The grinding process using a ball mill involves the use of a rotating cylinder filled with grinding media (such as steel balls or rods) to reduce the size of materials through impact, extrusion, and friction. The material is placed inside the mill, and as the cylinder rotates, the grinding media are tossed around, colliding with the material and breaking it down into finer particles. The process can be performed dry, in suspension, or in an inert gas environment, depending on the material and desired outcome. Achieving the critical speed of rotation is essential for effective grinding, as it ensures the grinding media cascade along the inner walls of the cylinder, maximizing impact and grinding efficiency.
Key Points Explained:
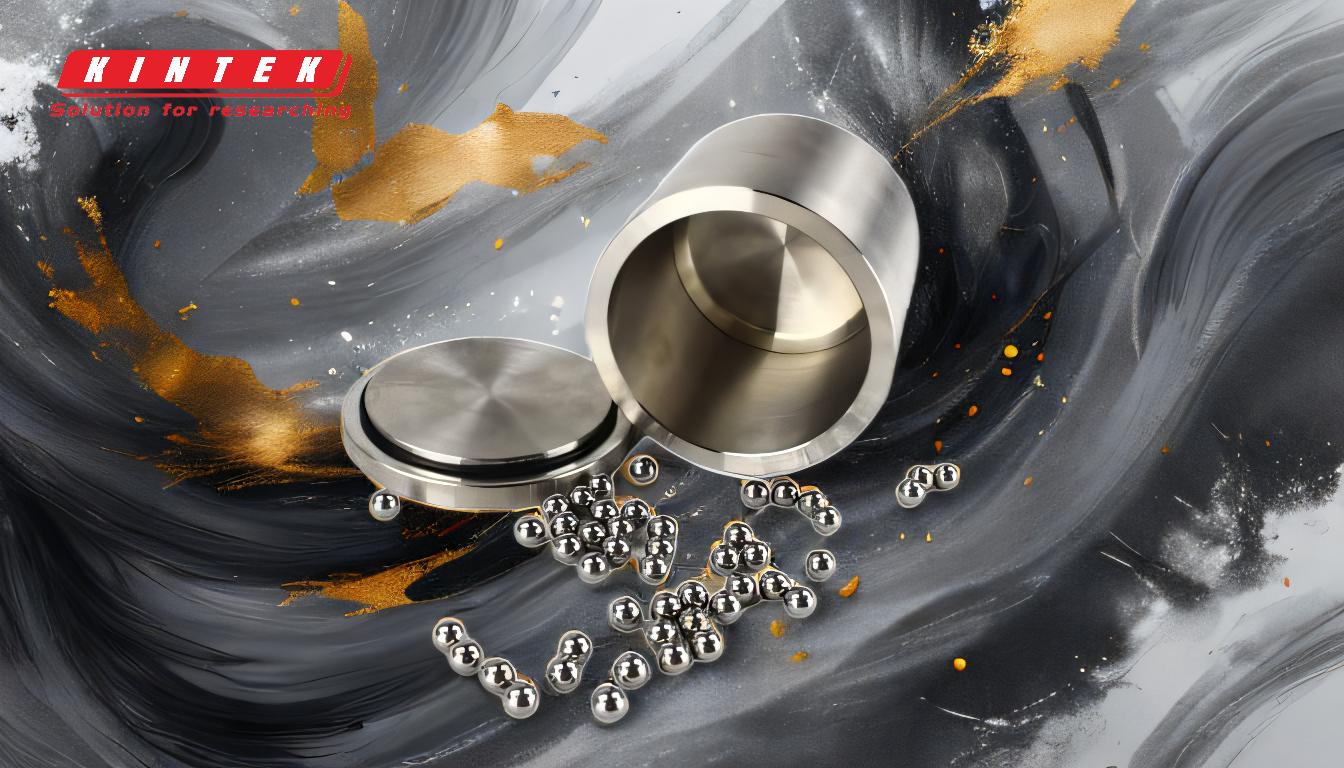
-
Mechanism of Grinding:
- The grinding process in a ball mill relies on the impact, extrusion, and friction generated by the grinding media (balls or rods) as they move within the rotating cylinder.
- When the cylinder rotates, the grinding media are lifted to a certain height and then fall or cascade, striking the material and breaking it into smaller particles.
- This repetitive action ensures thorough and uniform grinding of the material.
-
Critical Speed:
- Critical speed is the rotational speed at which the grinding media begin to centrifuge along the inner walls of the cylinder.
- Achieving critical speed is crucial for effective grinding, as it ensures the grinding media cascade and impact the material with sufficient force.
- If the speed is too low, the grinding media will not achieve the necessary impact force, resulting in inefficient grinding. If too high, the media may stick to the walls, reducing grinding effectiveness.
-
Types of Grinding Media:
- Steel balls are the most common grinding media, available in various sizes to suit different grinding requirements.
- Ceramic balls or rods may also be used, especially for materials that require contamination-free grinding.
- The choice of grinding media depends on the material being ground and the desired particle size.
-
Operating Modes:
- Dry Grinding: The material is ground without any liquid medium. This method is suitable for materials that do not require additional moisture or are sensitive to water.
- Wet Grinding: The material is ground in a liquid suspension, which helps reduce dust and can improve grinding efficiency for certain materials.
- Inert Gas Grinding: For materials that are sensitive to oxygen or moisture, grinding can be performed in an inert gas environment to prevent oxidation or contamination.
-
Planetary Ball Mills:
- Planetary ball mills are a specialized type of ball mill where grinding bowls rotate around their own axis while simultaneously orbiting around a central axis.
- This dual rotation generates high-energy impacts, making planetary ball mills ideal for fine and ultrafine grinding.
- They are commonly used in laboratories and industries requiring precise and controlled grinding.
-
Applications:
- Ball mills are widely used in industries such as mining, ceramics, pharmaceuticals, and materials science for grinding ores, chemicals, and other materials.
- They are also used in research and development to prepare samples for analysis or further processing.
-
Factors Affecting Grinding Efficiency:
- Rotation Speed: The speed of the cylinder must be optimized to achieve critical speed and ensure effective grinding.
- Grinding Media Size and Density: Larger or denser grinding media can provide greater impact force but may not be suitable for fine grinding.
- Material Properties: The hardness, brittleness, and moisture content of the material being ground influence the grinding process and the choice of grinding media.
By understanding these key points, users can optimize the grinding process in ball mills to achieve the desired particle size and quality for their specific applications.
Summary Table:
Key Aspect | Details |
---|---|
Mechanism of Grinding | Impact, extrusion, and friction from grinding media break down materials. |
Critical Speed | Rotational speed ensuring grinding media cascade for maximum impact. |
Grinding Media | Steel or ceramic balls/rods, chosen based on material and particle size. |
Operating Modes | Dry, wet, or inert gas grinding, depending on material requirements. |
Planetary Ball Mills | High-energy grinding for fine and ultrafine particle sizes. |
Applications | Mining, ceramics, pharmaceuticals, and materials science. |
Efficiency Factors | Rotation speed, media size/density, and material properties. |
Need help optimizing your ball mill grinding process? Contact our experts today for tailored solutions!