Sieve shakers, while widely used for particle size analysis, come with several disadvantages that can affect their accuracy, reliability, and suitability for certain types of materials. These drawbacks include reduced accuracy for fine materials, assumptions about particle shape, limitations with elongated or flat particles, unsuitability for very small particles, potential particle size reduction, and issues with sieve maintenance. Understanding these limitations is crucial for selecting the right equipment and ensuring accurate results in particle size analysis.
Key Points Explained:
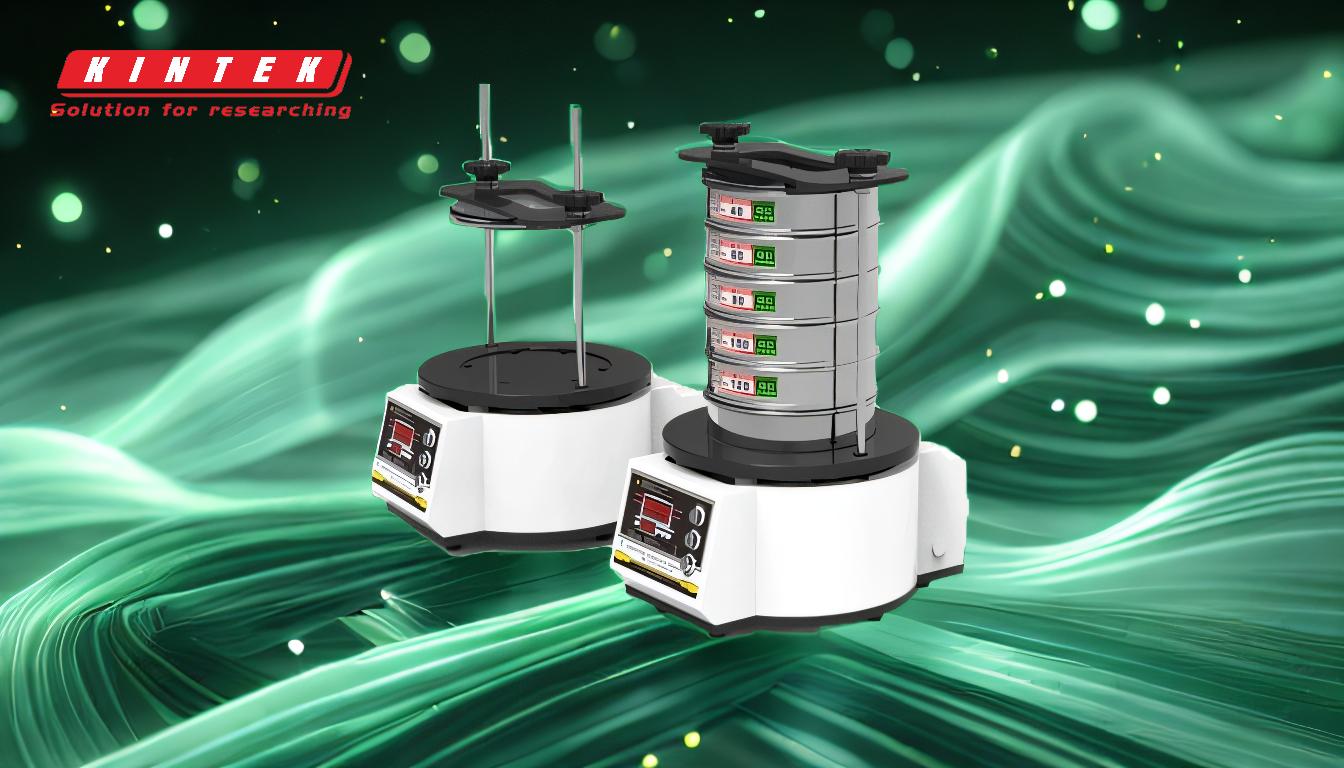
-
Reduced Accuracy for Fine Materials:
- Sieve shakers are less accurate for materials finer than 100 mesh. This is because smaller particles can pass through the sieve openings more easily, leading to less precise separation and measurement. The finer the material, the more challenging it becomes to achieve accurate and reproducible results.
-
Assumption of Particle Shape:
- Sieve analysis assumes that all particles are round or nearly spherical. However, many materials have irregular shapes, such as elongated or flat particles. This assumption can lead to unreliable mass-based results, as non-spherical particles may not pass through the sieve openings in the same way as spherical particles, skewing the size distribution data.
-
Unreliable Results for Elongated and Flat Particles:
- For elongated and flat particles, sieve shakers may provide unreliable mass-based results. These particles can orient themselves in ways that prevent them from passing through the sieve openings, leading to an overestimation of their size. This limitation is particularly problematic in industries where particle shape significantly impacts material properties.
-
Unsuitability for Particles Smaller Than 50 µm:
- Sieve shakers are generally unsuitable for particles smaller than 50 µm. At this size range, other methods like laser diffraction or dynamic light scattering are more appropriate. The limitations of sieve shakers in this context are due to the difficulty in accurately separating and measuring such small particles using traditional sieving methods.
-
Potential Particle Size Reduction:
- During the sieving process, there is a risk of further reducing the particle size, especially for brittle materials. This can occur due to the mechanical agitation of the sieve shaker, leading to particle breakage. Such unintended size reduction can introduce errors in the particle size distribution data, making it less representative of the original sample.
-
Sieve Clogging and Distortion:
- Sieves can become clogged or distorted if not properly handled and maintained. Clogging occurs when particles get stuck in the sieve openings, reducing the effective opening size and leading to inaccurate results. Distortion can happen due to improper cleaning or handling, which can alter the sieve's mesh size and affect the reproducibility of the analysis.
-
Variations in Mesh Weave:
- Variations in the weave of the mesh material can affect the reproducibility of test results. Even slight differences in the weave can lead to inconsistencies in the size of the sieve openings, which in turn affects the accuracy of the particle size distribution. This variability must be accounted for in data presentation and analysis.
-
Limited Number of Size Fractions:
- Sieve analysis typically provides a limited number of size fractions, usually up to 8 sieves. This restricts the resolution of the particle size distribution, making it less detailed compared to other methods that can provide a more continuous size distribution. The limited number of fractions can be a significant drawback when high-resolution data is required.
-
Time-Consuming Process:
- Sieve analysis can be a time-consuming process, especially when dealing with large sample sizes or materials that require extended sieving times to achieve accurate separation. This can be a disadvantage in settings where rapid results are needed.
-
Maintenance and Handling Requirements:
- Proper maintenance and handling of sieves are crucial to avoid issues like clogging and distortion. Regular cleaning and inspection are necessary to ensure the sieves remain in good condition. Failure to maintain the sieves properly can lead to inaccurate results and the need for frequent replacements, increasing the overall cost of the analysis.
In summary, while sieve shakers offer several advantages, such as simplicity and cost-effectiveness, they also come with notable disadvantages that can impact their accuracy and suitability for certain materials. Understanding these limitations is essential for making informed decisions about the use of sieve shakers in particle size analysis.
Summary Table:
Disadvantage | Description |
---|---|
Reduced Accuracy for Fine Materials | Less accurate for materials finer than 100 mesh. |
Assumption of Particle Shape | Assumes particles are spherical, leading to unreliable results for irregular shapes. |
Unreliable for Elongated/Flat Particles | Overestimates size due to particle orientation. |
Unsuitable for Particles < 50 µm | Other methods like laser diffraction are better for small particles. |
Potential Particle Size Reduction | Mechanical agitation may break brittle particles. |
Sieve Clogging and Distortion | Clogging and improper handling can lead to inaccurate results. |
Variations in Mesh Weave | Inconsistent sieve openings affect reproducibility. |
Limited Number of Size Fractions | Typically up to 8 sieves, restricting resolution. |
Time-Consuming Process | Extended sieving times for accurate separation. |
Maintenance and Handling Requirements | Regular cleaning and inspection are necessary to avoid inaccuracies. |
Need help choosing the right particle size analysis equipment? Contact our experts today for tailored solutions!