The speed of a ball mill is a critical factor influencing its grinding performance and overall efficiency. At low speeds, the grinding balls tend to slide or roll over each other, resulting in minimal size reduction. Conversely, at high speeds, centrifugal force causes the balls to be thrown against the cylinder wall, preventing effective grinding. Optimal performance is achieved at normal speeds, where the balls are carried to the top of the mill and then cascade down, maximizing size reduction. Additionally, other factors such as drum diameter, the ratio of drum diameter to length, and the properties of the material being ground also play significant roles in determining the productivity of a ball mill.
Key Points Explained:
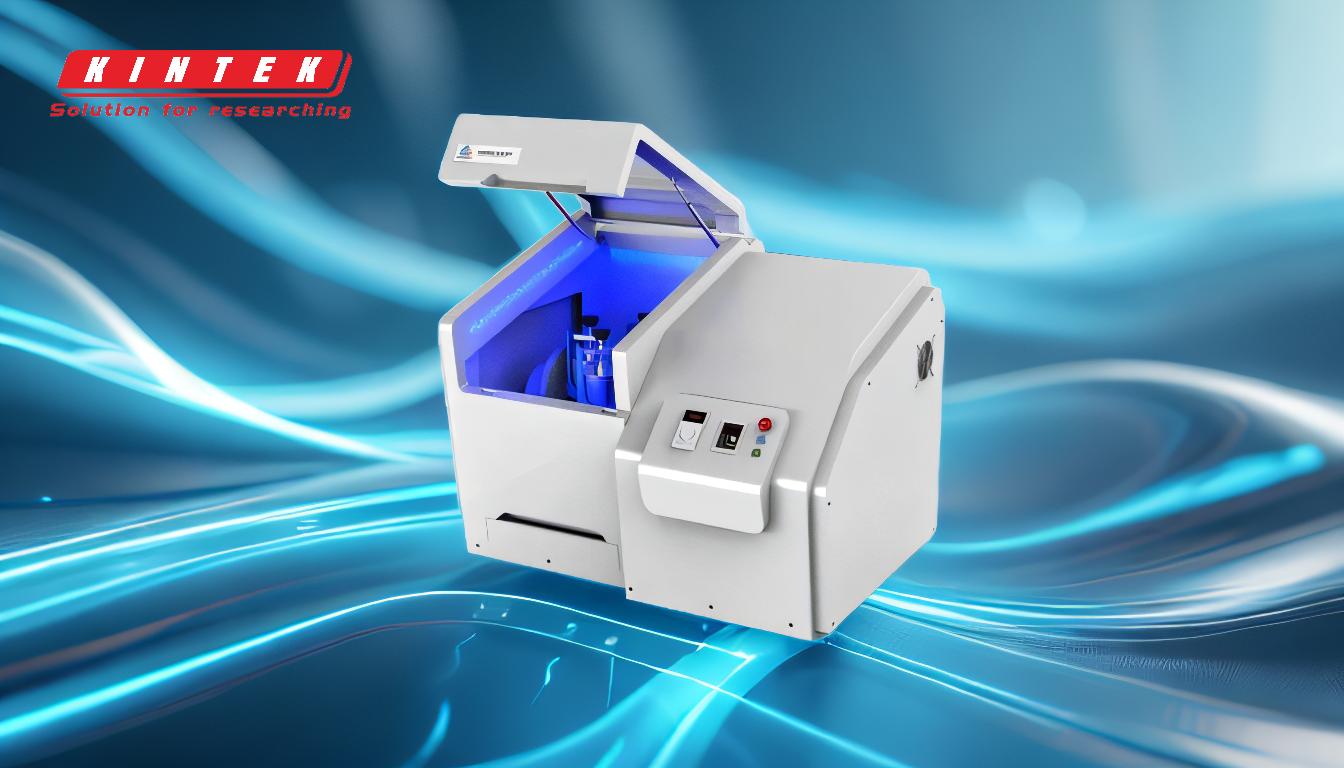
-
Impact of Speed on Grinding Efficiency:
- Low Speed: At low rotational speeds, the grinding balls tend to slide or roll over each other. This results in minimal impact and shear forces, leading to inefficient grinding and minimal size reduction.
- High Speed: When the mill operates at high speeds, the centrifugal force becomes dominant. The balls are thrown against the cylinder wall and do not cascade down, which prevents effective grinding as there is no significant impact or abrasion.
- Normal Speed: At optimal speeds, the balls are lifted to a certain height before cascading down. This cascade effect creates a combination of impact and abrasion forces, leading to maximum size reduction and efficient grinding.
-
Optimal Speed for Maximum Efficiency:
- The optimal speed for a ball mill is typically referred to as the "critical speed," where the balls are carried to the top of the mill and then cascade down. This critical speed is usually around 65-75% of the mill's critical speed, depending on the mill's design and the material being ground.
- Operating at this speed ensures that the grinding media (balls) are in constant motion, creating the necessary impact and shear forces to break down the material effectively.
-
Other Factors Influencing Ball Mill Performance:
- Drum Diameter and Length Ratio: The ratio of the drum diameter to its length (L:D ratio) is crucial. An optimal L:D ratio of 1.56–1.64 is generally recommended for efficient grinding.
- Grinding Medium: The size and type of grinding balls used in the mill can significantly affect grinding efficiency. Larger balls are more effective for coarse grinding, while smaller balls are better for fine grinding.
- Material Properties: The physical and chemical properties of the material being ground, such as hardness, moisture content, and particle size distribution, also impact grinding performance.
- Filling Ratio: The percentage of the mill volume filled with grinding medium (balls) affects the grinding efficiency. An optimal filling ratio ensures that there is enough contact between the balls and the material being ground without overloading the mill.
- Armor Surface Shape: The shape and condition of the mill's interior surface (armor) can influence the movement of the balls and the efficiency of the grinding process.
- Timely Removal of Ground Product: Efficient removal of the ground product from the mill is essential to prevent over-grinding and to maintain optimal grinding conditions.
-
Practical Implications for Equipment Purchasers:
- Speed Control: When selecting a ball mill, it is crucial to ensure that the mill has adjustable speed control to operate at the optimal speed for different materials and grinding requirements.
- Mill Design: Consider the drum diameter and length ratio, as well as the design of the armor surface, to ensure efficient grinding.
- Grinding Medium: Choose the appropriate size and type of grinding balls based on the material to be ground and the desired fineness of the product.
- Filling Ratio: Ensure that the mill can be operated at an optimal filling ratio to maximize grinding efficiency.
- Material Handling: Consider the ease of material loading and product removal to maintain continuous and efficient operation.
In summary, the speed of a ball mill is a vital parameter that directly affects its grinding performance. Operating at the optimal speed ensures efficient size reduction, while other factors such as mill design, grinding medium, and material properties also play significant roles in determining the overall productivity of the mill. Equipment purchasers should carefully consider these factors to select a ball mill that meets their specific grinding needs.
Summary Table:
Factor | Impact on Grinding Efficiency |
---|---|
Low Speed | Minimal impact and shear forces, leading to inefficient grinding and minimal size reduction. |
High Speed | Centrifugal force throws balls against the wall, preventing effective grinding. |
Normal Speed | Balls cascade down, creating impact and abrasion forces for maximum size reduction. |
Critical Speed | Typically 65-75% of the mill's critical speed, ensuring optimal grinding performance. |
Drum Diameter/Length | Optimal L:D ratio (1.56–1.64) enhances grinding efficiency. |
Grinding Medium | Larger balls for coarse grinding; smaller balls for fine grinding. |
Material Properties | Hardness, moisture, and particle size distribution affect grinding performance. |
Filling Ratio | Optimal filling ensures sufficient contact between balls and material without overloading. |
Armor Surface Shape | Influences ball movement and grinding efficiency. |
Product Removal | Timely removal prevents over-grinding and maintains optimal conditions. |
Ready to optimize your grinding process? Contact us today to find the perfect ball mill for your needs!