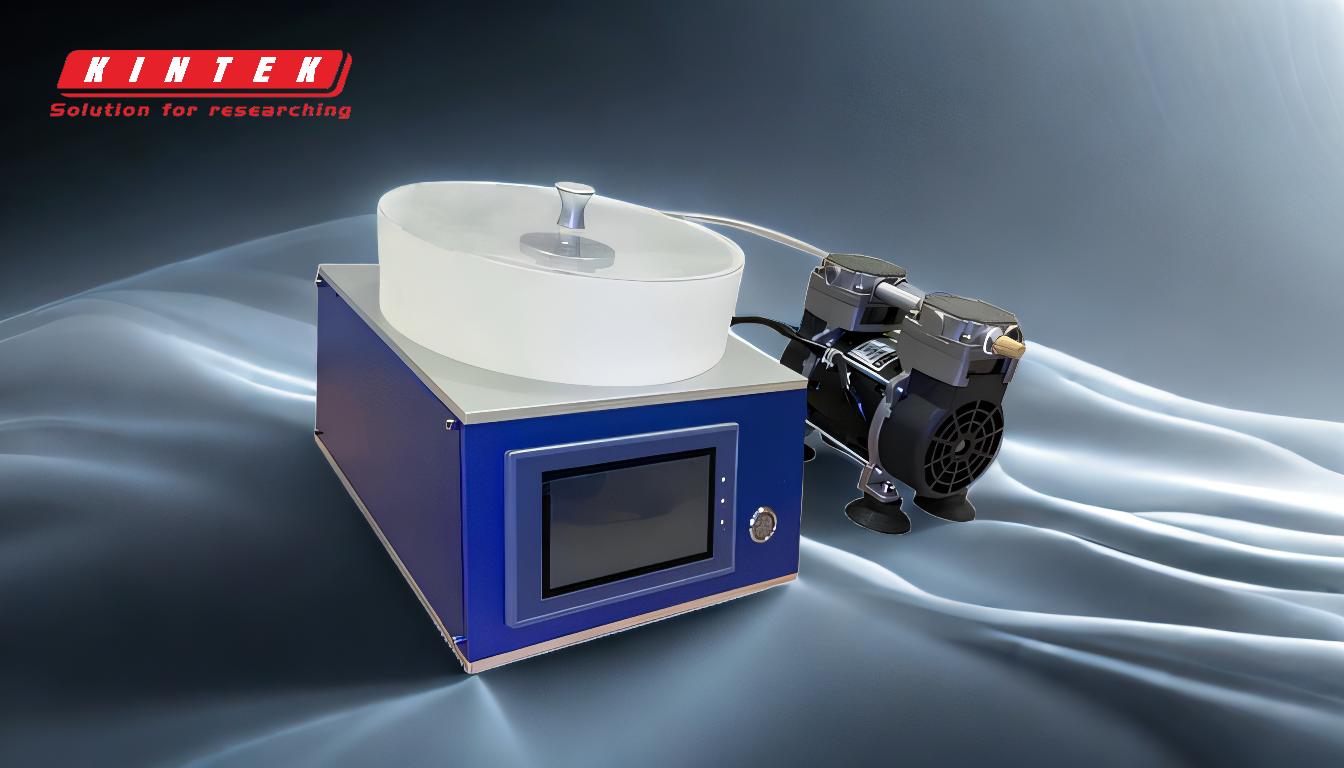
-
Mechanism of Operation:
- Homogenizer: Operates by forcing the product through a narrow gap under high pressure, which breaks down particles and creates a uniform mixture. This method is particularly effective for reducing particle size and achieving homogeneity in liquid mixtures.
- Colloid Mill: Utilizes a rotor-stator system to generate high shear forces. The product is subjected to intense mechanical action, which results in superfine grinding, emulsifying, homogenizing, and dispersing all in one cycle. This makes it highly efficient for processes requiring ultra-fine particle sizes.
-
Applications:
- Homogenizer: Commonly used in the food and beverage industry, pharmaceuticals, and cosmetics for creating stable emulsions, suspensions, and dispersions. It is ideal for products that require a high degree of uniformity and stability.
- Colloid Mill: Suitable for industries that require ultra-fine emulsions or dispersions, such as the chemical, pharmaceutical, and food industries. It is particularly effective for products that need simultaneous grinding, emulsifying, and homogenizing.
-
Outcome and Particle Size:
- Homogenizer: Typically achieves a uniform mixture with reduced particle size, but may not reach the ultra-fine levels that a colloid mill can achieve.
- Colloid Mill: Capable of achieving superfine grinding results, producing particles that are much smaller and more uniform than those produced by a homogenizer. This makes it ideal for applications requiring very fine emulsions or dispersions.
-
Process Efficiency:
- Homogenizer: Efficient for creating uniform mixtures but may require multiple passes to achieve the desired particle size reduction.
- Colloid Mill: Highly efficient as it combines multiple processes (grinding, emulsifying, homogenizing, and dispersing) into a single cycle, reducing the need for multiple processing steps.
-
Suitability for Different Products:
- Homogenizer: Best suited for products that require a high degree of uniformity and stability but do not necessarily need ultra-fine particle sizes.
- Colloid Mill: Ideal for products that require ultra-fine particle sizes and simultaneous multi-functional processing, making it suitable for more specialized applications.
In summary, while both homogenizers and colloid mills aim to create uniform mixtures, the choice between them depends on the specific requirements of the product and the desired outcome. Homogenizers are ideal for general homogenization and stability, whereas colloid mills excel in achieving ultra-fine particle sizes and multi-functional processing in a single cycle.
Summary Table:
Aspect | Homogenizer | Colloid Mill |
---|---|---|
Mechanism | High pressure forces product through a narrow gap to break down particles. | High shear forces via rotor-stator system for superfine grinding and emulsifying. |
Applications | Food, beverage, pharmaceuticals, cosmetics for stable emulsions and suspensions. | Chemical, pharmaceutical, food industries for ultra-fine emulsions and dispersions. |
Particle Size | Reduces particle size but may not achieve ultra-fine levels. | Achieves superfine grinding with smaller, more uniform particles. |
Process Efficiency | Efficient but may require multiple passes for desired particle size reduction. | Combines grinding, emulsifying, homogenizing, and dispersing in one cycle. |
Suitability | Ideal for general homogenization and stability. | Best for ultra-fine particle sizes and multi-functional processing. |
Need help choosing the right equipment for your liquid processing? Contact our experts today!