The preferred size range for the sieving method, specifically dry sieving, is between 40 µm and 125 mm. This range is ideal for most applications, but the effectiveness of sieving can be influenced by sample properties such as agglomeration, density, and electrostatic charging. When selecting a sieving machine or sieve shaker, it is crucial to consider factors like the type of material being tested, sieve diameter, and filling capacity. Industry standards also play a significant role in determining the construction of a test sieve stack, ensuring it is tailored to the specific needs of the material being analyzed.
Key Points Explained:
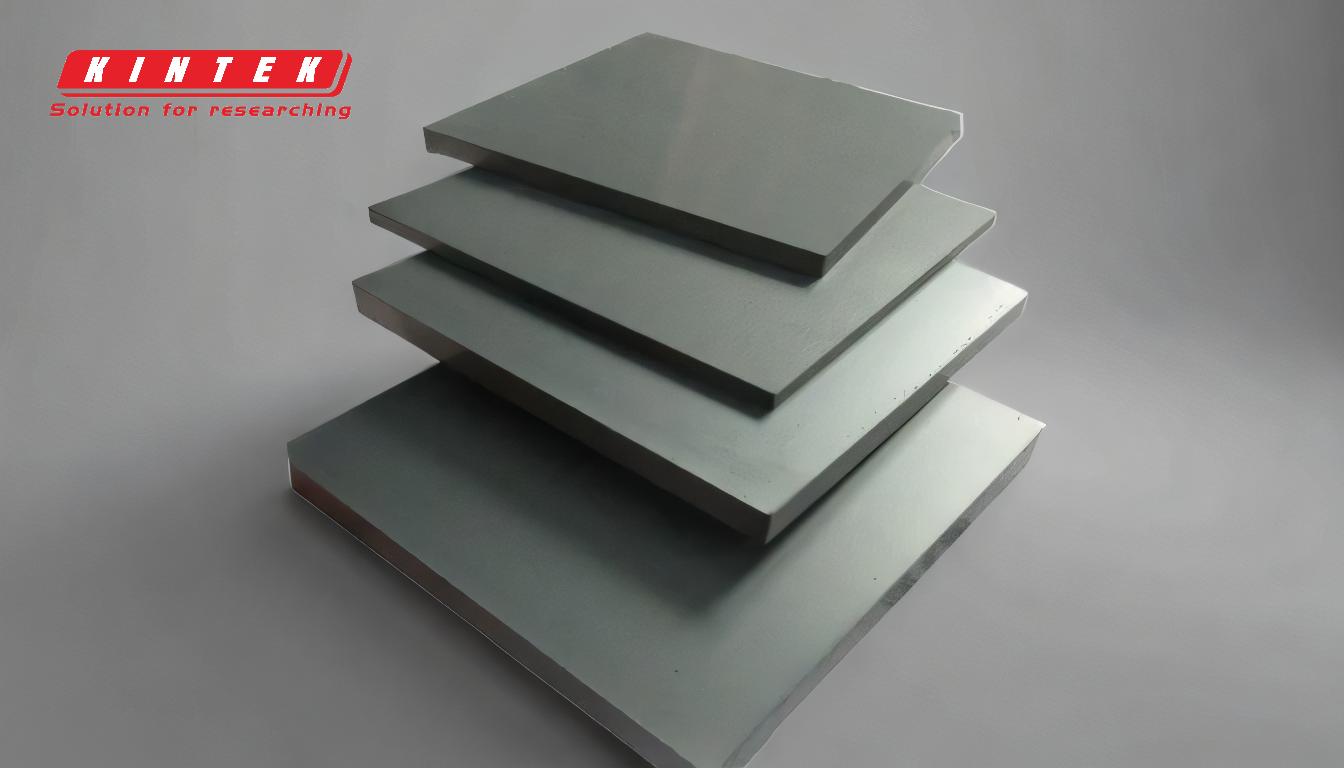
-
Preferred Size Range for Dry Sieving:
- Dry sieving is most effective for particles ranging from 40 µm to 125 mm. This range is suitable for a wide variety of materials, from fine powders to coarse aggregates.
- The size range is chosen based on the ability of sieves to accurately separate particles within these dimensions without significant loss or error.
-
Influence of Sample Properties:
- Agglomeration: Particles that tend to clump together can be challenging to sieve accurately. Agglomeration can lead to inaccurate size distribution results.
- Density: Materials with high density may require more vigorous sieving action to ensure proper separation.
- Electrostatic Charging: Particles that generate static electricity can stick to the sieve or each other, affecting the sieving process. Anti-static measures may be necessary.
-
Selection of Sieving Equipment:
- Type of Material: Different materials require different types of sieve shakers. For example, coarse aggregates need robust shakers, while fine materials like flour require gentler, more precise equipment.
- Sieve Diameter: The diameter of the sieves must match the volume and type of material being tested. Larger diameters are suitable for bulk materials, while smaller diameters are better for fine powders.
- Filling Capacity: The sieving machine must be compatible with the required filling capacity for the specific application. Overloading or underloading the sieve can lead to inaccurate results.
-
Industry Standards:
- The construction of a test sieve stack is governed by industry standards, which specify the required mesh sizes, number of sieves, and other parameters. These standards ensure that the sieve stack is optimized for the specific material being analyzed.
- Adhering to these standards is crucial for obtaining consistent and reliable results across different laboratories and applications.
-
Effectiveness of Sieve Shakers:
- The effectiveness of a sieve shaker is influenced by the characteristics of the material being tested. Factors such as the minimum size to be separated, resistance to agglomeration, and static electric factors must be considered.
- Different materials and particle sizes require different shaker features and techniques. For example, materials prone to agglomeration may benefit from sieve shakers that include tapping or ultrasonic features to break up clumps.
-
Optimizing Sieving Performance:
- To ensure optimal performance, it is essential to match the sieving machine's capabilities with the specific requirements of the material being tested. This includes considering the machine's filling capacity, the type of sieve shaker, and the construction of the sieve stack.
- Regular maintenance and calibration of sieving equipment are also important to maintain accuracy and reliability over time.
By considering these key points, one can select the appropriate sieving method and equipment to achieve accurate and reliable particle size analysis.
Summary Table:
Key Factor | Details |
---|---|
Preferred Size Range | 40 µm to 125 mm, ideal for most materials. |
Sample Properties | Agglomeration, density, and electrostatic charging affect sieving results. |
Equipment Selection | Consider material type, sieve diameter, and filling capacity. |
Industry Standards | Ensure sieve stack construction meets material-specific requirements. |
Optimizing Performance | Match machine capabilities, maintain equipment, and calibrate regularly. |
Need help selecting the right sieving equipment? Contact our experts today for tailored solutions!