The minimum detectable leak rate refers to the smallest leak rate that can be reliably detected by a leak detection system under specific conditions. It is a critical parameter in industries where leak detection is essential for safety, environmental compliance, or operational efficiency. The minimum detectable leak rate depends on factors such as the sensitivity of the detection equipment, the testing method used, and environmental conditions like temperature and pressure. Understanding this concept helps in selecting the right equipment and ensuring accurate leak detection in various applications.
Key Points Explained:
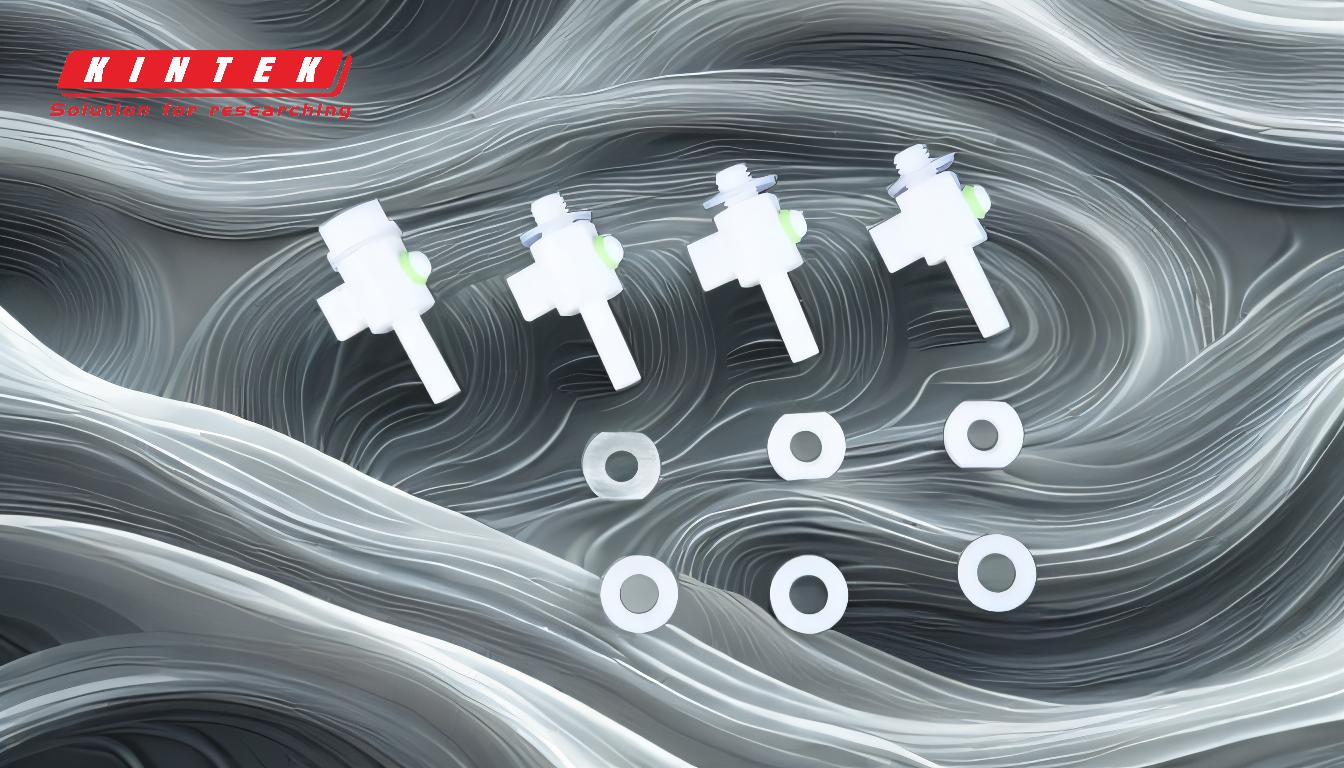
-
Definition of Minimum Detectable Leak Rate:
- The minimum detectable leak rate is the smallest rate of leakage that a detection system can reliably identify. It is typically expressed in units like standard cubic centimeters per second (scc/s) or millibar-liters per second (mbar·L/s).
- This parameter is crucial for ensuring that even the smallest leaks are identified, which is especially important in industries such as aerospace, automotive, and semiconductor manufacturing.
-
Factors Influencing Minimum Detectable Leak Rate:
- Sensitivity of Detection Equipment: The sensitivity of the leak detection equipment, such as mass spectrometers or helium leak detectors, directly impacts the minimum detectable leak rate. More sensitive equipment can detect smaller leaks.
- Testing Method: Different testing methods, such as pressure decay testing, bubble testing, or tracer gas testing, have varying levels of sensitivity. Tracer gas methods, for example, are often more sensitive than pressure decay methods.
- Environmental Conditions: Factors like temperature, pressure, and background noise can affect the ability to detect small leaks. For instance, high background noise can mask small leaks, making them harder to detect.
-
Importance in Different Industries:
- In industries like aerospace and automotive, detecting even the smallest leaks is critical for safety and performance. For example, a small leak in a fuel system can lead to significant safety hazards.
- In the semiconductor industry, detecting minute leaks is essential for maintaining the integrity of vacuum systems and ensuring the quality of the manufacturing process.
-
Measurement and Calibration:
- Accurate measurement of the minimum detectable leak rate requires proper calibration of the detection equipment. Calibration ensures that the equipment is sensitive enough to detect leaks at the desired rate.
- Regular calibration and maintenance of the equipment are necessary to maintain its sensitivity and accuracy over time.
-
Challenges in Detecting Small Leaks:
- One of the main challenges in detecting small leaks is distinguishing between actual leaks and background noise. Advanced signal processing techniques are often used to enhance the detection of small leaks.
- Another challenge is ensuring that the testing environment is stable and free from external disturbances that could affect the detection process.
-
Applications and Real-World Examples:
- In the pharmaceutical industry, detecting small leaks in packaging is crucial for ensuring the sterility and shelf life of products.
- In the oil and gas industry, detecting leaks in pipelines is essential for preventing environmental contamination and ensuring operational safety.
Understanding the minimum detectable leak rate and the factors that influence it is essential for selecting the right leak detection equipment and ensuring accurate and reliable detection in various applications.
Summary Table:
Key Aspect | Details |
---|---|
Definition | Smallest leak rate a system can reliably detect, measured in scc/s or mbar·L/s. |
Key Factors | Sensitivity of equipment, testing method, and environmental conditions. |
Industries | Aerospace, automotive, semiconductor, pharmaceutical, oil & gas. |
Challenges | Background noise, environmental stability, and equipment calibration. |
Applications | Fuel systems, vacuum systems, packaging, pipelines. |
Ensure accurate leak detection for your operations—contact our experts today for tailored solutions!