The maximum feed size for a hammer mill depends on several factors, including the design of the mill, the type of material being processed, and the intended output size. Generally, hammer mills can handle feed sizes ranging from a few millimeters up to several centimeters, but the exact maximum feed size varies based on the specific model and application. Hammer mills are designed to reduce materials by impacting them with hammers rotating at high speeds, and the feed size must be compatible with the mill's internal dimensions and hammer configuration. Larger feed sizes may require pre-processing or specialized hammer mill designs.
Key Points Explained:
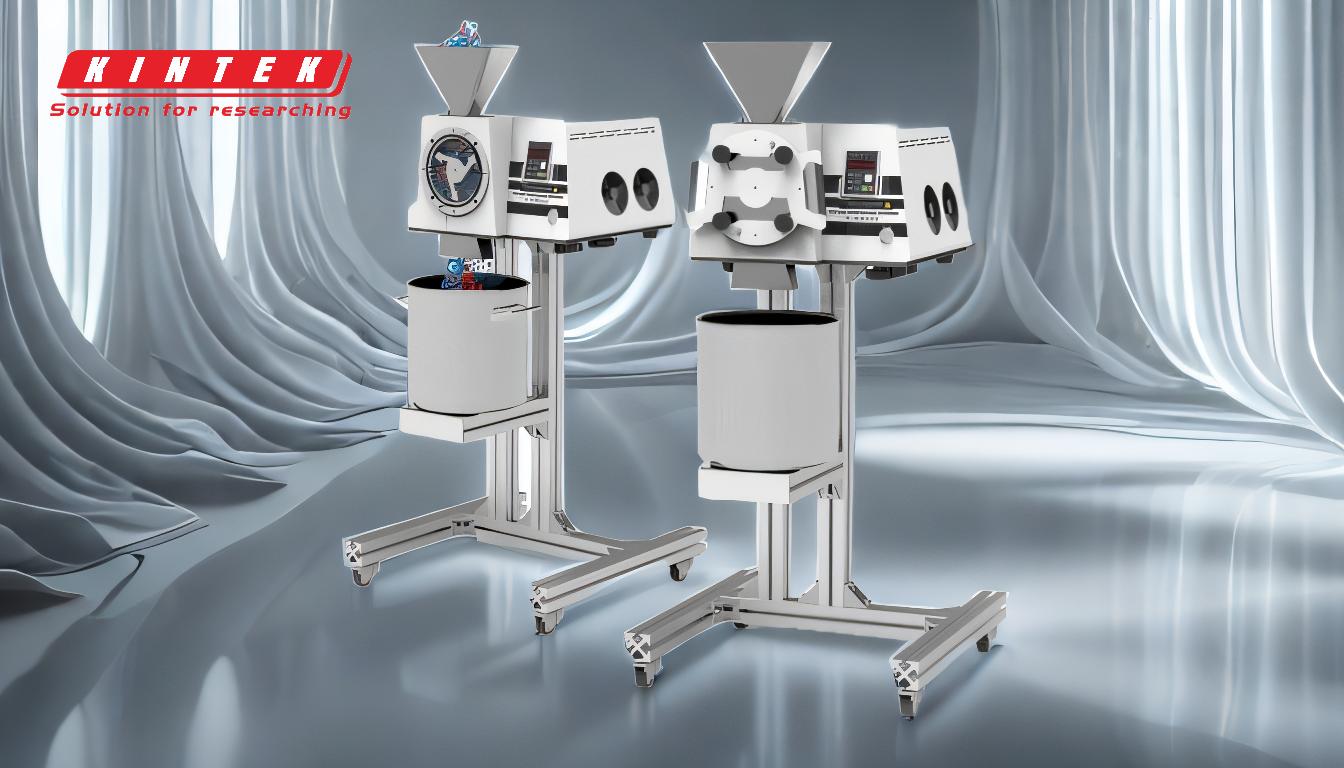
-
Design of the Hammer Mill:
- The maximum feed size is largely determined by the internal dimensions of the hammer mill, including the size of the grinding chamber and the spacing between the hammers and the screen.
- Larger hammer mills with bigger chambers and more robust hammers can typically accommodate larger feed sizes.
-
Type of Material Being Processed:
- The physical properties of the material, such as hardness, density, and moisture content, influence the maximum feed size.
- Brittle or soft materials can often be fed in larger sizes compared to tough or fibrous materials, which may require smaller feed sizes to ensure efficient grinding.
-
Intended Output Size:
- The desired final particle size affects the maximum feed size. For finer output, smaller feed sizes are generally required.
- Coarser output allows for larger feed sizes, as the mill does not need to reduce the material as much.
-
Hammer Mill Configuration:
- The number, size, and arrangement of hammers play a significant role in determining the maximum feed size.
- Mills with more hammers or heavier hammers can handle larger feed sizes more effectively.
-
Pre-Processing Requirements:
- For materials that exceed the maximum feed size of a standard hammer mill, pre-processing steps such as cutting, shredding, or crushing may be necessary.
- Some hammer mills are designed with pre-breakers or specialized inlets to handle larger feed sizes without additional pre-processing.
-
Application-Specific Considerations:
- Different industries and applications may have specific requirements for feed size. For example, agricultural applications may require larger feed sizes for processing grains or biomass, while pharmaceutical applications may need smaller feed sizes for precise grinding.
-
Manufacturer Specifications:
- Always refer to the manufacturer's guidelines for the specific hammer mill model to determine the maximum feed size.
- Manufacturers often provide detailed specifications and recommendations based on extensive testing and experience.
By considering these factors, you can determine the appropriate maximum feed size for a hammer mill in your specific application, ensuring efficient and effective operation.
Summary Table:
Factor | Impact on Maximum Feed Size |
---|---|
Design of the Hammer Mill | Larger chambers and robust hammers allow for bigger feed sizes. |
Type of Material | Brittle/soft materials can handle larger feed sizes; tough/fibrous materials require smaller. |
Intended Output Size | Finer output requires smaller feed sizes; coarser output allows larger feed sizes. |
Hammer Mill Configuration | More or heavier hammers enable handling of larger feed sizes. |
Pre-Processing | Pre-processing may be needed for oversized materials or specialized mill designs. |
Application-Specific Needs | Agricultural uses may require larger feed sizes; pharmaceutical uses need smaller feed sizes. |
Manufacturer Specifications | Always refer to manufacturer guidelines for specific feed size recommendations. |
Need help determining the right hammer mill feed size for your application? Contact our experts today!