A mold is a tool used in manufacturing to shape plastic or other materials into a desired form. It is typically made from stainless steel and consists of one or more cavities, which are hollow spaces shaped like the part to be produced. The mold cavity is a specific part of the mold, representing the exact shape and dimensions of the final product. While the mold is the entire tool, the mold cavity is the specific area within the mold where the material is injected to form the part. Understanding this distinction is crucial for designing and selecting the right mold for manufacturing processes.
Key Points Explained:
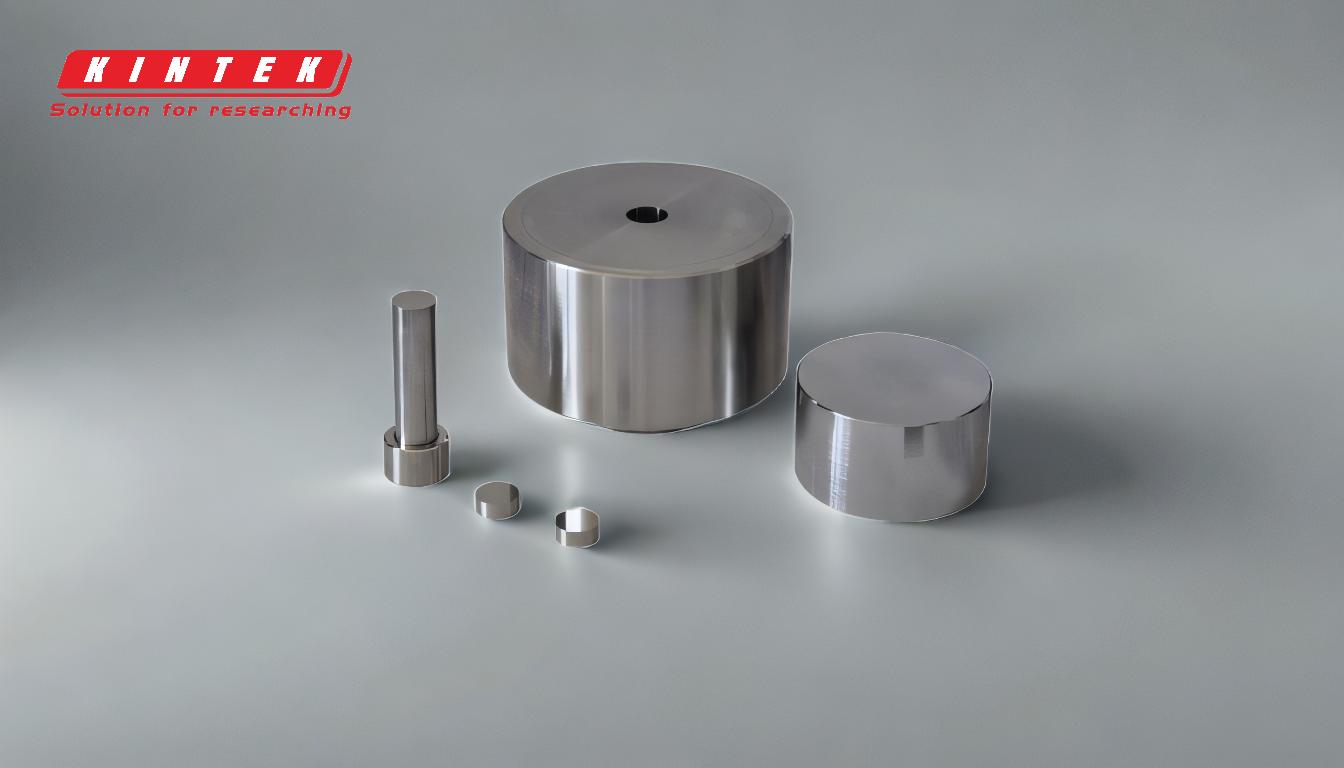
-
Definition of a Mold:
- A mold is a hollow form, usually made from durable materials like stainless steel, used in manufacturing processes such as injection molding.
- It serves as the overall tool that contains one or more cavities where the material is shaped into the desired part.
-
Definition of a Mold Cavity:
- The mold cavity is a specific part of the mold, representing the hollow space or hole within the mold that is shaped exactly like the final product.
- It is the area where the plastic or other material is injected and takes the form of the desired part.
-
Relationship Between Mold and Mold Cavity:
- The mold is the entire tool, while the mold cavity is a component of the mold.
- A single mold can have multiple cavities, allowing for the production of several parts simultaneously.
-
Functionality:
- The mold provides the structure and support needed for the injection molding process.
- The mold cavity defines the shape, size, and surface finish of the final product.
-
Design Considerations:
- When designing a mold, engineers must consider both the overall mold structure and the specific design of the mold cavity.
- The mold cavity must be precisely machined to ensure the final product meets the required specifications.
-
Material and Durability:
- Molds are typically made from high-strength materials like stainless steel to withstand the pressures and temperatures of the molding process.
- The mold cavity must also be made from durable materials to maintain its shape and precision over many production cycles.
-
Applications:
- Molds and mold cavities are used in various industries, including automotive, consumer goods, and medical devices, to produce complex and precise parts.
- Understanding the difference between the two is essential for selecting the right mold for a specific application.
-
Maintenance and Care:
- Regular maintenance of both the mold and mold cavity is necessary to ensure consistent product quality and to extend the lifespan of the mold.
- This includes cleaning, inspecting for wear, and making any necessary repairs or adjustments.
By understanding the distinction between a mold and a mold cavity, manufacturers can make informed decisions about mold design, material selection, and maintenance, ultimately leading to more efficient and effective production processes.
Summary Table:
Aspect | Mold | Mold Cavity |
---|---|---|
Definition | The entire tool used to shape materials into a desired form. | A specific hollow space within the mold that defines the shape of the product. |
Function | Provides structure and support for the molding process. | Determines the shape, size, and surface finish of the final product. |
Material | Typically made from durable materials like stainless steel. | Must also be durable to maintain precision over many production cycles. |
Design Considerations | Engineers must consider overall mold structure and cavity design. | Requires precise machining to meet product specifications. |
Applications | Used in industries like automotive, consumer goods, and medical devices. | Essential for producing complex and precise parts in various industries. |
Maintenance | Regular cleaning, inspection, and repairs are necessary. | Requires careful maintenance to ensure consistent product quality. |
Need help selecting the right mold for your manufacturing process? Contact our experts today!