Microwave and Electrothermal Digestion Instruments
Microwave Digestion Instrument
Microwave digestion instruments revolutionize sample preparation by leveraging the power of microwaves to heat reagents and samples within a closed container. This method not only accelerates the digestion process but also enhances the overall efficiency of laboratory workflows.
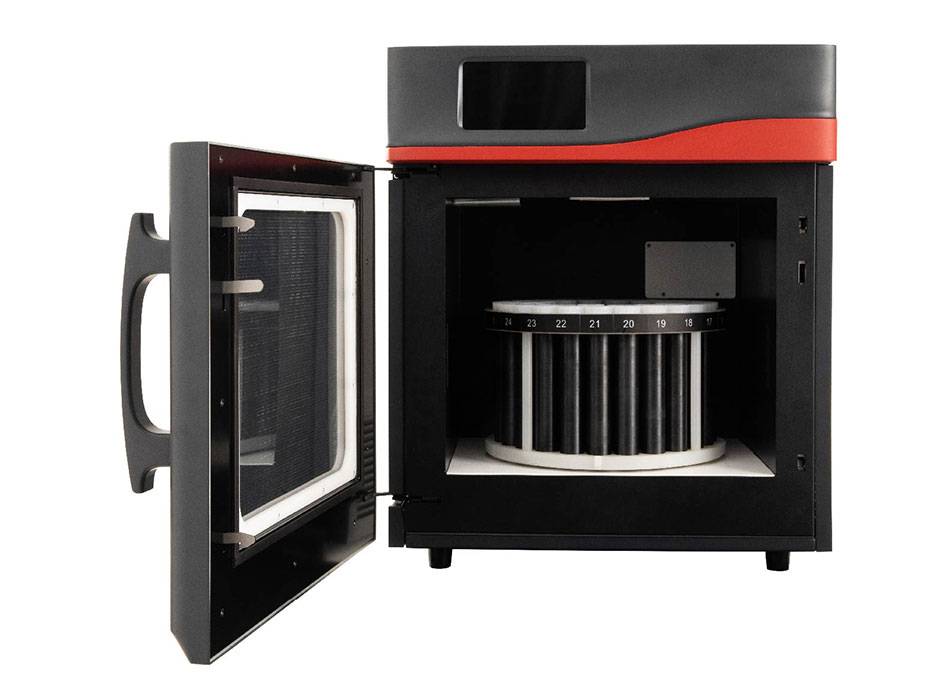
The closed-container system employed in microwave digestion instruments is crucial for several reasons. Firstly, it prevents the loss of volatile compounds, ensuring that the sample integrity is preserved. Secondly, the closed environment allows for the build-up of pressure, which in turn increases the reaction temperature. This elevated temperature significantly reduces the time required for sample digestion, making the process more time-efficient.
Moreover, the use of microwaves in this process introduces a uniform and rapid heating mechanism. Unlike traditional heating methods, microwaves penetrate the sample, causing polar molecules to oscillate and generate heat internally. This uniform heating minimizes hotspots and ensures that the entire sample is digested evenly, leading to more accurate and reproducible results.
In summary, microwave digestion instruments offer a superior method for sample preparation by combining rapid heating, increased pressure, and a closed-container system, all of which contribute to faster and more efficient sample digestion.
Electrothermal Digestion Instrument
The electrothermal digestion instrument is a sophisticated piece of laboratory equipment designed to heat samples using alternating current (AC) power. This method leverages the interaction between polar molecules and microwave frequency, a process that significantly accelerates the digestion process.
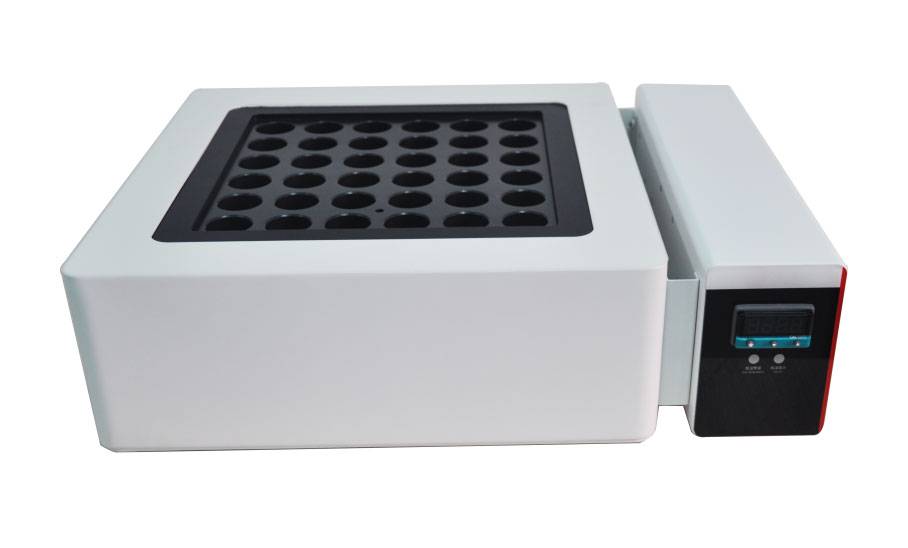
When AC power is applied, polar molecules within the sample rapidly change their orientation in response to the oscillating electric field. This rapid change in orientation increases the molecular energy of the sample, leading to a corresponding rise in sample temperature. The efficiency of this process is attributed to the continuous and rapid changes in molecular orientation, which are synchronized with the microwave frequency.
This method of heating offers several advantages over traditional heating techniques. Firstly, it allows for more uniform heating, as the energy is distributed evenly across the sample. Secondly, the rapid increase in molecular energy translates to faster sample digestion times, making it an ideal choice for laboratories requiring high throughput. Additionally, the controlled environment provided by the electrothermal digestion instrument minimizes the risk of sample contamination, ensuring more accurate and reliable results.
In summary, the electrothermal digestion instrument harnesses the power of AC and microwave frequency to expedite sample digestion, offering a reliable and efficient solution for laboratories engaged in complex sample preparation processes.
UV and Furnace Digestion Instruments
UV Digestion Instrument
The UV digestion instrument employs ultraviolet photocatalysis to generate free radicals, which are highly reactive species that can effectively break down organic matter in liquid samples. This method is particularly advantageous in analytical chemistry, where the presence of organic contaminants can interfere with the accurate measurement of heavy metals. By utilizing UV light, the instrument triggers a series of photochemical reactions that degrade organic molecules into simpler, non-interfering compounds.
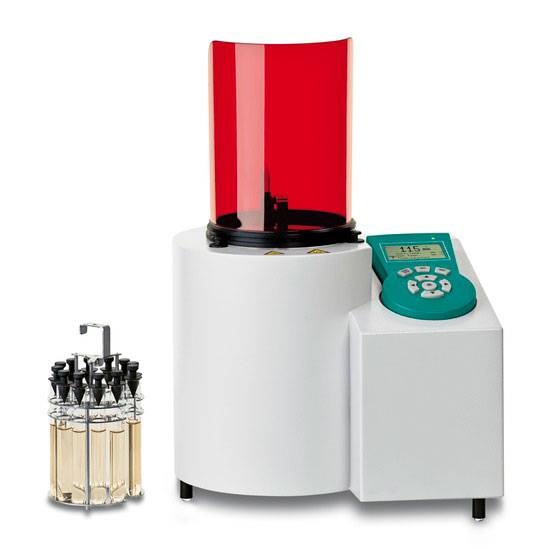
This process not only ensures the purity of the sample but also enhances the accuracy and reliability of subsequent analytical tests. The UV digestion instrument is a critical tool in laboratories where the analysis of trace elements, such as heavy metals, is paramount. It provides a controlled and efficient means of sample preparation, minimizing the risk of contamination and ensuring that the results reflect the true composition of the sample.
Feature | Description |
---|---|
Technology | Ultraviolet photocatalysis for generating free radicals. |
Application | Digestion of organic matter in liquid samples. |
Benefit | Avoids interference with heavy metal tests by breaking down organic contaminants. |
Importance | Enhances accuracy and reliability in trace element analysis. |
The UV digestion instrument is a cornerstone in modern analytical laboratories, offering a sophisticated solution for the preparation of samples that require the utmost precision and cleanliness.
Digestion Furnace
The digestion furnace stands out as a critical piece of equipment in laboratory sample preparation, particularly for its ability to handle the delicate balance between efficient sample digestion and environmental safety. This instrument employs a well-type electric heating mechanism, which is instrumental in rapidly elevating the temperature of the samples. This method not only accelerates the digestion process but also ensures that the harmful gases generated during the digestion are effectively managed and contained.
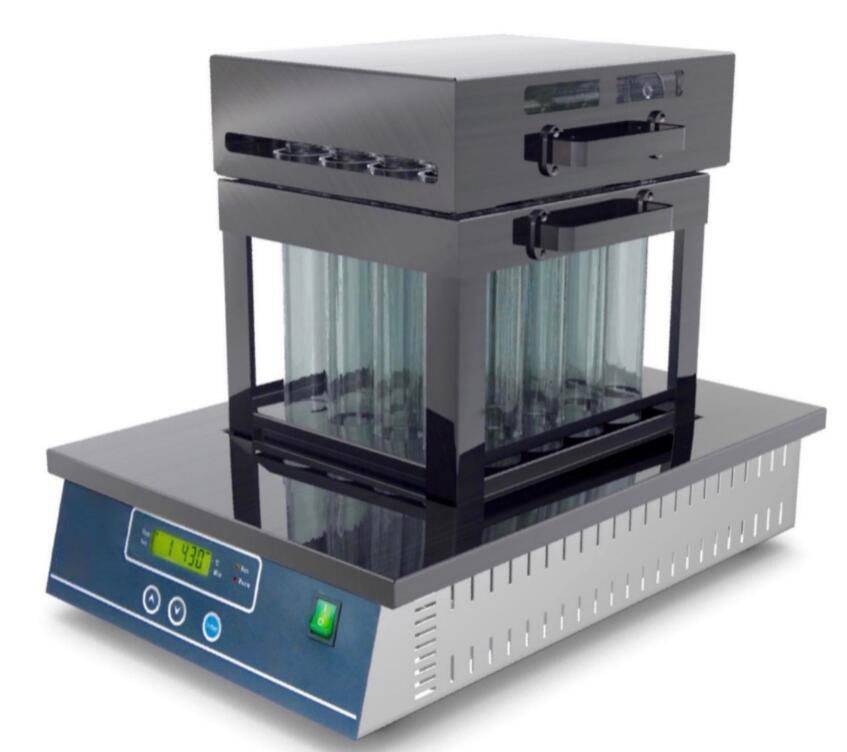
One of the key advantages of using a well-type electric heating system is its precision in controlling the temperature. This precision is crucial for maintaining the integrity of the samples and ensuring reproducible results. The electric heating system operates by directly applying heat to the sample, which minimizes energy loss and maximizes the efficiency of the digestion process. This direct heating method contrasts with other techniques that may involve indirect heating, which can lead to uneven temperature distribution and potentially compromise the quality of the analysis.
Moreover, the well-type design of the furnace allows for multiple samples to be processed simultaneously, thereby increasing throughput and reducing the time required for sample preparation. This feature is particularly beneficial in high-throughput laboratories where the demand for quick and accurate sample analysis is paramount. Additionally, the effective management of harmful gas emissions is a significant safety feature, as it prevents the release of toxic fumes into the laboratory environment, thereby protecting both the personnel and the equipment.
In summary, the digestion furnace, with its well-type electric heating system, offers a robust solution for accelerating sample digestion while ensuring environmental safety and operational efficiency. Its ability to handle multiple samples concurrently and its precise temperature control make it an indispensable tool in modern analytical laboratories.
Other Sample Preparation Equipment
Glue Spreader
The glue spreader is a specialized piece of equipment designed to precisely apply and evenly coat glue liquids onto various substrates. This process is achieved through the application of centrifugal force, which is meticulously controlled by adjusting the rotation speed and the viscosity of the glue solution.
By leveraging the principles of centrifugal force, the glue spreader ensures that the glue is distributed uniformly across the surface of the substrate. The rotation speed plays a crucial role in this process, as it directly influences the spread pattern and thickness of the glue layer. Higher rotation speeds generally result in thinner, more evenly distributed layers, while lower speeds may lead to thicker, less uniform coatings.
The viscosity of the glue solution is another critical factor that the glue spreader takes into account. A more viscous glue will require higher rotation speeds to achieve the same level of uniformity as a less viscous solution. Conversely, less viscous glues can be effectively spread at lower speeds, making the process more efficient and adaptable to different types of glue and substrate materials.
In summary, the glue spreader's ability to control both rotation speed and glue viscosity allows for precise and uniform application of glue liquids, which is essential for ensuring the integrity and performance of the final product.
Cutting Machine
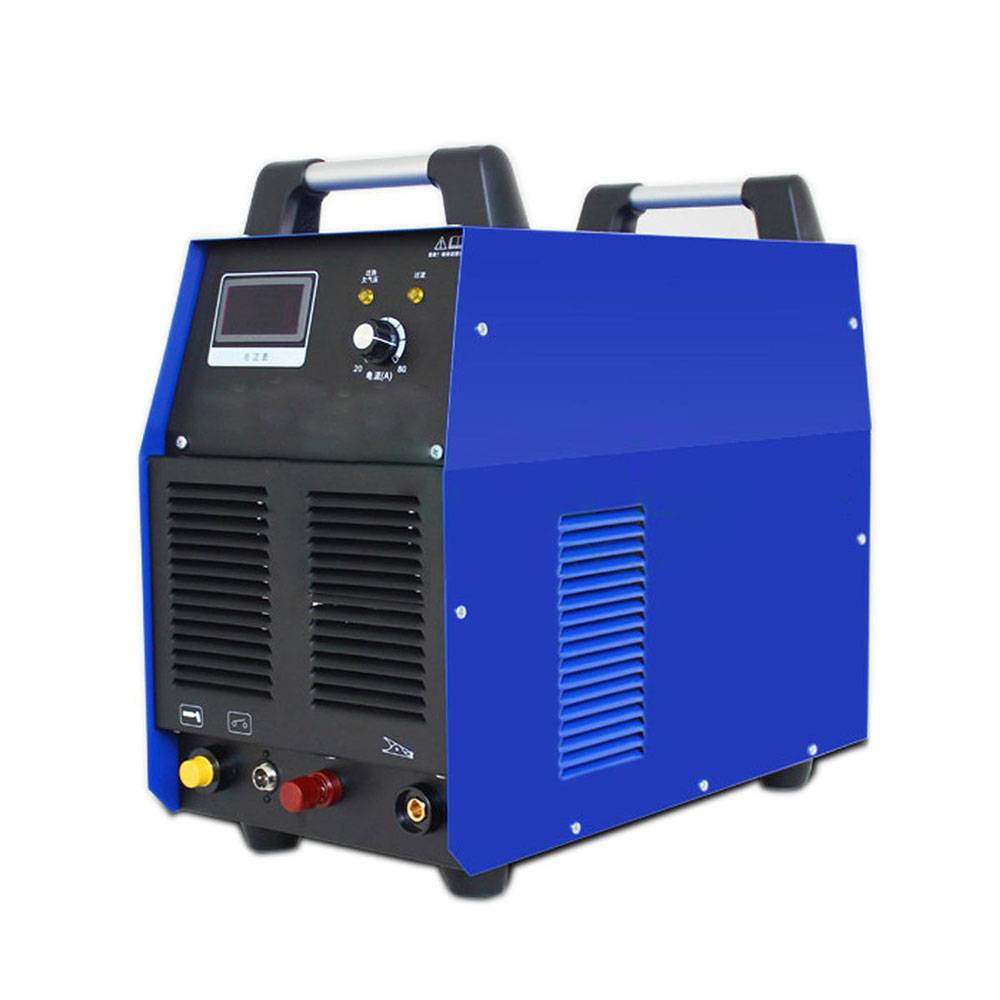
Cutting machines are indispensable tools in laboratory sample preparation, offering a variety of methods to precisely cut materials. These machines include:
- Flame Cutting Machines: Utilizing controlled flame to cut materials, ideal for high-temperature resistant samples.
- Plasma Cutting Machines: Employing ionized gas to cut through electrically conductive materials with high precision.
- Laser Cutting Machines: Using laser beams for ultra-precise cuts, suitable for delicate and intricate sample geometries.
- Water Cutting Machines: Harnessing high-pressure water jets, often mixed with abrasive particles, for cutting hard materials without heat-induced damage.
Each type of cutting machine offers unique advantages in terms of cutting efficiency and accuracy, catering to different sample preparation needs in the laboratory.
Melting Machine
The melting machine is an indispensable tool in laboratory settings, specifically designed to prepare glass samples for detailed analysis. This equipment employs a variety of heating methods to achieve the necessary temperature for melting glass, ensuring that the samples are in a consistent and analyzable state.
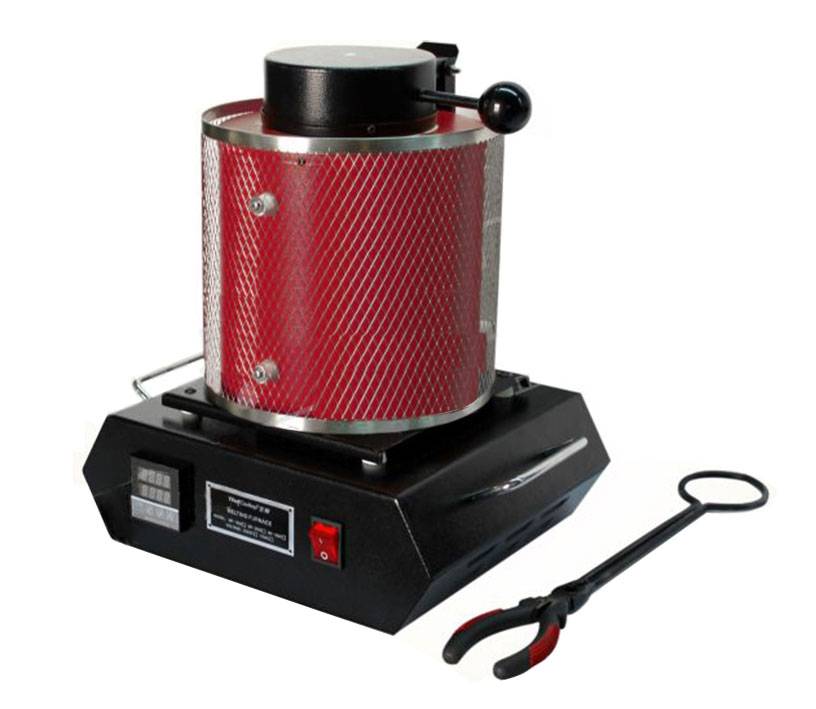
One of the primary methods used by melting machines is gas heating. This technique involves the controlled combustion of gases such as propane or natural gas to generate heat. The gas is typically fed through a burner system that directs the flame towards the sample, facilitating even and rapid melting.
Another common method is resistance radiation heating. In this process, the sample is placed within a chamber where it is exposed to intense radiation from high-resistance elements. These elements emit heat in the form of infrared radiation, which penetrates the glass sample, causing it to melt uniformly.
High-frequency induction heating is also a favored method for melting glass. This technique uses electromagnetic fields to induce currents within the sample, which in turn generate heat due to the resistance of the glass to these currents. The advantage of this method is its ability to precisely control the temperature and heating rate, ensuring that the glass melts without degradation or contamination.
Each of these heating methods offers unique advantages in terms of control, efficiency, and precision, making the melting machine a versatile and essential piece of equipment in any laboratory focused on glass analysis.
Tablet Press
The tablet press is an essential piece of machinery in the pharmaceutical industry, designed to automate the production of tablets by compressing powder into uniform shapes and sizes. This process, known as compression, relies on the interaction of two punches and a die, collectively referred to as the station. The upper and lower punches collaborate to compress the powder within the die, resulting in the formulation of tablets.
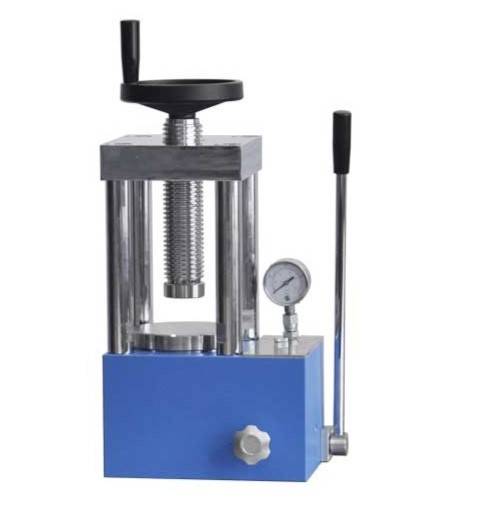
Tablet presses are versatile, capable of fabricating tablets in various sizes and shapes for a multitude of industries, including cosmetics, nutraceuticals, ayurvedic medicine, fitness supplements, herbs, confectionery, industrial pellets, cleaning products, and even mining applications. The evolution of tablet presses has been driven by the growing population's demand for tablets and the stringent regulations, such as CGMP (Current Good Manufacturing Process), that ensure the quality and safety of pharmaceutical products.
Working Principle
The operation of a tablet press involves a two-step process. Initially, the bottom punch descends into the die, creating a cavity that is then filled with powder. Excess powder is scraped off, and the top punch descends to compress the powder. High force is applied via compression rolls, bonding the granulated material and shaping it into a hard tablet. Post-compression, the lower punch elevates, ejecting the tablet from the die. The hydraulic pressure mechanism ensures uniform pressure distribution, with the ability to adjust the force applied for different tablet formulations.
Salient Features
Small tablet presses, in particular, boast several noteworthy features:
- Compact GMP Model: Designed to meet Good Manufacturing Practice standards.
- Motorized and Hand Wheel Systems: Offering flexibility in operation.
- SS Coverings: All moving parts are covered with stainless steel for safety.
- Heavy-Duty Structure: Constructed from painted MS material to prevent vibration during operation.
- Outside Hopper: Facilitates easy powder feeding.
- Easily Dismantled Parts: All contact parts can be quickly dismantled for thorough cleaning.
- Hard Chrome Plated Die Punch: Ensures rust-free operation.
- Small Footprint: Makes the machine easily movable and adaptable to various lab setups.
These features collectively ensure that tablet presses are not only efficient but also compliant with industry standards, making them indispensable in modern pharmaceutical manufacturing.
Crusher
Crushers are essential tools in laboratory sample preparation, designed to reduce solid raw materials to the required sizes efficiently. Unlike traditional methods that rely on screening processes, crushers leverage high-speed impact and wind energy to achieve this reduction. This innovative approach not only speeds up the process but also ensures a more uniform particle size distribution, which is crucial for accurate analysis.
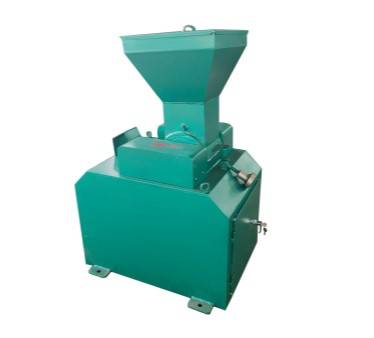
The operation of a crusher involves subjecting the raw materials to intense mechanical forces. High-speed impact mechanisms, often powered by electric motors, generate the necessary energy to break down the materials. Simultaneously, the incorporation of wind energy helps in the dispersion and further fragmentation of the particles. This dual-action method minimizes the need for subsequent screening, streamlining the sample preparation workflow.
Moreover, the elimination of traditional screening processes in crushers enhances the overall efficiency and precision of laboratory operations. By reducing the time and labor required for sample preparation, crushers contribute to faster turnaround times and more reliable analytical results. This makes them indispensable in environments where rapid and accurate sample processing is paramount, such as in pharmaceutical research, environmental testing, and materials science.
Grinding Machine
Grinding machines are essential tools in laboratory sample preparation, designed to achieve high-precision grinding and polishing of various surfaces on workpieces. These machines utilize abrasive tools, such as grinding wheels or abrasive belts, to remove material from the workpiece surface, resulting in a smoother and more precise finish.
The primary function of a grinding machine is to refine the surface of a workpiece, whether it be metal, glass, or other materials, to meet specific dimensional and surface quality requirements. This process is crucial in preparing samples for further analysis or for achieving a polished appearance in finished products.
Grinding machines operate through controlled abrasion, where the abrasive tools interact with the workpiece to remove small particles of material. The level of precision achieved depends on factors such as the type of abrasive used, the pressure applied, and the rotational speed of the grinding tool. For instance, finer abrasives are typically used for polishing, while coarser abrasives are employed for more aggressive material removal.
In laboratory settings, grinding machines are often used in conjunction with other sample preparation equipment, such as crushers and cutting machines, to create a comprehensive workflow for preparing samples for analysis. This integrated approach ensures that each step in the sample preparation process is optimized for accuracy and efficiency.
The versatility of grinding machines makes them indispensable in various industries, including metallurgy, electronics, and pharmaceuticals. They are particularly useful in applications where high surface finish and dimensional accuracy are critical, such as in the production of precision components or in the preparation of samples for microscopy and spectroscopy.
In summary, grinding machines play a pivotal role in laboratory sample preparation by providing the means to achieve high-precision grinding and polishing, essential for ensuring the quality and accuracy of subsequent analytical processes.
CONTACT US FOR A FREE CONSULTATION
KINTEK LAB SOLUTION's products and services have been recognized by customers around the world. Our staff will be happy to assist with any inquiry you might have. Contact us for a free consultation and talk to a product specialist to find the most suitable solution for your application needs!