A ball mill is a cylindrical device used for grinding or mixing materials such as ores, chemicals, ceramic raw materials, and paints. It operates by rotating a hollow cylindrical shell partially filled with grinding media (typically steel, ceramic, or rubber balls) around its horizontal or slightly inclined axis. The mechanical design of a ball mill includes a metallic frame, a rotating cylinder, grinding media, and liners made of abrasion-resistant materials like manganese steel or rubber. The mill relies on the principles of impact and attrition to break down materials into finer particles. The large balls crush coarse feed materials, while smaller balls reduce void spaces to produce fine products.
Key Points Explained:
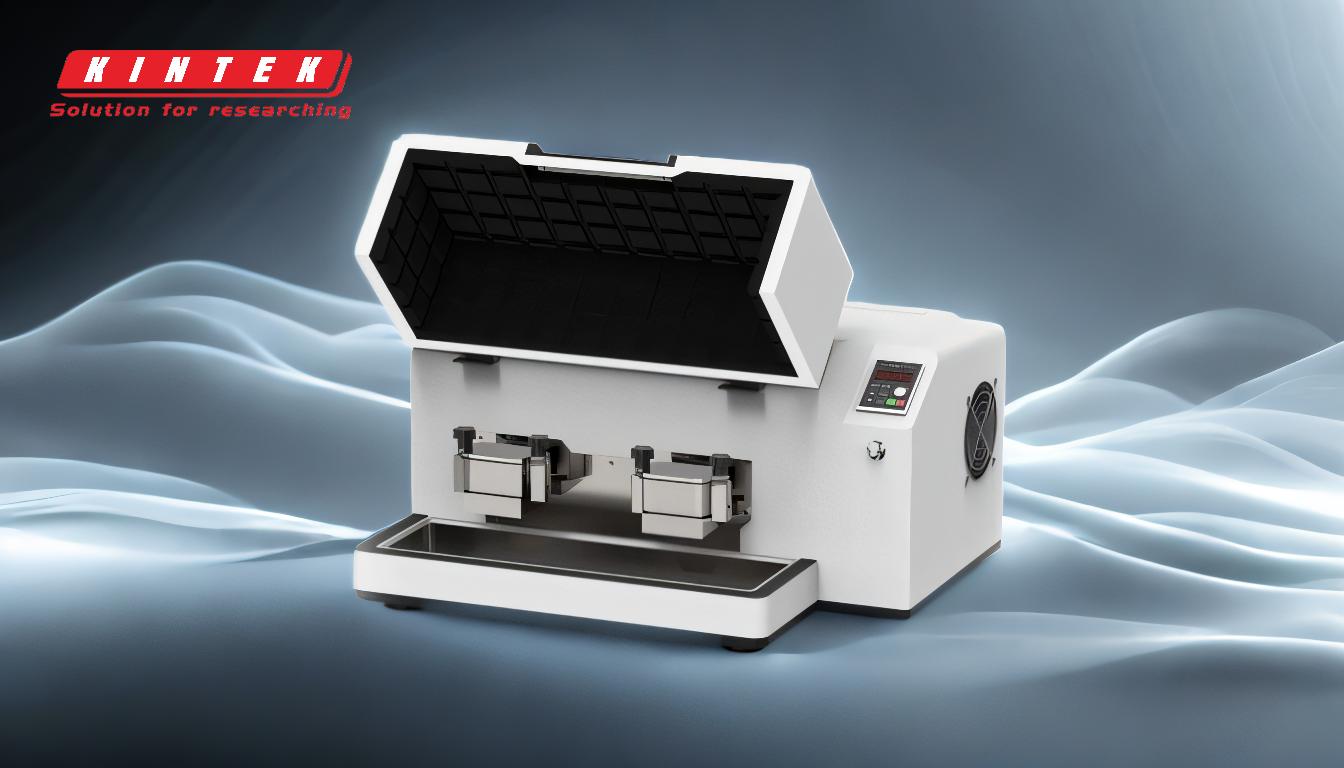
-
Cylindrical Shell Structure:
- The ball mill consists of a hollow cylindrical shell that rotates about its axis. The shell is typically made of durable materials to withstand the grinding process.
- The cylinder can be oriented horizontally or at a slight angle to the horizontal, depending on the design and application.
-
Grinding Media:
- The cylinder is partially filled with grinding media, which are usually spherical balls made of materials like steel, stainless steel, ceramic, or rubber.
- The size and material of the balls depend on the application and the type of material being ground. Larger balls are used for coarse grinding, while smaller balls are used for fine grinding.
-
Abrasion-Resistant Liners:
- The inner surface of the cylindrical shell is lined with abrasion-resistant materials such as manganese steel or rubber. These liners protect the shell from wear and tear caused by the grinding media and the materials being processed.
- The choice of liner material depends on the hardness and abrasiveness of the materials being ground.
-
Rotational Mechanism:
- The cylindrical shell is mounted on a metallic frame that allows it to rotate along its longitudinal axis. The rotation is typically driven by a motor connected to the frame.
- The speed of rotation is a critical factor in the grinding process. Optimal rotation speed ensures that the grinding media cascade and impact the materials effectively.
-
Principles of Operation:
- Impact: The grinding process relies on the impact of the grinding media (balls) on the materials. The force exerted by the balls breaks down the materials into smaller particles.
- Attrition: In addition to impact, the grinding process also involves attrition, where the materials are reduced in size due to the friction and collision between the balls and the materials.
-
Size Reduction Mechanism:
- The large balls in the mill are primarily responsible for breaking down coarse feed materials. These balls exert significant force, crushing the materials into smaller fragments.
- The smaller balls help in reducing void spaces within the mill, ensuring that the materials are ground into fine particles. The combination of different ball sizes ensures efficient grinding and uniform particle size distribution.
-
Applications:
- Ball mills are widely used in various industries, including mining, ceramics, and chemical processing. They are essential for grinding ores, chemicals, and other raw materials into fine powders.
- The versatility of ball mills allows them to be used for both wet and dry grinding processes.
-
Design Considerations:
- The design of a ball mill must consider factors such as the size and material of the grinding media, the speed of rotation, and the type of liner used.
- The mill's capacity, efficiency, and durability are influenced by these design parameters. Proper maintenance and operation are also crucial for optimal performance.
In summary, the mechanical design of a ball mill involves a rotating cylindrical shell filled with grinding media and lined with abrasion-resistant materials. The mill operates on the principles of impact and attrition, with the grinding media breaking down materials into fine particles. The design considerations, including the choice of materials and rotational speed, play a critical role in the mill's performance and efficiency.
Summary Table:
Key Component | Description |
---|---|
Cylindrical Shell | Hollow cylinder made of durable materials, rotates horizontally or at an angle. |
Grinding Media | Spherical balls (steel, ceramic, rubber) for coarse and fine grinding. |
Abrasion-Resistant Liners | Liners (manganese steel, rubber) protect the shell from wear. |
Rotational Mechanism | Motor-driven rotation for optimal grinding speed. |
Principles of Operation | Impact and attrition break materials into fine particles. |
Applications | Used in mining, ceramics, and chemical processing for wet and dry grinding. |
Design Considerations | Size/material of grinding media, rotation speed, and liner type are critical. |
Discover how a ball mill can optimize your material grinding process—contact our experts today!