Rolling mills are essential equipment in metalworking, used to shape and process metals into various forms like bars, rods, plates, and more. The primary difference between two-high and three-high rolling mills lies in their design, operational efficiency, and functionality. A two-high rolling mill consists of two rolls rotating in opposite directions, while a three-high rolling mill adds a middle roll that rotates in the opposite direction to the top and bottom rolls. This design allows for continuous rolling without reversing the direction of the drive, making three-high mills more efficient and easier to use compared to two-high mills. Below, we explore the key differences and advantages of each type in detail.
Key Points Explained:
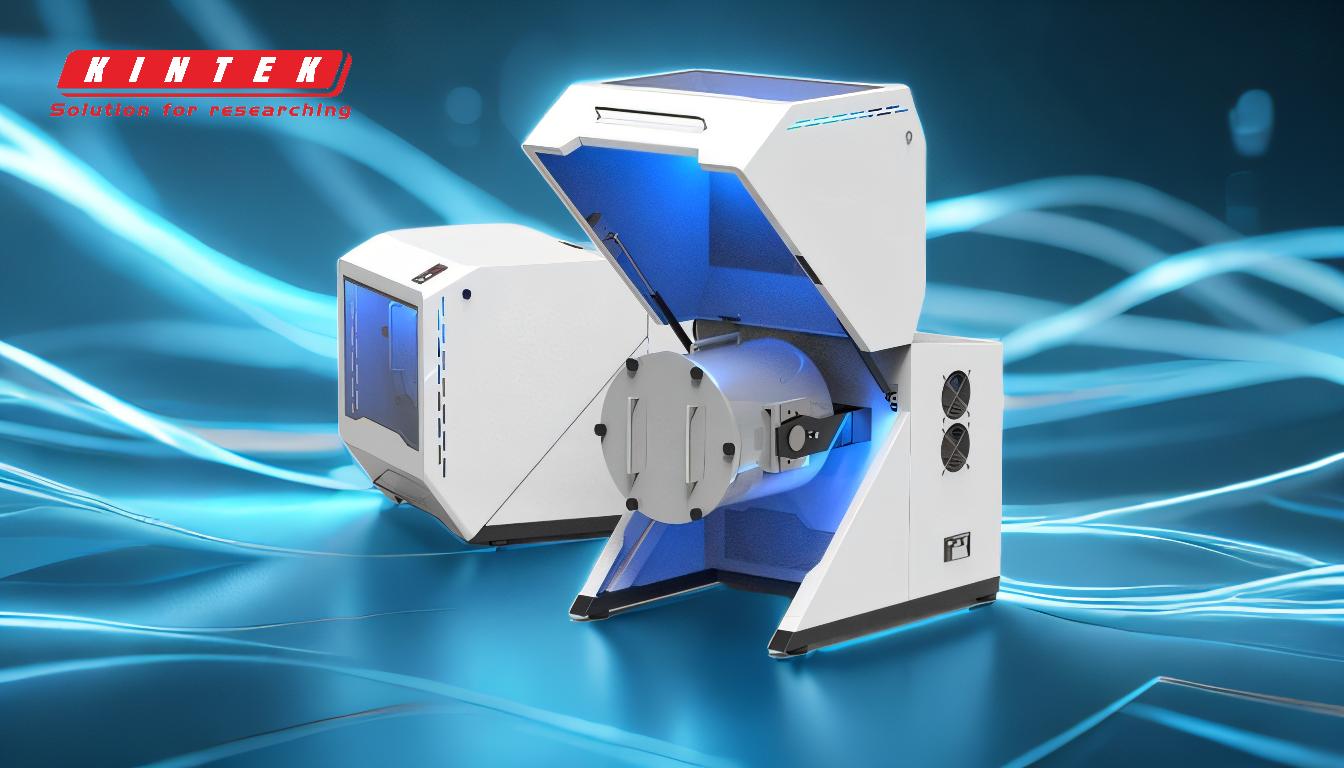
-
Design and Configuration:
- Two-High Rolling Mills: These mills consist of two horizontal rolls stacked vertically. The rolls rotate in opposite directions, allowing the metal to pass through and be shaped. After each pass, the direction of the rolls may need to be reversed to bring the metal back for further processing.
- Three-High Rolling Mills: These mills add a third, middle roll that rotates in the opposite direction to the top and bottom rolls. This configuration eliminates the need to reverse the direction of the drive between passes, enabling continuous rolling.
-
Operational Efficiency:
- Two-High Rolling Mills: While effective, these mills require reversing the roll direction after each pass, which can slow down the rolling process and reduce overall efficiency.
- Three-High Rolling Mills: The addition of the middle roll allows for continuous rolling without reversing the drive direction, significantly improving efficiency and reducing downtime.
-
Ease of Use:
- Two-High Rolling Mills: These mills are simpler in design but may require more manual intervention, such as reversing the roll direction, which can complicate operations.
- Three-High Rolling Mills: The continuous rolling process makes these mills easier to operate, as there is no need to stop and reverse the rolls between passes.
-
Applications:
- Both types of rolling mills are used in the production of bars, rods, wire rods, bands, hoops, metal shapes, plates, and even jewelry. However, the choice between the two depends on the specific requirements of the production process, such as the need for continuous rolling or the type of metal being processed.
-
Specifications and Considerations:
- When selecting a rolling mill, important specifications to consider include roll diameter, the type of metal to be rolled, work rolls, back-up rolls, roll journal, maximum separation force at 1000 feet per minute (fpm), total column area, and estimated floor space. These factors will influence the choice between a two-high and three-high rolling mill based on the specific needs of the operation.
In summary, while both two-high and three-high rolling mills serve the same fundamental purpose of shaping and processing metals, the three-high rolling mill offers greater efficiency and ease of use due to its continuous rolling capability. The choice between the two will depend on the specific requirements of the production process, including the need for continuous operation and the type of metal being processed.
Summary Table:
Feature | Two-High Rolling Mill | Three-High Rolling Mill |
---|---|---|
Design | Two horizontal rolls stacked vertically | Three rolls: top, middle, and bottom, with the middle roll rotating oppositely |
Operational Efficiency | Requires reversing roll direction after each pass, reducing efficiency | Enables continuous rolling without reversing, improving efficiency |
Ease of Use | Simpler design but may require manual intervention for reversing | Easier to operate with no need to stop and reverse rolls |
Applications | Used for bars, rods, plates, and more; depends on production needs | Preferred for continuous rolling processes and high-efficiency operations |
Specifications | Roll diameter, metal type, work rolls, back-up rolls, roll journal, separation force, etc. | Similar considerations but optimized for continuous rolling and higher productivity |
Need help choosing the right rolling mill for your metalworking needs? Contact our experts today!