Activated carbon is widely used for adsorption due to its high surface area and porosity. Over time, its adsorption capacity diminishes as pores become filled with contaminants. To restore its effectiveness, two methods are commonly employed: regeneration and reactivation. Regeneration involves milder processing conditions, such as washing or steaming, to remove adsorbed contaminants without significantly altering the carbon structure. Reactivation, on the other hand, uses high-temperature processes to burn off contaminants and restore porosity, often resulting in a more thorough restoration of adsorption capacity. Understanding the differences between these methods is crucial for selecting the appropriate restoration technique based on the specific application and desired outcomes.
Key Points Explained:
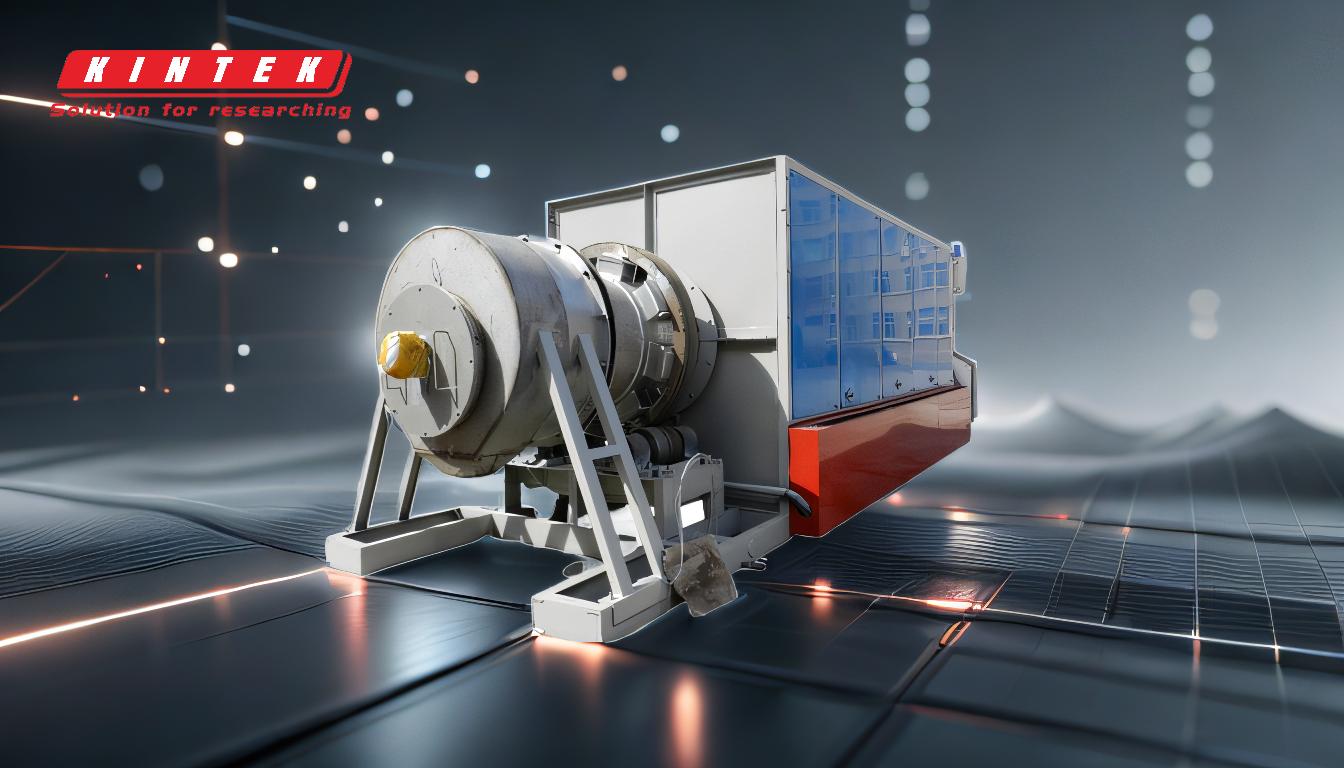
-
Definition of Regeneration:
- Regeneration refers to the process of restoring the adsorption capacity of activated carbon through milder methods.
- Common techniques include washing with solvents, steaming, or chemical treatments to remove adsorbed contaminants.
- This method is less aggressive and aims to partially restore the carbon's porosity and capacity without significantly altering its structure.
-
Definition of Reactivation:
- Reactivation involves a more intensive process, typically using high temperatures (600–900°C) in a controlled environment.
- The high heat burns off organic contaminants and restores the carbon's porosity more thoroughly than regeneration.
- This method is more effective in fully restoring the carbon's adsorption capacity but may also result in some loss of carbon mass.
-
Key Differences Between Regeneration and Reactivation:
- Temperature: Regeneration uses lower temperatures, while reactivation requires high temperatures.
- Extent of Restoration: Regeneration partially restores capacity, whereas reactivation provides a more complete restoration.
- Carbon Structure: Regeneration preserves the carbon structure, while reactivation may alter it due to high heat.
- Applications: Regeneration is suitable for less contaminated carbon or applications requiring frequent reuse. Reactivation is better for heavily contaminated carbon or when maximum capacity restoration is needed.
-
Advantages and Disadvantages:
-
Regeneration:
- Advantages: Lower energy consumption, cost-effective, preserves carbon structure.
- Disadvantages: Partial restoration, may not remove all contaminants.
-
Reactivation:
- Advantages: Thorough restoration of capacity, effective for heavily contaminated carbon.
- Disadvantages: Higher energy consumption, potential loss of carbon mass, more expensive.
-
Regeneration:
-
Choosing the Right Method:
- The choice between regeneration and reactivation depends on factors such as the level of contamination, desired restoration level, and cost considerations.
- For lightly contaminated carbon or frequent reuse, regeneration is often sufficient.
- For heavily contaminated carbon or when maximum adsorption capacity is required, reactivation is the preferred method.
-
Environmental and Economic Considerations:
- Regeneration is more environmentally friendly due to lower energy consumption and reduced carbon loss.
- Reactivation, while more resource-intensive, may be justified for high-value applications where maximum performance is critical.
By understanding these differences, users can make informed decisions about the appropriate restoration method for their activated carbon, ensuring optimal performance and cost-effectiveness.
Summary Table:
Aspect | Regeneration | Reactivation |
---|---|---|
Temperature | Lower temperatures (e.g., washing, steaming) | High temperatures (600–900°C) |
Extent of Restoration | Partial restoration of adsorption capacity | Complete restoration of adsorption capacity |
Carbon Structure | Preserves carbon structure | May alter carbon structure due to high heat |
Applications | Suitable for lightly contaminated carbon or frequent reuse | Ideal for heavily contaminated carbon or maximum capacity restoration |
Advantages | Lower energy consumption, cost-effective, preserves carbon structure | Thorough restoration, effective for heavily contaminated carbon |
Disadvantages | Partial restoration, may not remove all contaminants | Higher energy consumption, potential carbon mass loss, more expensive |
Need help choosing the right method for your activated carbon? Contact our experts today for personalized advice!