The effect of power in sputtering is significant as it directly influences the sputtering yield, deposition rate, and the quality of the deposited films. Power, particularly in the form of incident ion energy, determines the kinetic energy of the ions bombarding the target material, which in turn affects the number of target atoms ejected per incident ion (sputtering yield). Higher power levels generally increase the sputtering yield and deposition rate but must be balanced with other factors such as target material properties, chamber pressure, and the type of power source (DC or RF) to ensure optimal film quality and process efficiency.
Key Points Explained:
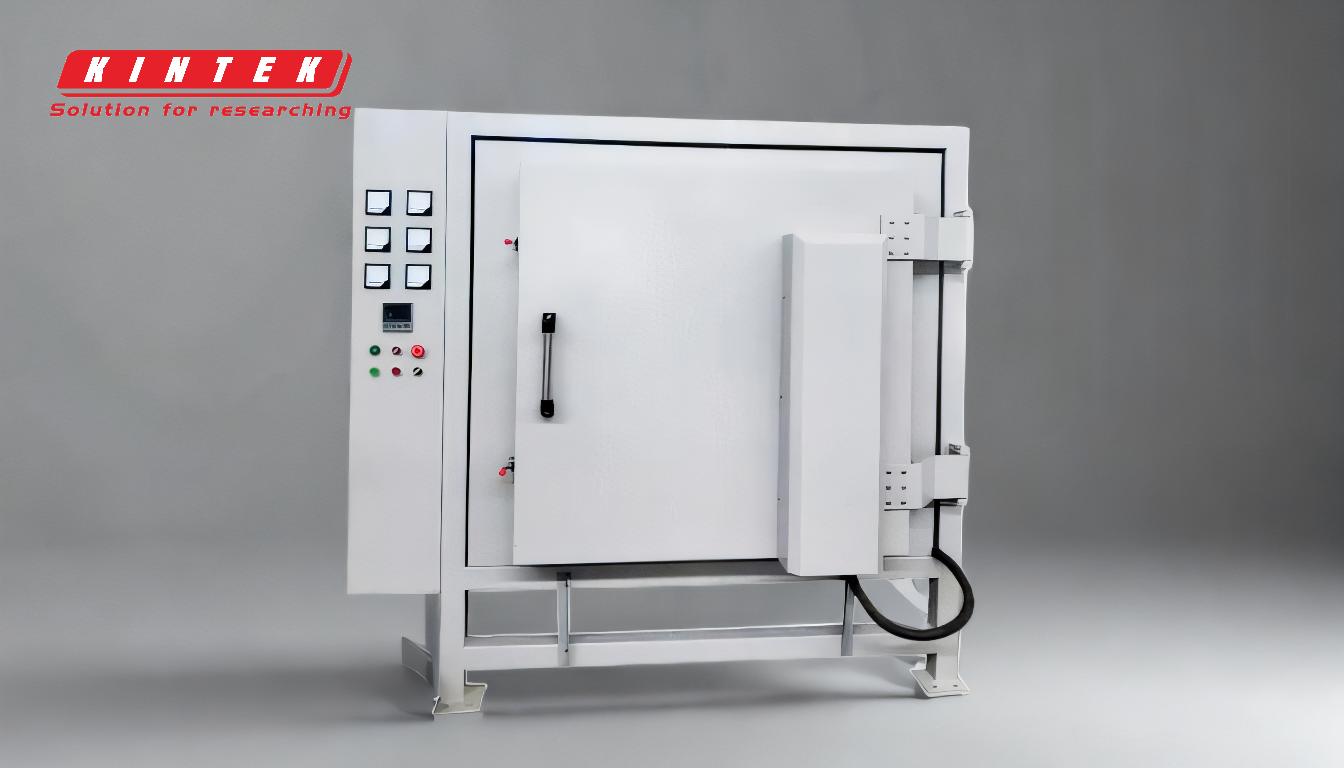
-
Impact of Power on Sputtering Yield:
- Definition: Sputtering yield is the number of target atoms ejected per incident ion.
- Influence of Power: Higher power levels increase the incident ion energy, leading to a higher sputtering yield. This is because more energy is transferred to the target atoms, causing more atoms to be ejected from the surface.
- Example: For a given target material, increasing the power from 100W to 200W might double the sputtering yield, depending on the material's properties and the sputtering conditions.
-
Effect on Deposition Rate:
- Direct Correlation: The deposition rate, or the rate at which material is deposited onto the substrate, is directly proportional to the sputtering yield. Higher power levels result in a higher deposition rate.
- Practical Consideration: In industrial applications, a higher deposition rate can lead to faster production times but may also require careful control to avoid defects in the film.
-
Quality of Deposited Films:
- Surface Mobility: Excess energy from high-power sputtering can increase the surface mobility of the deposited atoms, leading to better film quality with fewer defects.
- Trade-offs: While higher power can improve film quality, it can also lead to issues such as increased stress in the film or unwanted reactions with the substrate material.
-
Role of Power Source (DC vs. RF):
- DC Sputtering: Typically used for conductive materials. Higher DC power increases the sputtering rate but may limit the types of materials that can be effectively sputtered.
- RF Sputtering: Suitable for both conductive and insulating materials. RF power allows for better control over the sputtering process, enabling the deposition of high-quality films on a wider range of substrates.
-
Interaction with Chamber Pressure:
- High Pressure: At higher chamber pressures, the increased collisions between ions and gas atoms can moderate the energy of the ions, affecting the sputtering process. Higher power can help maintain the desired sputtering yield despite these collisions.
- Low Pressure: Lower pressures allow for high-energy ballistic impact, where higher power can significantly increase the sputtering yield and deposition rate.
-
Material Compatibility and Cost:
- Material Considerations: Different materials respond differently to power levels. For example, some materials may require higher power to achieve a reasonable sputtering yield, while others may be more sensitive to power changes.
- Cost Implications: Higher power levels can increase operational costs due to higher energy consumption and potential wear on equipment. Balancing power with other process parameters is crucial for cost-effective sputtering.
In summary, power is a critical factor in the sputtering process, influencing the sputtering yield, deposition rate, and film quality. The choice of power level must be carefully considered in conjunction with other factors such as target material properties, chamber pressure, and the type of power source to optimize the sputtering process for specific applications.
Summary Table:
Factor | Impact of Power |
---|---|
Sputtering Yield | Higher power increases ion energy, boosting the number of atoms ejected per ion. |
Deposition Rate | Directly proportional to sputtering yield; higher power = faster deposition. |
Film Quality | Higher power improves surface mobility, reducing defects but may increase stress. |
Power Source (DC/RF) | DC for conductive materials; RF for conductive and insulating materials. |
Chamber Pressure | High pressure moderates ion energy; low pressure enhances high-energy impact. |
Material & Cost | Material compatibility and energy costs must be balanced for optimal sputtering. |
Ready to optimize your sputtering process? Contact our experts today for tailored solutions!