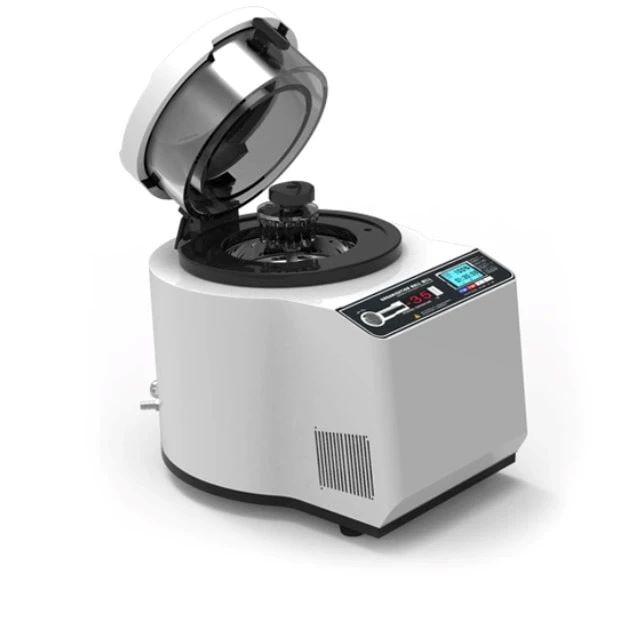
Milling Equipment
Laboratory High Throughput Tissue Grinding Mill Grinder
Item Number : KT-MT
Price varies based on specs and customizations
- Maximum injection size
- <10 mm
- Sample particle size range
- 0.1-20um
- Movement frequency
- 3000 times/min
- Number of ball mill jars
- 2
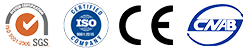
Shipping:
Contact us to get shipping details Enjoy On-time Dispatch Guarantee.
Why Choose Us
Reliable PartnerEasy ordering process, quality products, and dedicated support for your business success.
Introduction
High-throughput tissue grinder KT-MT is a high-quality small high-throughput tissue grinder, equipped with 24 2ml or 48 2ml cell wall breaking adapters and ball grinding tanks, the product can be used in food, medical, biological, metallurgy Sample crushing, grinding, mixing, homogenization, and cell wall breaking in the fields of chemical, chemical, and environmental protection are widely used in DNA, RNA, and protein extraction. The product conforms to ergonomic design, desktop visual operation, and adopts frequency conversion LCD control system Realize multiple functions such as speed regulation, timing, intermittent grinding, etc., 3000 times per minute high-frequency three-dimensional vibration, so K-MT has many advantages such as comprehensive functions, short processing time, good sampling effect, low noise, stable operation, and simple operation.
- Processing principle: impact force
- Application Sample Characteristics: Hard | Low to medium hardness | Brittle | Dry or wet | Fibrous | Elastic | Sticky
- Processing Type: Grinding | Blending | Cell Disruption | Homogenization
- Main functions: continuous and intermittent operation | variable speed operation | timing | power failure memory | temperature monitoring | liquid nitrogen port | condensate port | Double-layer PC sound-proof and visible flip cover | low-temperature grinding stainless steel inner cavity | sound-proof and heat-dissipating
Applications
The High Throughput Tissue Grinder is a versatile laboratory equipment designed for grinding and homogenizing a wide range of materials, including wet, soft, brittle, elastic, hard, dry, and fibrous substances. Its applications span across various sectors, particularly in research and development environments where precise and efficient material processing is crucial.
- Material Science Research: Ideal for researchers studying the properties of various materials, helping in the preparation of samples for analysis by reducing them to fine particles.
- Pharmaceutical Industry: Used in the grinding of pharmaceutical ingredients to ensure uniform particle size, which is critical for drug efficacy and stability.
- Food and Beverage Industry: Essential for the homogenization of food products, enhancing the texture and consistency of food items.
- Environmental Testing: Employed in the preparation of soil and other environmental samples for analysis, aiding in the assessment of environmental health.
- Academic Research: Widely used in university labs for educational and research purposes, facilitating hands-on learning and experimentation.
- Government Testing Facilities: Supports the rigorous testing and analysis of materials in government-run laboratories, ensuring compliance with safety and quality standards.
- Pilot Plants: Helps in the development and testing of new products and processes on a small scale before full-scale production.
Advantages
The High Throughput Tissue Grinder offers a multitude of advantages that enhance laboratory efficiency and productivity. Key benefits include:
- Increased Productivity: The grinder optimizes particle size and increases throughput, significantly boosting productivity in sample preparation.
- Decreased Wear on Equipment: The design reduces wear and tear on grinding equipment, extending the lifespan of the machinery.
- Separation of Composite Materials: It facilitates the separation of composite materials within the mill, enhancing the purity of the final product.
- Higher Production Rate: With its advanced technology, the grinder achieves a higher production rate compared to traditional methods.
- Lower Energy Consumption: It operates with lower energy consumption, making it an eco-friendly choice for laboratories.
- Fine Particle Size: The grinder produces a fine particle size, which is crucial for many analytical and research applications.
- Uniform Particle Distribution: It ensures a more uniform particle distribution, improving the consistency and quality of the ground material.
- Lower Grinding Cost: The overall grinding cost is reduced, making it a cost-effective solution for sample preparation.
- Improved Pouring Properties: Finely ground materials improve pouring properties, enhancing the usability of the samples in various applications.
- Simplicity of Maintenance: Easy maintenance that can be performed by operators without specialized assistance, reducing downtime.
- Excellent OEE: The grinder boasts very reduced downtimes for cleaning and maintenance, contributing to its high Overall Equipment Effectiveness.
- Highest Reduction of Production Time: Significantly reduces production time by up to 50% compared to traditional mills, enhancing laboratory workflow efficiency.
- More Power & Lifetime: The vibratory head is driven by a universal shaft, delivering more power to the grinding bowls and optimizing motor life.
- Size Reduction to 2 Microns and Below: Achieves ultra-fine grinding, crucial for detailed analysis and research.
- Automatic Control System: Features an automatic control system for precise and consistent grinding operations.
- Easy to Disassemble and Clean: Quick coupling installation allows for easy disassembly and cleaning, maintaining hygiene and operational efficiency.
- Small Footprint: Efficient space utilization with a compact design, ideal for laboratories with limited space.
- No Risk of Contamination: Ensures no risk of contamination during the grinding process, crucial for maintaining sample integrity.
Features
The High Throughput Tissue Grinder is a versatile and efficient laboratory tool designed for processing a wide range of materials, from soft and brittle to hard and fibrous. This equipment is particularly beneficial for research environments such as pilot plants, university labs, and government testing facilities, where precision and efficiency are paramount. Here are the key features that enhance its utility and performance:
- High Processing Capacity: Capable of processing 50-150 pounds per hour, depending on the material type, this grinder ensures high throughput in laboratory settings.
- Customizable Product Size: The size of the ground material can be adjusted according to the choice of screen size and hammer speed, grinding materials down to under 1mm.
- Robust Motor and Drive System: Powered by a 1.5kW electric motor via vee-belts, the grinder delivers more power to the grinding bowls, optimizing motor life and enhancing the grinding efficiency.
- Multiple Grinding Bowls: The ability to install one to four grinding bowls with different capacities allows for a maximum total of 1600 grams of samples, catering to various research needs.
- Versatile Application: Suitable for grinding or homogenizing a variety of materials, including wet, soft, brittle, elastic, hard, dry, and fibrous substances.
- Advanced Grinding Technology: Utilizes a unique working principle where the motor drives the rotating shaft to generate centrifugal force, causing the bowl puck and ring to hit, squeeze, and grind the sample effectively.
- No Risk of Contamination: Features easy disassembly and cleaning with quick couplings, ensuring no contamination during the grinding process.
- Compact Design: Efficient space utilization with a small footprint, making it ideal for labs with limited space.
- Plug and Play: No additional installation required, simplifying setup and operation.
- Custom Design Options: Available for specific research needs, ensuring the equipment meets the exact requirements of your laboratory.
These features collectively make the High Throughput Tissue Grinder an indispensable tool for laboratories requiring efficient, precise, and versatile material processing capabilities.
Detail & Parts
Technical specifications
Model | K-MT24 | K-MT48 |
Recommended maximum injection size | < 10mm | < 10mm |
Sample particle size range | 0.1-20um | 0.1-20um |
Grinding method | dry grinding | wet grinding | low temperature grinding | dry grinding | wet grinding | low temperature grinding |
Number of ball mill jars | 2 | 2 |
Range of motion | 35mm | 55mm |
Movement mode | 8-track high-frequency three-dimensional movement | 8-track high-frequency three-dimensional movement |
Vibration frequency | 3000 times/min | 3000 times/min |
Control mode | LCD screen frequency conversion control | LCD screen frequency conversion control |
Time setting | 99:99:99(h:m:s) | 99:99:99(h:m:s) |
Ball mill material | Zirconia | Tungsten Carbide | Stainless Steel | PTFE Optional | Zirconia | Tungsten Carbide | Stainless Steel | PTFE Optional |
Ball mill jar volume | 15mlX2 | 25mlX2 | 50mlX2 | 15mlX2 | 25mlX2 | 50mlX2 |
Grinding carrier type | ball mill jar | cell disruption adapter | ball mill jar | cell disruption adapter |
Grinding ball size | 0.1-25m optional | 0.1-25m optional |
Configurable centrifuge tube volume | 0.2ml | 0.5ml | 2ml | 5ml etc. | 0.2ml | 0.5ml | 2ml | 5ml etc. |
Cell breaking adapter | 0.2-2ml X 24 | 5-15ml X 8 | 0.2-2ml X 48 | 5-15ml X 8 |
Adapter material | PC | MC | PC | MC |
Centrifuge tube material | EP | EP |
Electrical description | 200-240V AC,50-60Hz,150W | 200-240V AC,50-60Hz,200W |
Power port | National Standard | European Standard | American Standard | British Standard, etc. | National Standard | European Standard | American Standard | British Standard, etc. |
Net weight | 28kg | 32kg |
Dimensions (length, width and height) | 380*480*350mm | 380*480*350mm |
Protection class | IP65 | IP65 |
Standard | CE | CE |
Noise description | <60dB | <60dB |
Warnings
Operator safety is the top important issue! Please operate the equipment with cautions. Working with inflammable& explosive or toxic gases is very dangerous, operators must take all necessary precautions before starting the equipment. Working with positive pressure inside the reactors or chambers is dangerous, operator must fellow the safety procedures strictly. Extra caution must also be taken when operating with air-reactive materials, especially under vacuum. A leak can draw air into the apparatus and cause a violent reaction to occur.
Designed for You
KinTek provide deep custom made service and equipment to worldwide customers, our specialized teamwork and rich experienced engineers are capable to undertake the custom tailoring hardware and software equipment requirements, and help our customer to build up the exclusive and personalized equipment and solution!
Would you please drop your ideas to us, our engineers are ready for you now!
FAQ
What Is The Difference Between Cryogenic And Conventional Grinding Processes?
How Does The Multiple Grinding Bowls Design Benefit The Grinding Process?
4.8
out of
5
KINTEK's High Throughput Tissue Grinder is a lifesaver! The machine's speed, accuracy, and ease of use have transformed our lab's workflow. Highly recommended!
4.7
out of
5
The High Throughput Tissue Grinder from KINTEK is a great investment. It's a versatile machine that handles various sample types and consistently delivers exceptional results.
4.9
out of
5
I'm thrilled with the KINTEK High Throughput Tissue Grinder. It's a user-friendly machine that integrates seamlessly into our lab setup. The results have been consistently impressive.
4.6
out of
5
KINTEK's High Throughput Tissue Grinder is a solid choice for labs seeking efficiency and accuracy. The machine's intuitive interface and reliable performance make it a valuable asset.
4.8
out of
5
The High Throughput Tissue Grinder from KINTEK has exceeded our expectations. Its speed and precision have significantly improved our sample processing times, leading to increased productivity.
4.7
out of
5
I highly recommend the KINTEK High Throughput Tissue Grinder. It's a robust machine that handles challenging samples with ease. The quality of the results is outstanding.
4.9
out of
5
KINTEK's High Throughput Tissue Grinder is a game-changer. Its advanced technology and user-friendly design make it an indispensable tool in our lab. The results are always precise and consistent.
4.6
out of
5
We're delighted with the KINTEK High Throughput Tissue Grinder. It has streamlined our sample processing workflow, reducing turnaround times significantly. The machine's durability and reliability are exceptional.
4.8
out of
5
The High Throughput Tissue Grinder from KINTEK is a worthwhile investment. It's a versatile machine that accommodates various sample types and delivers consistent, high-quality results. Highly recommended!
4.7
out of
5
KINTEK's High Throughput Tissue Grinder is an excellent choice for labs seeking efficiency and accuracy. The machine's user-friendly interface and reliable performance make it a valuable asset.
4.9
out of
5
I'm thoroughly impressed with the KINTEK High Throughput Tissue Grinder. It's a robust machine that handles challenging samples with ease. The quality of the results is outstanding.
4.6
out of
5
We're delighted with the KINTEK High Throughput Tissue Grinder. It has streamlined our sample processing workflow, reducing turnaround times significantly. The machine's durability and reliability are exceptional.
4.8
out of
5
The High Throughput Tissue Grinder from KINTEK is a worthwhile investment. It's a versatile machine that accommodates various sample types and delivers consistent, high-quality results. Highly recommended!
4.7
out of
5
KINTEK's High Throughput Tissue Grinder is an excellent choice for labs seeking efficiency and accuracy. The machine's user-friendly interface and reliable performance make it a valuable asset.
4.9
out of
5
I'm thoroughly impressed with the KINTEK High Throughput Tissue Grinder. It's a robust machine that handles challenging samples with ease. The quality of the results is outstanding.
4.6
out of
5
We're delighted with the KINTEK High Throughput Tissue Grinder. It has streamlined our sample processing workflow, reducing turnaround times significantly. The machine's durability and reliability are exceptional.
4.8
out of
5
The High Throughput Tissue Grinder from KINTEK is a worthwhile investment. It's a versatile machine that accommodates various sample types and delivers consistent, high-quality results. Highly recommended!
4.7
out of
5
KINTEK's High Throughput Tissue Grinder is an excellent choice for labs seeking efficiency and accuracy. The machine's user-friendly interface and reliable performance make it a valuable asset.
4.9
out of
5
I'm thoroughly impressed with the KINTEK High Throughput Tissue Grinder. It's a robust machine that handles challenging samples with ease. The quality of the results is outstanding.
Products
Laboratory High Throughput Tissue Grinding Mill Grinder
REQUEST A QUOTE
Our professional team will reply to you within one business day. Please feel free to contact us!
Related Products
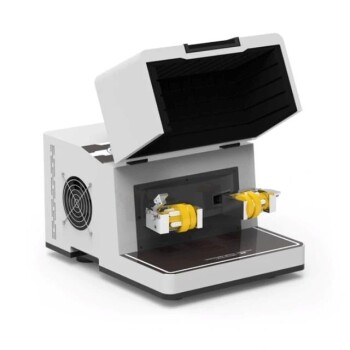
Laboratory Hybrid Tissue Grinding Mill
KT-MT20 is a versatile laboratory device used for rapid grinding or mixing of small samples, whether dry, wet, or frozen. It comes with two 50ml ball mill jars and various cell wall breaking adapters for biological applications such as DNA/RNA and protein extraction.
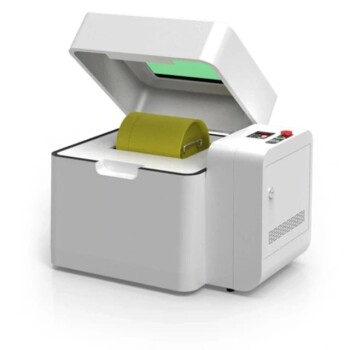
Laboratory Single Horizontal Jar Mill
KT-JM3000 is a mixing and grinding instrument for placing a ball milling tank with a volume of 3000ml or less. It adopts frequency conversion control to realize timing, constant speed, direction change, overload protection and other functions.
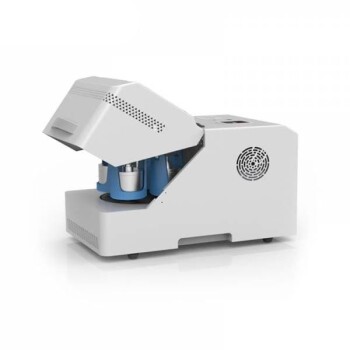
Mini Planetary Ball Mill Machine for Laboratory Milling
Discover the KT-P400 desktop planetary ball mill, ideal for grinding and mixing small samples in the lab. Enjoy stable performance, long service life, and practicality. Functions include timing and overload protection.
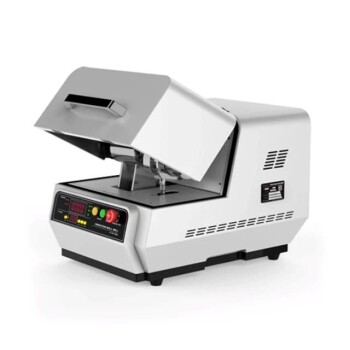
High Energy Vibratory Laboratory Ball Mill Grinding Mill Single Tank Type
High-energy vibration ball mill is a small desktop laboratory grinding instrument.It can be ball-milled or mixed with different particle sizes and materials by dry and wet methods.
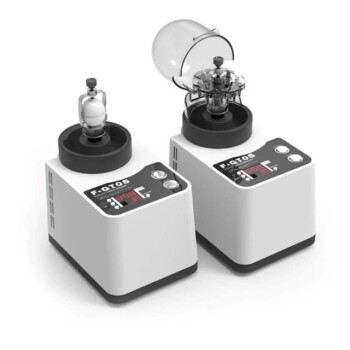
Laboratory Micro Tissue Grinding Mill Grinder
KT-MT10 is a miniature ball mill with a compact structure design. The width and depth are only 15X21 cm, and the total weight is only 8 kg. It can be used with a minimum 0.2ml centrifuge tube or a maximum 15ml ball mill jar.
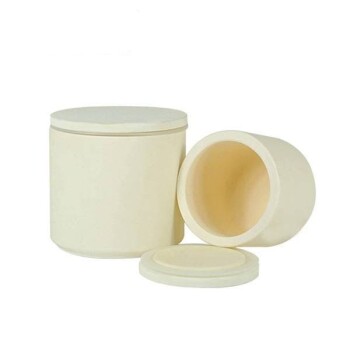
Laboratory Jar Ball Mill with Alumina Zirconia Grinding Jar and Balls
Grind to perfection with alumina/zirconia grinding jars and balls. Available in volume sizes from 50ml to 2500ml, compatible with various mills.
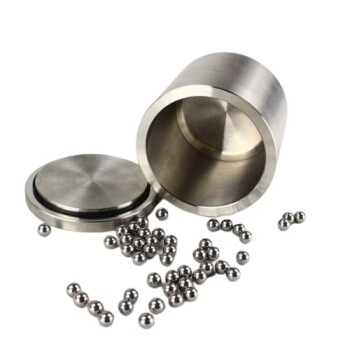
Laboratory Ball Mill Jar Mill with Metal Alloy Grinding Jar and Balls
Grind and mill with ease using metal alloy grinding jars with balls. Choose from 304/316L stainless steel or tungsten carbide and optional liner materials. Compatible with various mills and features optional functions.
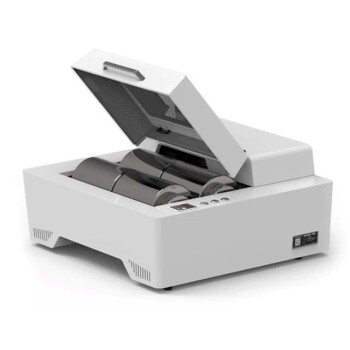
Laboratory Four-Body Horizontal Jar Mill
The four-body horizontal tank mill ball mill can be used with four horizontal ball mill tanks with a volume of 3000ml. It is mostly used for mixing and grinding laboratory samples.
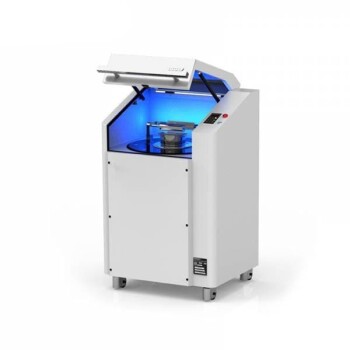
Vibration Mill for Efficient Sample Preparation, Suitable for Crushing and Grinding a Variety of Materials with Analytical Precision. Supports Dry / Wet / Cryogenic Grinding and Vacuum/Inert Gas Protection.
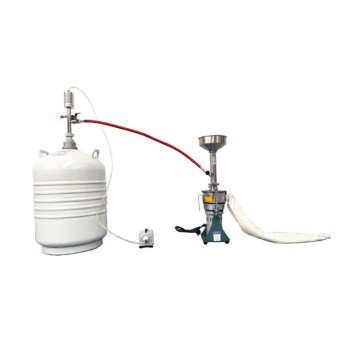
Liquid Nitrogen Cryogenic Grinder Mill Cryomill Airflow Ultrafine Pulverizer
Discover the Liquid Nitrogen Cryogenic Grinding Machine, perfect for lab use, ultra-fine pulverization, and preserving material properties. Ideal for pharmaceuticals, cosmetics, and more.
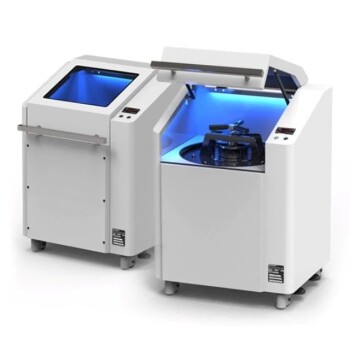
Laboratory Disc Cup Vibratory Mill for Sample Grinding
The vibrating disc mill is suitable for non-destructive crushing and fine grinding of samples with large particle sizes, and can quickly prepare samples with analytical fineness and purity.
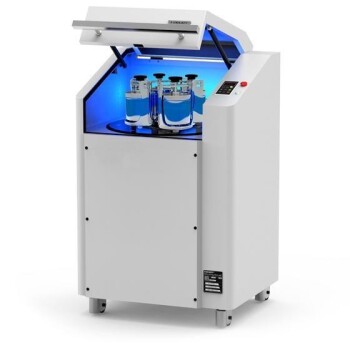
Laboratory Planetary Ball Mill Cabinet Planetary Ball Milling Machine
The vertical cabinet structure combined with ergonomic design enables users to obtain the best comfortable experience in standing operation. The maximum processing capacity is 2000ml, and the speed is 1200 revolutions per minute.
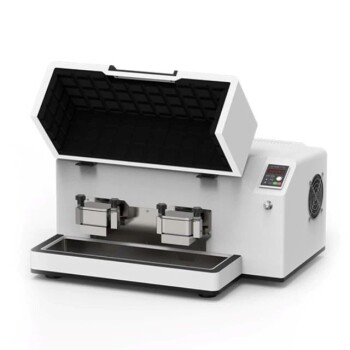
High Energy Vibratory Ball Mill for Lab Use
The high-energy vibrating ball mill is a high-energy oscillating and impacting multifunctional laboratory ball mill. The table-top type is easy to operate, small in size, comfortable and safe.
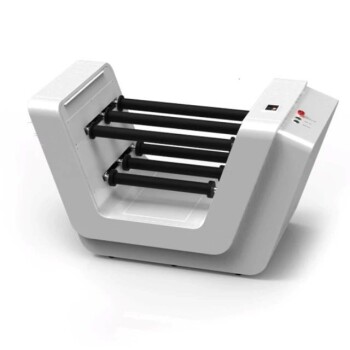
Laboratory Ten-Body Horizontal Jar Mill for Lab Use
The Ten-body horizontal jar mill is for 10 ball mill pots (3000ml or less). It has frequency conversion control, rubber roller movement, and PE protective cover.
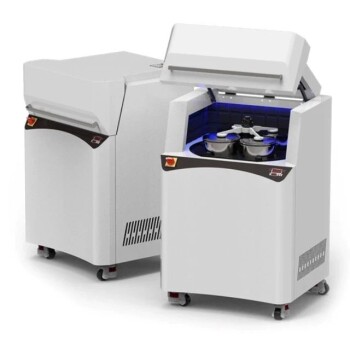
Disc Cup Vibrating Mill Multi-Platform for Lab
The multi-platform vibrating disc mill is suitable for non-destructive crushing and fine grinding of samples with large particle sizes. It is suitable for crushing and grinding applications of medium-hard, high-hard, brittle, fibrous, and elastic materials.
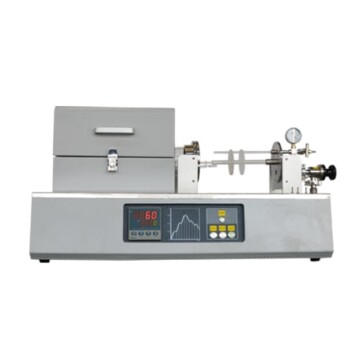
Laboratory Quartz Tube Furnace Tubular RTP Heating Furnace
Get lightning-fast heating with our RTP Rapid Heating Tube Furnace. Designed for precise, high-speed heating and cooling with convenient sliding rail and TFT touch screen controller. Order now for ideal thermal processing!
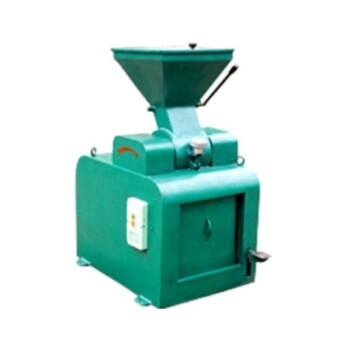
Laboratory Sealed Hammer Crusher for Efficient Sample Preparation
Discover the Laboratory Sealed Hammer Crusher for efficient sample preparation. Ideal for coal, metallurgy, and research, this crusher ensures high production efficiency and environmental friendliness.
Related Articles
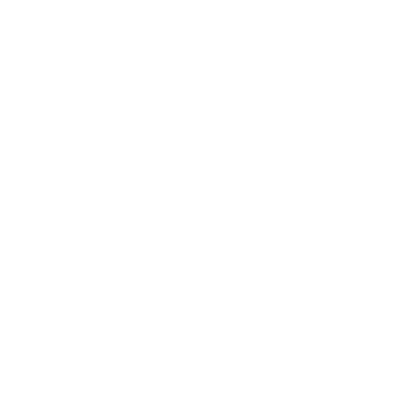
Key Features of the Micro Tissue Grinder: Usage, Advantages, and Applications
Discover the key features of the Micro Tissue Grinder, including usage instructions, advantages, and application fields. Learn the principles and structure of the Micro Tissue Grinder, and explore its benefits in sample preparation and industrial settings.
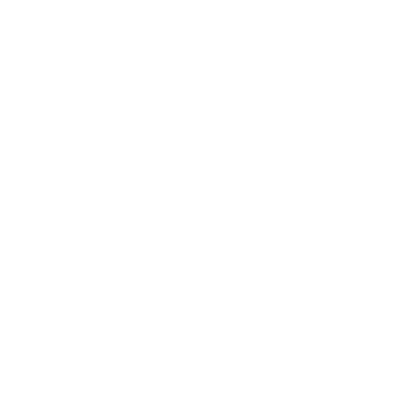
The Three Stages of Lab Crushing: A Comprehensive Guide
Learn about the three stages of crushing: primary, secondary, and tertiary, and how they are used in sample preparation for scientific analysis. Discover the different types of crushers and their applications in reducing bulky materials into smaller particles.
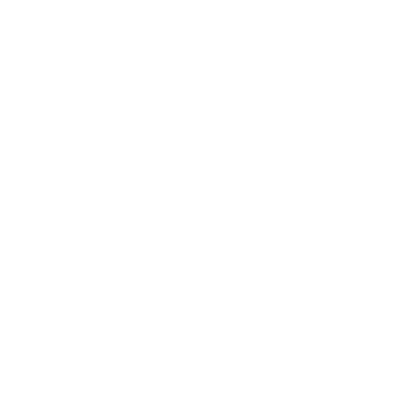
What is a Laboratory Crusher Used For?
Discover the uses and working mechanism of laboratory crushers. Explore various types of crushing equipment and their applications. Learn how laboratory crushers play a crucial role in scientific analysis and environmental studies.
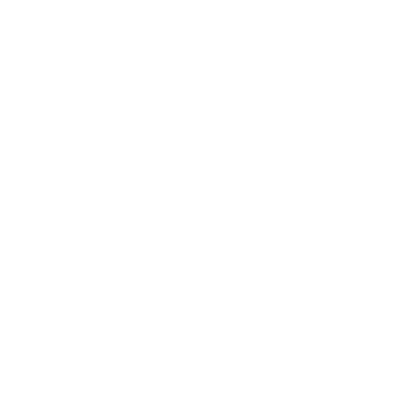
Laboratory Crushers: A Comprehensive Guide to Their Uses and Functionality
Laboratory crushers play a crucial role in scientific research and analysis. These crushers, commonly known as jaw crushers, are indispensable in obtaining accurate and consistent results for sample preparation.
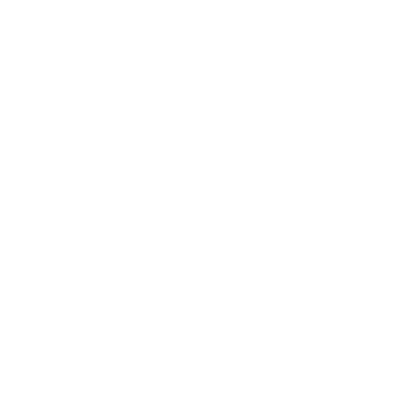
Revolutionize Your Spectroscopy Analysis with FTIR Pellet Press
FTIR (Fourier Transform Infrared) spectroscopy is a widely used technique to analyze the chemical composition of various materials. This method is particularly useful for samples that are difficult to analyze using other techniques.
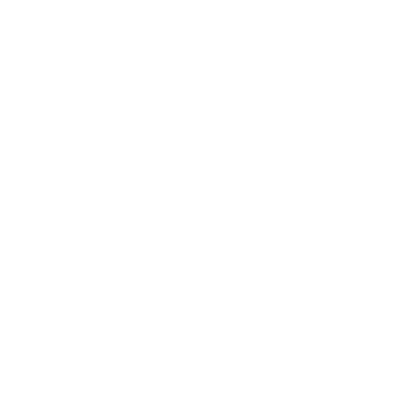
How to Use FTIR Pellet Press to Prepare Samples for Analysis
Fourier Transform Infrared (FTIR) spectroscopy is a powerful analytical technique used to identify and quantify chemical compounds in a wide range of samples. FTIR analysis requires the sample to be in the form of a pellet, which is prepared by compressing the sample with a suitable matrix material.
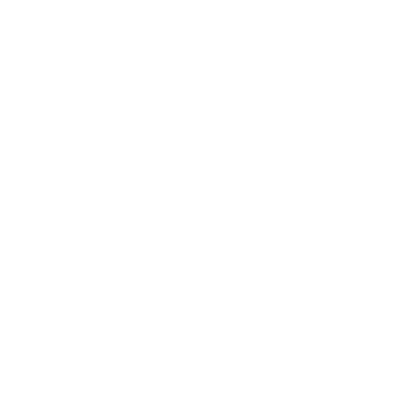
Laboratory Sample Preparation and Digestion Equipment
Overview of essential lab equipment for sample preparation and digestion.
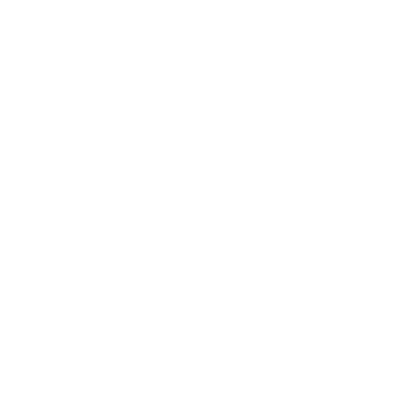
Development and Principles of Frozen Tissue Crushers
Explore the history, classification, and principles of frozen tissue crushers, including grinding ball selection and how to choose the right crusher.
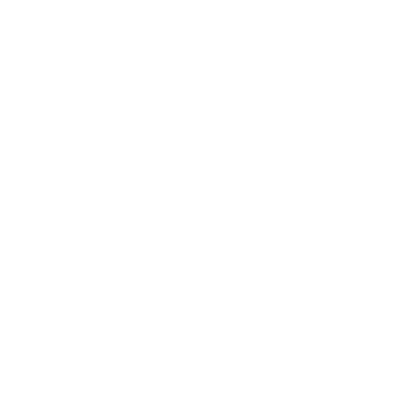
Application of Ultra-Micro Pulverization Technology in the Food Industry
Explores the benefits and applications of ultra-micro pulverization technology in enhancing food processing and nutrient absorption.
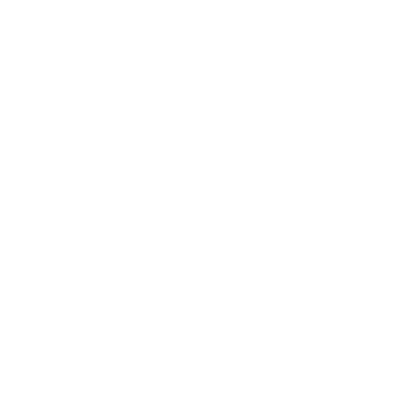
Basic Laboratory Centrifuge Equipment
Overview of different types of centrifuges used in laboratories.
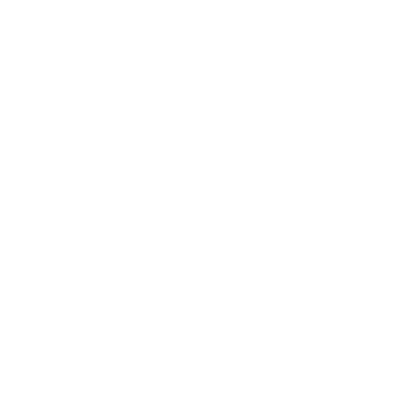
Sample Preparation Methods in X-ray Fluorescence and Their Impact on Test Results
Explores the tablet and melting methods in X-ray fluorescence, detailing their advantages, disadvantages, and key considerations.
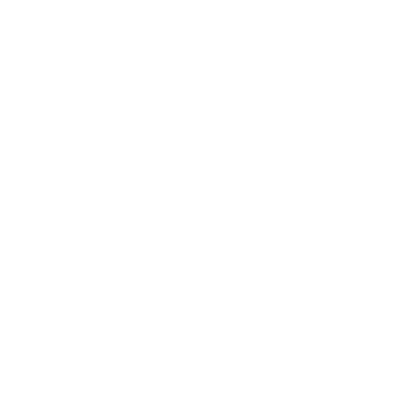
Why Most PELLET PRESS XRF SAMPLE PREPARATION Fail: Common Issues and Solutions
Discover the common pitfalls in PELLET PRESS XRF SAMPLE PREPARATION and learn effective solutions to ensure accurate results. Covers particle size, contamination, binder choice, and more.