Grinders and pulverizers are both machines used to reduce the size of materials, but they differ in their mechanisms, applications, and the fineness of the output. Grinders typically use abrasive surfaces to cut or crush materials into smaller pieces or powders, often through a shearing or crushing action. Pulverizers, on the other hand, focus on crushing or pressing materials until they become a fine powder or soft mass, often using impact or compression forces. While grinders are more versatile and used for a variety of materials, pulverizers are specialized for achieving ultra-fine powders, making them ideal for industries like pharmaceuticals, food processing, and chemical manufacturing.
Key Points Explained:
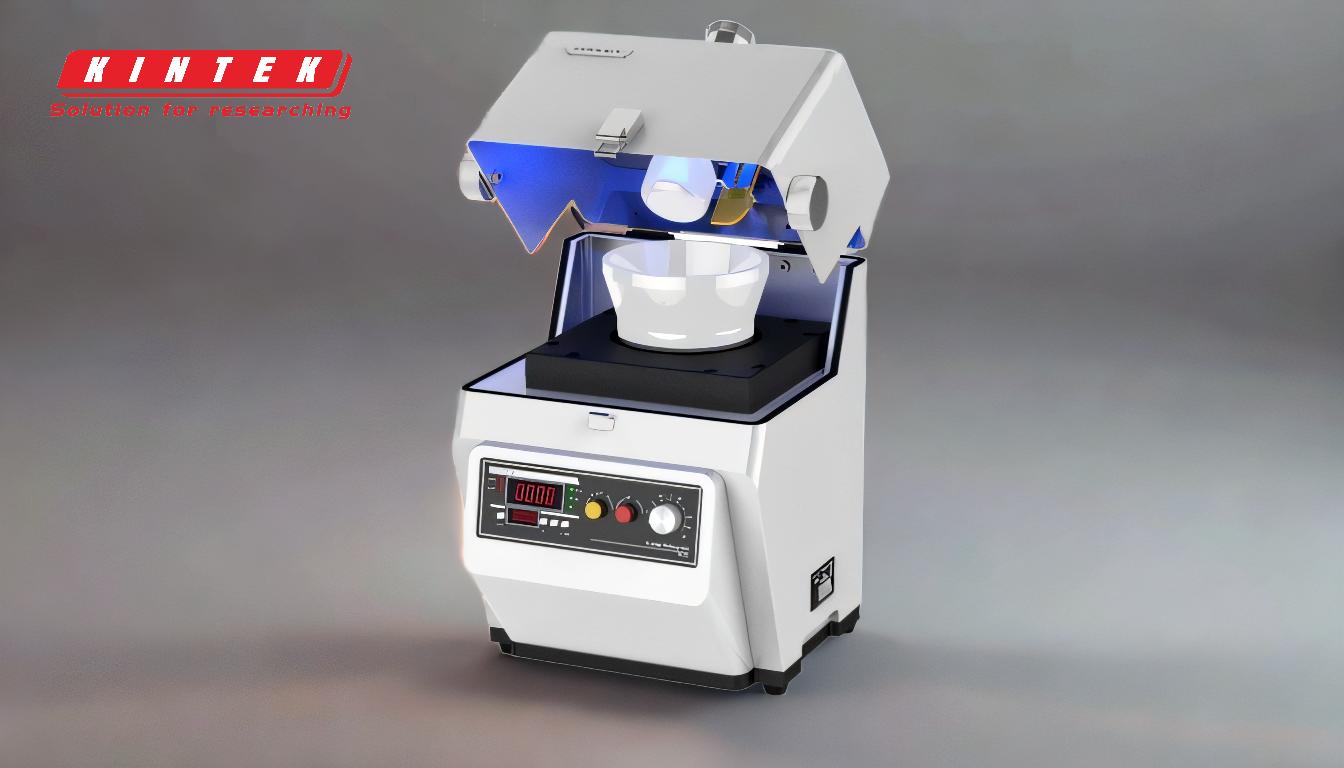
-
Mechanism of Operation
- Grinder: Grinders operate by using abrasive surfaces or hard materials to cut, crush, or shear the input material into smaller pieces or powders. The process often involves rotating blades, discs, or wheels that apply force to break down the material.
- Pulverizer: Pulverizers rely on impact, compression, or attrition forces to crush or press materials until they become a fine powder or soft mass. They often use hammers, rollers, or pins to achieve this.
-
Fineness of Output
- Grinder: The output from a grinder can range from coarse particles to fine powders, depending on the type of grinder and its settings. However, grinders are generally not designed to produce ultra-fine powders.
- Pulverizer: Pulverizers are specifically designed to produce very fine powders or soft masses. They excel in achieving a consistent and uniform particle size, making them suitable for applications requiring high precision.
-
Applications
- Grinder: Grinders are versatile and used in a wide range of industries, including food processing (e.g., coffee grinders), metalworking (e.g., angle grinders), and construction (e.g., concrete grinders). They are suitable for materials like grains, spices, metals, and plastics.
- Pulverizer: Pulverizers are more specialized and are commonly used in industries like pharmaceuticals, chemicals, and food processing, where ultra-fine powders are required. They are ideal for materials like herbs, minerals, and chemicals.
-
Types of Machines
- Grinder: Common types of grinders include angle grinders, bench grinders, coffee grinders, and meat grinders. Each type is designed for specific materials and applications.
- Pulverizer: Pulverizers come in various forms, such as hammer mills, ball mills, and ring mills. These machines are tailored for specific tasks, such as grinding minerals, herbs, or chemicals into fine powders.
-
Material Compatibility
- Grinder: Grinders can handle a wide variety of materials, including hard substances like metals and stones, as well as softer materials like food products.
- Pulverizer: Pulverizers are typically used for softer or brittle materials that can be easily crushed into fine powders. They are less suitable for extremely hard materials.
-
Energy Consumption and Efficiency
- Grinder: Grinders generally consume less energy compared to pulverizers, especially when used for coarse grinding. However, achieving fine powders with a grinder may require more time and energy.
- Pulverizer: Pulverizers are designed for high efficiency in producing fine powders, but they often require more energy due to the intense crushing or impact forces involved.
-
Maintenance and Durability
- Grinder: Grinders are relatively easy to maintain, with replaceable blades or discs. They are durable and can handle a variety of materials without significant wear.
- Pulverizer: Pulverizers may require more frequent maintenance, especially if used for abrasive materials. The hammers, pins, or rollers can wear out over time and need replacement.
-
Cost Considerations
- Grinder: Grinders are generally more affordable and widely available, making them a cost-effective choice for many applications.
- Pulverizer: Pulverizers tend to be more expensive due to their specialized design and higher energy requirements. However, they are a worthwhile investment for industries requiring ultra-fine powders.
By understanding these key differences, purchasers can make informed decisions about whether a grinder or pulverizer is more suitable for their specific needs, based on the material type, desired output, and industry requirements.
Summary Table:
Aspect | Grinder | Pulverizer |
---|---|---|
Mechanism | Uses abrasive surfaces, shearing, or crushing | Relies on impact, compression, or attrition forces |
Output Fineness | Coarse to fine powders, not ultra-fine | Ultra-fine powders or soft masses |
Applications | Versatile: food, metalworking, construction | Specialized: pharmaceuticals, chemicals, food processing |
Material Compatibility | Handles hard (metals, stones) and soft (food) materials | Best for soft or brittle materials (herbs, minerals, chemicals) |
Energy Efficiency | Lower energy consumption for coarse grinding | Higher energy consumption for fine powder production |
Maintenance | Easy maintenance with replaceable parts | Requires frequent maintenance for abrasive materials |
Cost | Affordable and cost-effective | More expensive due to specialized design |
Still unsure which machine is right for you? Contact our experts today for personalized advice!