The injection molding process is a highly efficient manufacturing technique used to produce plastic parts by injecting molten plastic material into a press mold, where it cools and solidifies into the desired shape. This process is widely used in industries for mass production due to its ability to produce high volumes of identical parts with precision and consistency. Below is a detailed explanation of the key aspects of the injection molding process.
Key Points Explained:
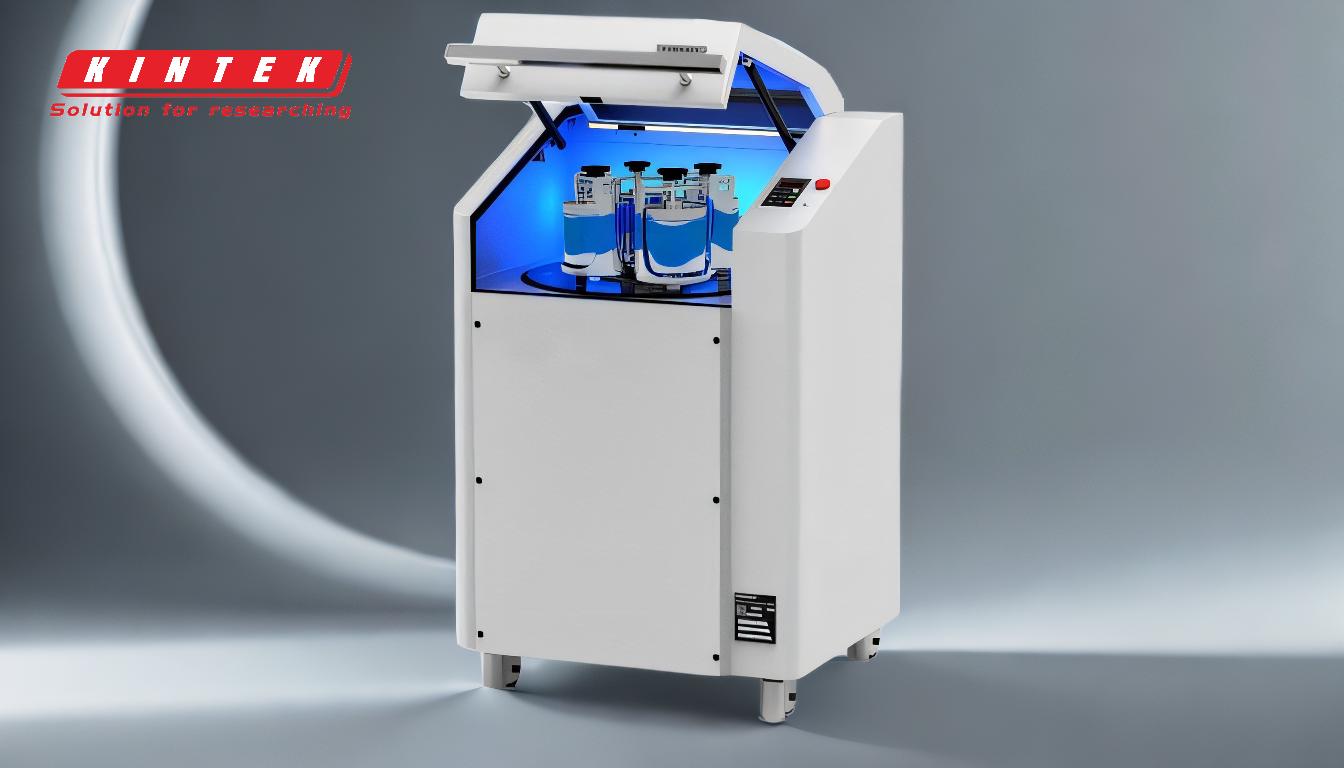
-
Overview of Injection Molding:
- Injection molding is a manufacturing process used to produce plastic parts by injecting molten plastic material into a mold.
- The process involves several stages: melting the plastic, injecting it into the mold, cooling, and ejecting the finished part.
-
Materials Used:
- The most common materials used in injection molding are thermoplastics, such as polyethylene, polypropylene, and polystyrene.
- These materials are chosen for their ability to be melted and solidified repeatedly without significant degradation.
-
The Injection Molding Machine:
- The machine consists of two main parts: the injection unit and the clamping unit.
- The injection unit melts the plastic and injects it into the mold.
- The clamping unit holds the mold closed during the injection and cooling phases.
-
The Mold:
- The mold is a custom-made tool designed to shape the molten plastic into the desired form.
- It is typically made from steel or aluminum and can be quite complex, depending on the part being produced.
-
The Injection Molding Process:
- Melting: The plastic material is fed into the injection molding machine, where it is heated until it becomes molten.
- Injection: The molten plastic is then injected into the mold cavity under high pressure.
- Cooling: Once the plastic fills the mold, it is allowed to cool and solidify.
- Ejection: After cooling, the mold opens, and the finished part is ejected.
-
Advantages of Injection Molding:
- High Efficiency: Injection molding can produce large quantities of parts quickly.
- Precision: The process allows for high precision and repeatability, making it ideal for complex parts.
- Material Variety: A wide range of materials can be used, allowing for flexibility in product design.
-
Challenges and Considerations:
- Initial Costs: The cost of designing and manufacturing the mold can be high, making it less economical for small production runs.
- Design Constraints: The design of the part must take into account the limitations of the injection molding process, such as wall thickness and draft angles.
-
Applications:
- Injection molding is used in a variety of industries, including automotive, consumer goods, medical devices, and electronics.
- Common products include plastic housings, containers, caps, and intricate components.
In summary, the injection molding process is a versatile and efficient method for producing plastic parts. It involves melting plastic, injecting it into a mold, cooling it, and ejecting the finished product. While the initial setup costs can be high, the process is ideal for high-volume production due to its precision, repeatability, and ability to use a wide range of materials.
Summary Table:
Aspect | Details |
---|---|
Overview | Produces plastic parts by injecting molten material into a mold. |
Materials | Thermoplastics like polyethylene, polypropylene, and polystyrene. |
Machine Components | Injection unit (melts and injects plastic) and clamping unit (holds mold). |
Process Steps | Melting, injection, cooling, and ejection. |
Advantages | High efficiency, precision, and material variety. |
Challenges | High initial costs and design constraints. |
Applications | Automotive, consumer goods, medical devices, and electronics. |
Ready to optimize your plastic part production? Contact us today to learn more about injection molding solutions!