Wiped film distillation and thin film distillation are both advanced techniques used for separating and purifying substances, particularly in industries like cannabis extraction, pharmaceuticals, and chemical processing. While they share similarities, such as the creation of a thin film to enhance heat transfer, they differ in design, operation, and application. Wiped film distillation is a specialized form of short-path distillation that uses mechanical wipers to create a thin film on a heated surface, allowing for rapid evaporation and condensation. Thin film distillation, on the other hand, relies on gravity or other mechanisms to spread the material into a thin film, often requiring an external condenser. These differences impact their efficiency, scalability, and suitability for specific applications.
Key Points Explained:
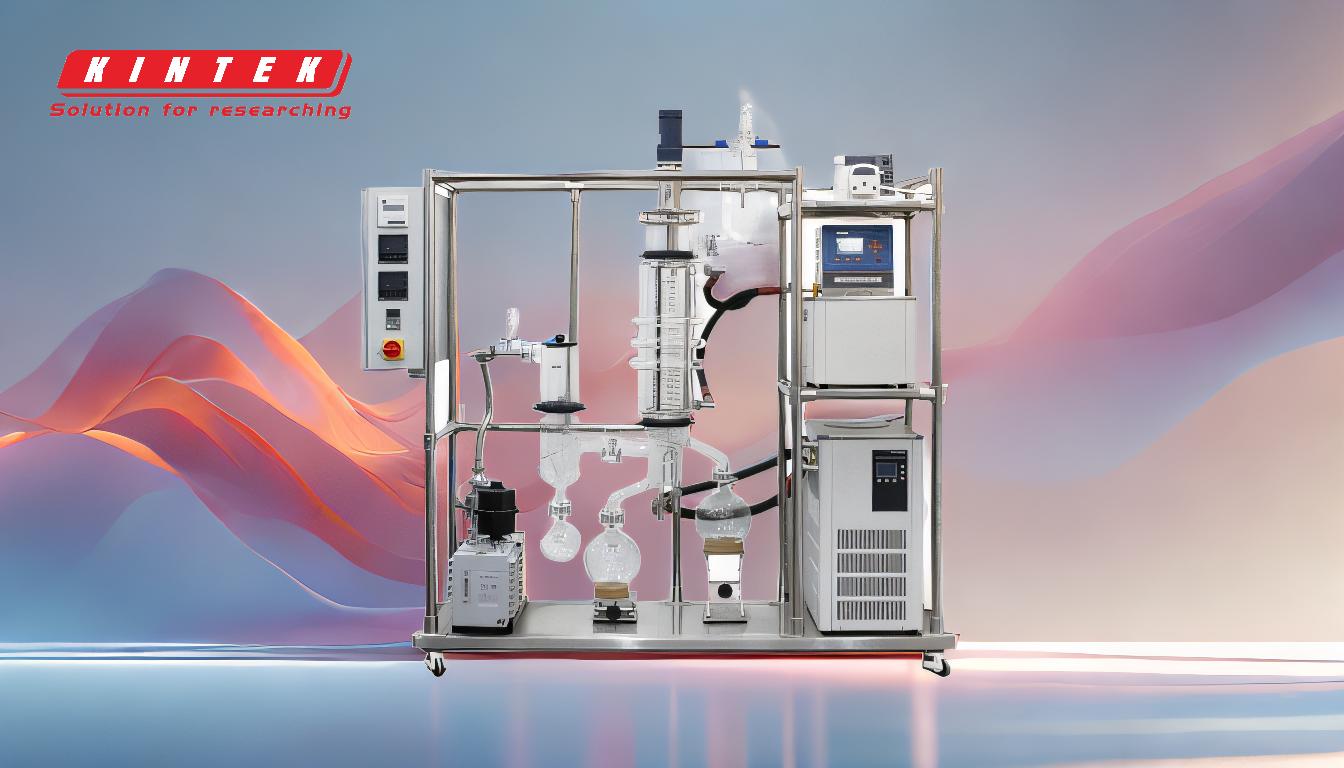
-
Design and Condenser Configuration:
- Wiped Film Distillation: This system features a built-in condenser, which is integrated into the distillation apparatus. The condenser is positioned close to the evaporator, allowing vapors to condense almost immediately after evaporation. This short-path design minimizes the distance vapors travel, reducing the risk of degradation or contamination.
- Thin Film Distillation: In contrast, thin film evaporators typically use an external condenser connected to the vapor phase outlet. This setup requires vapors to travel a longer distance before condensation, which can affect the purity and quality of the distillate, especially for heat-sensitive materials.
-
Mechanism of Film Formation:
- Wiped Film Distillation: Mechanical wipers or rollers are used to spread the crude oil into a thin film on the inner surface of a heated cylinder. This continuous wiping action ensures uniform heat distribution and efficient evaporation. The wipers also help reduce the residence time of the material on the heated surface, which is crucial for preserving the integrity of heat-sensitive compounds.
- Thin Film Distillation: The thin film is typically formed by gravity or centrifugal force as the material flows over a heated surface. While this method also creates a thin film, it lacks the mechanical agitation provided by wipers, which can result in less uniform heat transfer and longer residence times.
-
Residence Time and Scalability:
- Wiped Film Distillation: The residence time (the duration the material spends in contact with the heated surface) is significantly shorter, typically ranging from 1 to 3 minutes. This short exposure to heat minimizes thermal degradation, making it ideal for processing heat-sensitive materials like cannabinoids or essential oils. Additionally, wiped film systems are better suited for large-scale operations due to their continuous feed mechanism and higher throughput.
- Thin Film Distillation: The residence time is generally longer, often between 10 to 60 minutes, depending on the design and application. While this can result in higher-quality distillate for some applications, it limits scalability and is less efficient for large-scale production.
-
Efficiency and Suitability for Viscous Materials:
- Wiped Film Distillation: The mechanical wipers ensure efficient heat transfer, even for highly viscous materials. This makes wiped film distillation particularly effective for processing crude oils, resins, and other viscous substances. The continuous wiping action also prevents fouling or buildup on the heated surface, maintaining consistent performance over time.
- Thin Film Distillation: While it can handle a range of materials, thin film distillation may struggle with highly viscous substances due to the lack of mechanical agitation. The reliance on gravity or centrifugal force for film formation can lead to uneven heat distribution and reduced efficiency for thicker or more complex mixtures.
-
Applications and Product Quality:
- Wiped Film Distillation: This method is widely used in industries requiring high-purity distillates, such as cannabis extraction, where preserving the integrity of cannabinoids and terpenes is critical. The short residence time and efficient heat transfer result in a high-quality product with minimal thermal degradation.
- Thin Film Distillation: It is often employed in applications where longer residence times are acceptable or where the material is less sensitive to heat. While it can produce high-quality distillates, it is generally less efficient for heat-sensitive or viscous materials compared to wiped film distillation.
-
Cost and Maintenance:
- Wiped Film Distillation: The integration of mechanical wipers and a built-in condenser increases the complexity and cost of the system. However, the higher efficiency and scalability often justify the investment, especially for large-scale or high-throughput operations.
- Thin Film Distillation: These systems are generally simpler and less expensive to manufacture and maintain. However, the need for an external condenser and potential challenges with viscous materials may offset these cost advantages in certain applications.
In summary, while both wiped film and thin film distillation techniques aim to create a thin film for efficient heat transfer, they differ significantly in design, operation, and suitability for specific applications. Wiped film distillation excels in handling heat-sensitive and viscous materials, offering shorter residence times and higher scalability, making it ideal for large-scale, high-purity production. Thin film distillation, on the other hand, is simpler and more cost-effective but may struggle with highly viscous or heat-sensitive substances. The choice between the two depends on the specific requirements of the application, including the nature of the material, desired product quality, and production scale.
Summary Table:
Aspect | Wiped Film Distillation | Thin Film Distillation |
---|---|---|
Condenser Configuration | Built-in condenser for short-path distillation, minimizing vapor travel distance. | External condenser, requiring longer vapor travel distance. |
Film Formation | Mechanical wipers create a uniform thin film for efficient heat transfer. | Gravity or centrifugal force forms the film, lacking mechanical agitation. |
Residence Time | Short (1-3 minutes), ideal for heat-sensitive materials. | Longer (10-60 minutes), suitable for less heat-sensitive materials. |
Scalability | High scalability, ideal for large-scale production. | Limited scalability, better for smaller-scale operations. |
Efficiency with Viscous Materials | Handles viscous materials effectively due to mechanical wiping. | Struggles with highly viscous materials due to lack of mechanical agitation. |
Applications | High-purity distillates, cannabis extraction, pharmaceuticals. | Applications with longer residence times, less heat-sensitive materials. |
Cost and Maintenance | Higher initial cost but justified by efficiency and scalability. | Simpler and less expensive, but may face challenges with viscous materials. |
Need help choosing the right distillation technique for your application? Contact our experts today for personalized guidance!