Sputter deposition is a physical vapor deposition (PVD) technique used to deposit thin films onto substrates. It involves bombarding a target material with high-energy ions, typically from an argon plasma, which ejects atoms from the target. These ejected atoms then travel through a vacuum and deposit onto a substrate, forming a thin film. The process is driven by the phenomenon of sputtering, where ions collide with the target material, dislodging atoms that subsequently condense on the substrate. This method is widely used in industries such as semiconductor manufacturing, optics, and solar cell production due to its ability to produce high-quality, uniform coatings.
Key Points Explained:
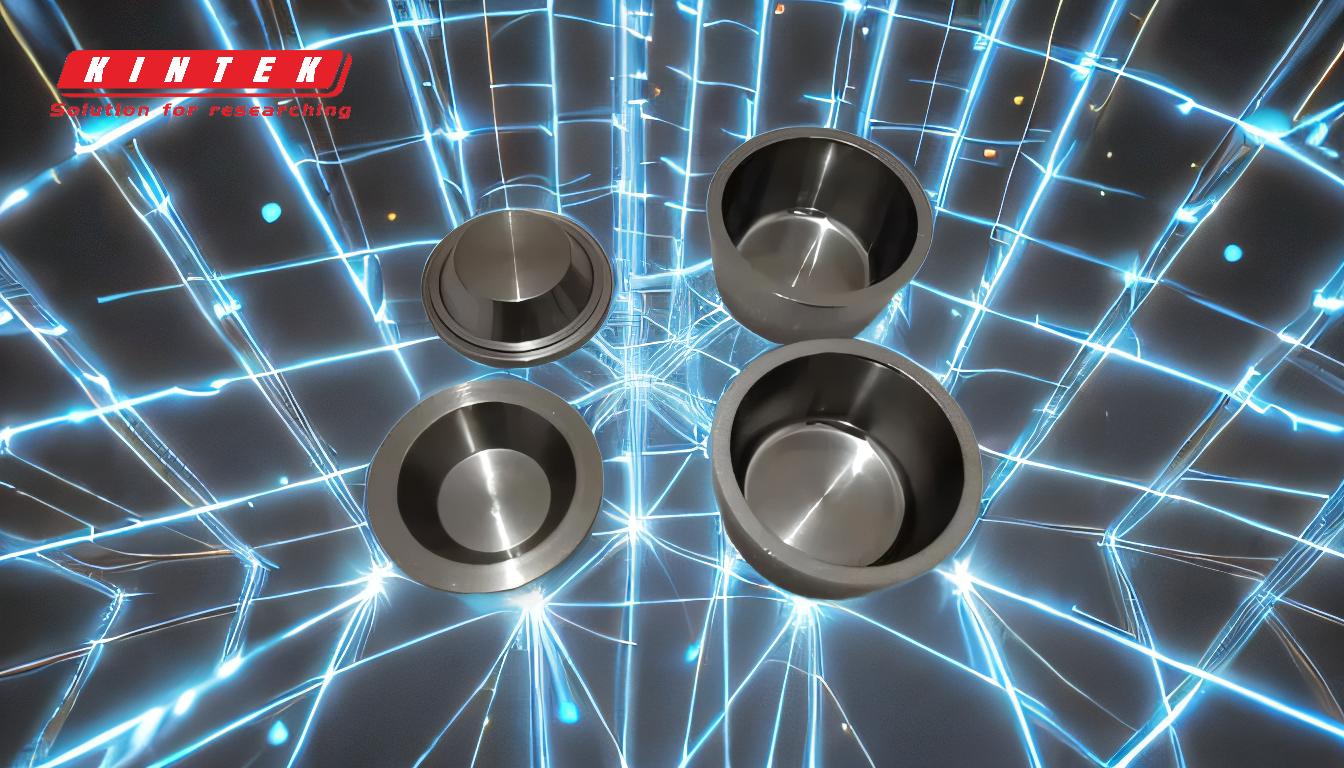
-
Definition and Overview of Sputter Deposition:
- Sputter deposition is a type of physical vapor deposition (PVD) used to create thin films on substrates.
- It involves the ejection of atoms from a target material through bombardment by high-energy ions, typically argon ions from a plasma.
- The ejected atoms travel through a vacuum and deposit onto a substrate, forming a thin film.
-
The Role of Plasma and Ions:
- A plasma is created in the vacuum chamber using an inert gas, usually argon.
- The plasma contains positively charged argon ions and free electrons.
- The ions are accelerated towards the target material (cathode) due to an applied electric field, gaining sufficient energy to dislodge atoms from the target upon impact.
-
Sputtering Phenomenon:
- Sputtering occurs when high-energy ions collide with the target material, transferring their energy to the target atoms.
- This energy transfer causes the target atoms to be ejected from the surface into the gas phase.
- The sputtered atoms are ejected in a nearly random direction, with some traveling towards the substrate.
-
Deposition onto the Substrate:
- The ejected atoms travel through the vacuum and condense onto the substrate, forming a thin film.
- The substrate can be a silicon wafer, solar cell, optical component, or any other material requiring a thin film coating.
- The deposition process is highly controlled, allowing for precise thickness and uniformity of the film.
-
Advantages of Sputter Deposition:
- High-Quality Films: Sputter deposition produces films with excellent adhesion, uniformity, and density.
- Versatility: It can deposit a wide range of materials, including metals, alloys, and ceramics.
- Low Temperature: The process can be performed at relatively low temperatures, making it suitable for temperature-sensitive substrates.
- Scalability: It is compatible with large-scale industrial processes, such as semiconductor manufacturing.
-
Applications of Sputter Deposition:
- Semiconductors: Used to deposit thin films for integrated circuits and microelectronics.
- Optics: Coating of lenses, mirrors, and other optical components to enhance performance.
- Solar Cells: Deposition of thin films for photovoltaic applications.
- Decorative Coatings: Used in the production of decorative and functional coatings on various materials.
-
Resputtering and Secondary Effects:
- Resputtering occurs when deposited material is re-emitted from the substrate due to further ion bombardment.
- This can affect the final film properties, such as density and stress, but can also be controlled to optimize film quality.
-
Comparison with Other Deposition Techniques:
- Compared to thermal evaporation, sputter deposition provides better adhesion and higher energy for the deposited atoms.
- It is more versatile than chemical vapor deposition (CVD) for certain materials and applications, as it does not require chemical reactions.
In summary, sputter deposition is a versatile and widely used technique for depositing thin films with high precision and quality. Its fundamental principles involve the creation of a plasma, sputtering of target material, and deposition onto a substrate, making it a cornerstone of modern thin-film technology.
Summary Table:
Aspect | Details |
---|---|
Technique | Physical Vapor Deposition (PVD) |
Process | Bombardment of target material with high-energy ions (argon plasma) |
Key Components | Plasma, target material, substrate, vacuum chamber |
Advantages | High-quality films, versatility, low temperature, scalability |
Applications | Semiconductors, optics, solar cells, decorative coatings |
Comparison | Better adhesion than thermal evaporation; more versatile than CVD |
Interested in sputter deposition for your project? Contact us today to learn more!