Sputtering and deposition are both techniques used to create thin films, but they differ significantly in their mechanisms and applications. Sputtering is a physical process where atoms are ejected from a solid target material due to bombardment by energetic ions, typically from a plasma. These ejected atoms then deposit onto a substrate to form a thin film. Deposition, on the other hand, is a broader term that encompasses various methods, including chemical vapor deposition (CVD), where a chemical reaction occurs to form a coating on the substrate. Sputtering is a type of physical vapor deposition (PVD) and is often preferred for applications requiring precise control over film properties, such as in optical coatings and semiconductor manufacturing.
Key Points Explained:
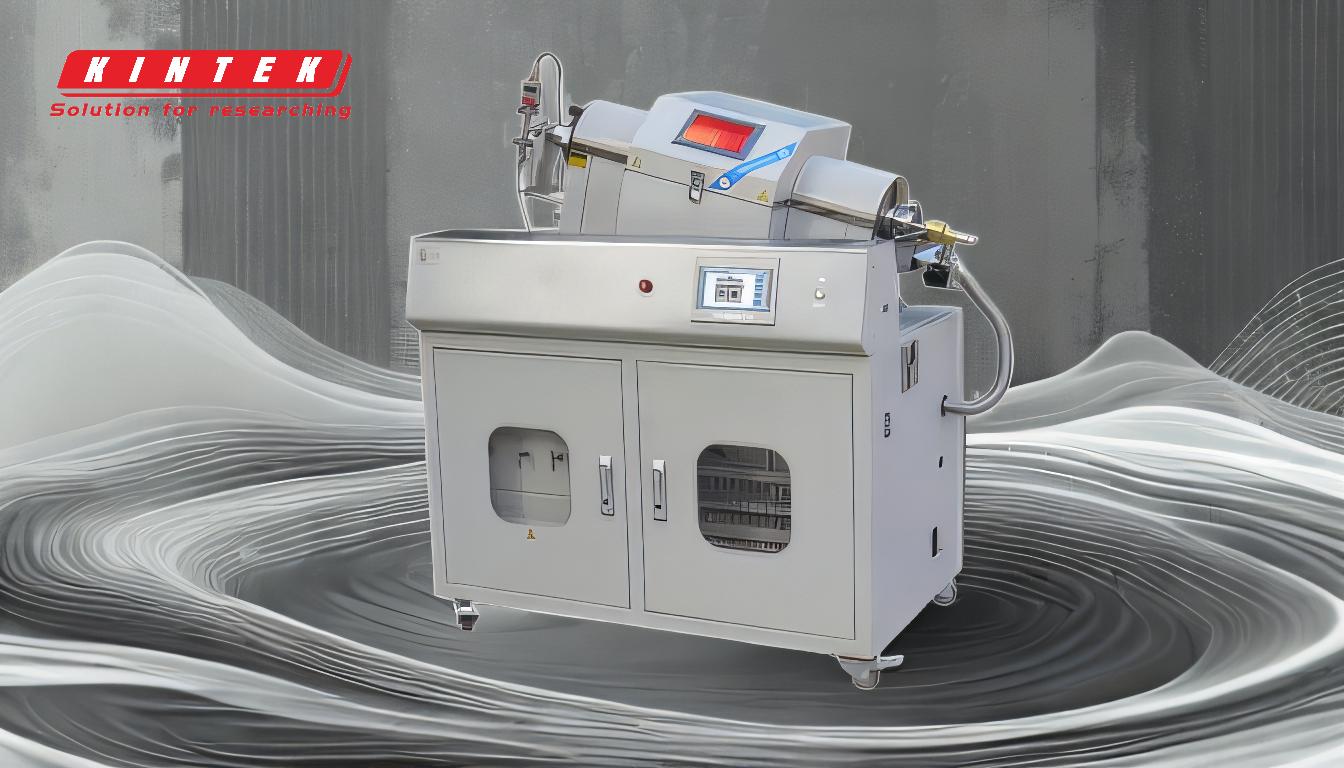
-
Mechanism of Sputtering:
- Sputtering involves the ejection of atoms from a target material due to bombardment by energetic ions, typically from a plasma. This process is purely physical, relying on momentum transfer rather than chemical reactions.
- The sputtered atoms travel through a vacuum or low-pressure environment and then deposit onto a substrate, forming a thin film. This method is known for its ability to produce high-quality, uniform coatings.
-
Mechanism of Deposition:
- Deposition is a broader term that includes various techniques, such as chemical vapor deposition (CVD) and physical vapor deposition (PVD). CVD involves chemical reactions between precursors to form coating molecules, which then condense on a cooler substrate.
- Unlike sputtering, CVD can produce films with complex compositions and structures, making it suitable for applications like creating polycrystalline silicon films for integrated circuits.
-
Process Steps in Sputtering:
- Ramp Up: The vacuum chamber is prepared by gradually increasing temperature and decreasing pressure.
- Etching: The substrate is cleaned using cathodic cleaning to remove surface contaminants.
- Coating: The target material is bombarded with ions, causing atoms to be ejected and deposited onto the substrate.
- Ramp Down: The chamber is returned to room temperature and ambient pressure using a cooling system.
-
Types of Sputtering:
- Sputtering techniques include RF and DC magnetron sputtering, ion beam sputtering, and reactive sputtering. Each method has specific applications and advantages, such as the ability to deposit materials with high precision or to create films with specific properties.
-
Applications of Sputtering and Deposition:
- Sputtering: Commonly used in applications requiring precise control over film properties, such as optical coatings, semiconductor manufacturing, and decorative finishes.
- Deposition (CVD): Often used in the production of integrated circuits, solar cells, and other electronic components where complex film compositions and structures are required.
-
Comparison of Sputtering and CVD:
- Sputtering: A physical process that does not involve melting the material. It is preferred for coatings that improve optical properties and for applications requiring high precision.
- CVD: A chemical process that involves the reaction of precursors to form coating molecules. It is suitable for creating films with complex compositions and is widely used in the electronics industry.
In summary, while both sputtering and deposition are used to create thin films, they differ in their mechanisms, process steps, and applications. Sputtering is a physical process that offers precise control over film properties, making it ideal for specific applications like optical coatings and semiconductor manufacturing. Deposition, particularly CVD, involves chemical reactions and is used for creating films with complex compositions, such as in the production of integrated circuits.
Summary Table:
Aspect | Sputtering | Deposition (CVD) |
---|---|---|
Mechanism | Physical process: Ejection of atoms via ion bombardment. | Chemical process: Reaction of precursors to form coating molecules. |
Process Steps | Ramp Up → Etching → Coating → Ramp Down | Precursor reaction → Condensation on substrate. |
Applications | Optical coatings, semiconductors, decorative finishes. | Integrated circuits, solar cells, electronic components. |
Key Advantages | Precise control, high-quality, uniform coatings. | Complex film compositions, suitable for electronics. |
Need help choosing the right thin film technique for your project? Contact our experts today!