Lamination and co-extrusion are both processes used in material manufacturing to combine layers with different properties, but they differ significantly in their methods and outcomes. Lamination involves bonding pre-formed layers together using adhesives or heat, which can sometimes lead to delamination over time. Co-extrusion, on the other hand, extrudes multiple materials simultaneously through a single die, creating a seamless bond between layers that prevents delamination. This makes co-extruded materials more durable and reliable for applications where layer separation is a concern. Below, we explore the key differences between these two processes in detail.
Key Points Explained:
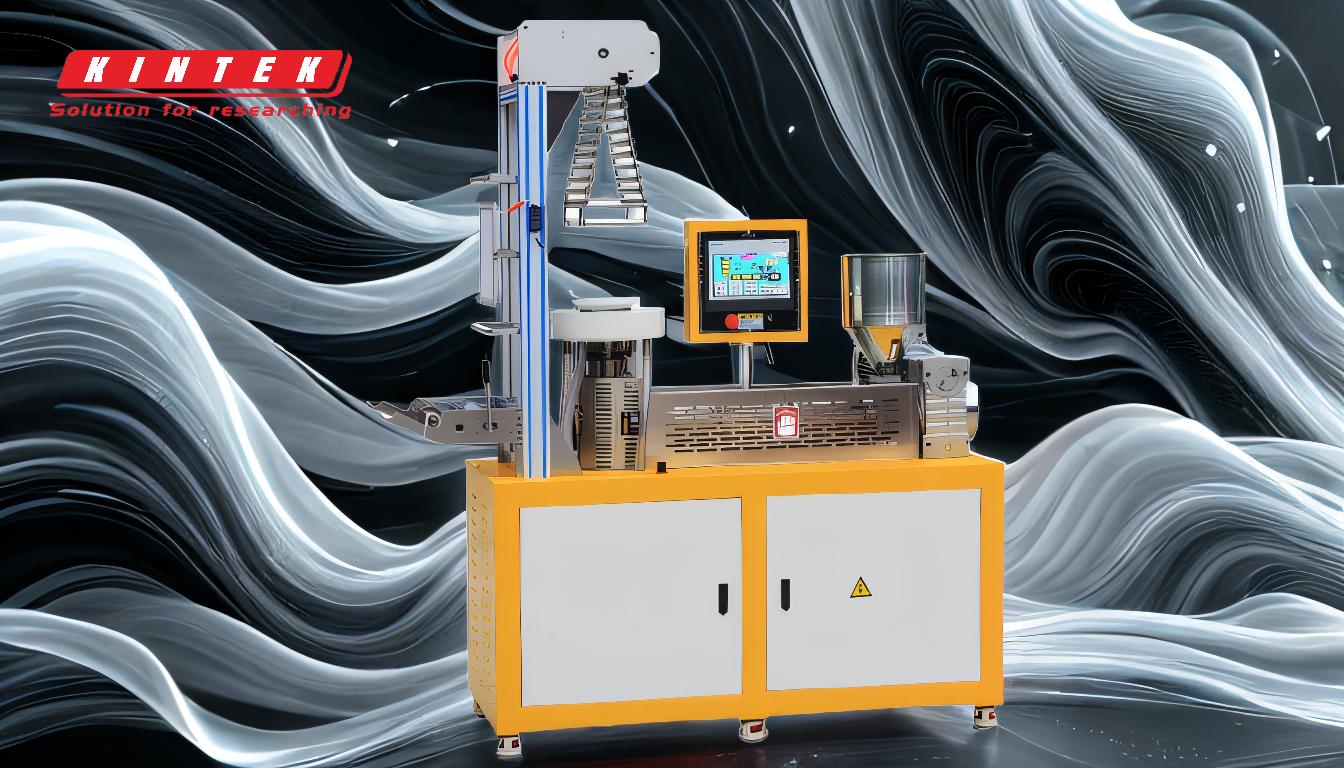
-
Process Methodology:
- Lamination: Involves bonding pre-formed layers of material together using adhesives, heat, or pressure. This process can be done in multiple steps, where each layer is prepared separately before being combined.
- Co-extrusion: Involves extruding multiple materials simultaneously through a single die. The materials are melted and forced through the die together, creating a single, unified product with distinct layers.
-
Bonding Mechanism:
- Lamination: The bonding between layers is achieved through external means such as adhesives or heat. This can sometimes result in weaker bonds, especially if the adhesive fails or the heat application is uneven.
- Co-extrusion: The layers are bonded during the extrusion process itself, creating a seamless and strong bond between the materials. This intrinsic bonding prevents the layers from separating over time.
-
Risk of Delamination:
- Lamination: There is a risk of delamination, where the layers can separate over time due to environmental factors, mechanical stress, or adhesive failure.
- Co-extrusion: Delamination is virtually impossible because the layers are fused together during the extrusion process, creating a more durable and reliable product.
-
Material Properties:
- Lamination: Allows for the combination of materials with very different properties, such as plastic and metal, but the final product's properties are limited by the bonding method used.
- Co-extrusion: Enables the combination of materials with different properties, such as flexibility and rigidity, but with the added benefit of a seamless bond that enhances the overall performance of the material.
-
Applications:
- Lamination: Commonly used in applications where the aesthetic appearance or specific surface properties are important, such as in packaging, flooring, and decorative panels.
- Co-extrusion: Often used in applications where durability and resistance to environmental factors are critical, such as in medical tubing, automotive parts, and industrial films.
-
Cost and Complexity:
- Lamination: Generally less complex and can be more cost-effective for certain applications, especially when dealing with large or irregularly shaped materials.
- Co-extrusion: Can be more complex and costly due to the need for specialized equipment and precise control over the extrusion process. However, the benefits of a seamless bond and reduced risk of delamination often justify the higher cost.
In summary, while both lamination and co-extrusion are used to create multi-layered materials, they differ in their processes, bonding mechanisms, and the resulting product properties. Co-extrusion offers a more durable and reliable solution by creating a seamless bond between layers, making it ideal for applications where delamination is a concern. Lamination, on the other hand, is often chosen for its simplicity and cost-effectiveness, particularly in applications where surface properties and aesthetics are more important than structural integrity.
Summary Table:
Aspect | Lamination | Co-Extrusion |
---|---|---|
Process Methodology | Bonds pre-formed layers using adhesives, heat, or pressure. | Extrudes multiple materials simultaneously through a single die. |
Bonding Mechanism | External bonding (adhesives/heat) may result in weaker bonds. | Intrinsic bonding during extrusion creates a seamless, strong bond. |
Risk of Delamination | Higher risk due to adhesive failure or environmental factors. | Virtually no risk; layers are fused together during extrusion. |
Material Properties | Combines materials with different properties but limited by bonding method. | Enhances material performance with seamless bonding. |
Applications | Used in packaging, flooring, and decorative panels. | Ideal for medical tubing, automotive parts, and industrial films. |
Cost and Complexity | Less complex and cost-effective for large or irregular materials. | More complex and costly but offers superior durability and reliability. |
Need help choosing the right process for your materials? Contact our experts today to get started!