The principle of size reduction in a ball mill revolves around the mechanical forces applied to materials through the impact, extrusion, and friction generated by grinding balls within the mill. When the ball mill operates, the grinding balls collide with the material, breaking it into smaller particles. Additionally, the rolling and sliding motion of the balls against the material and the mill's inner walls contribute to further size reduction. This process continues until the desired particle size is achieved. The efficiency of size reduction depends on factors such as the speed of the mill, the size and quantity of grinding balls, and the properties of the material being processed.
Key Points Explained:
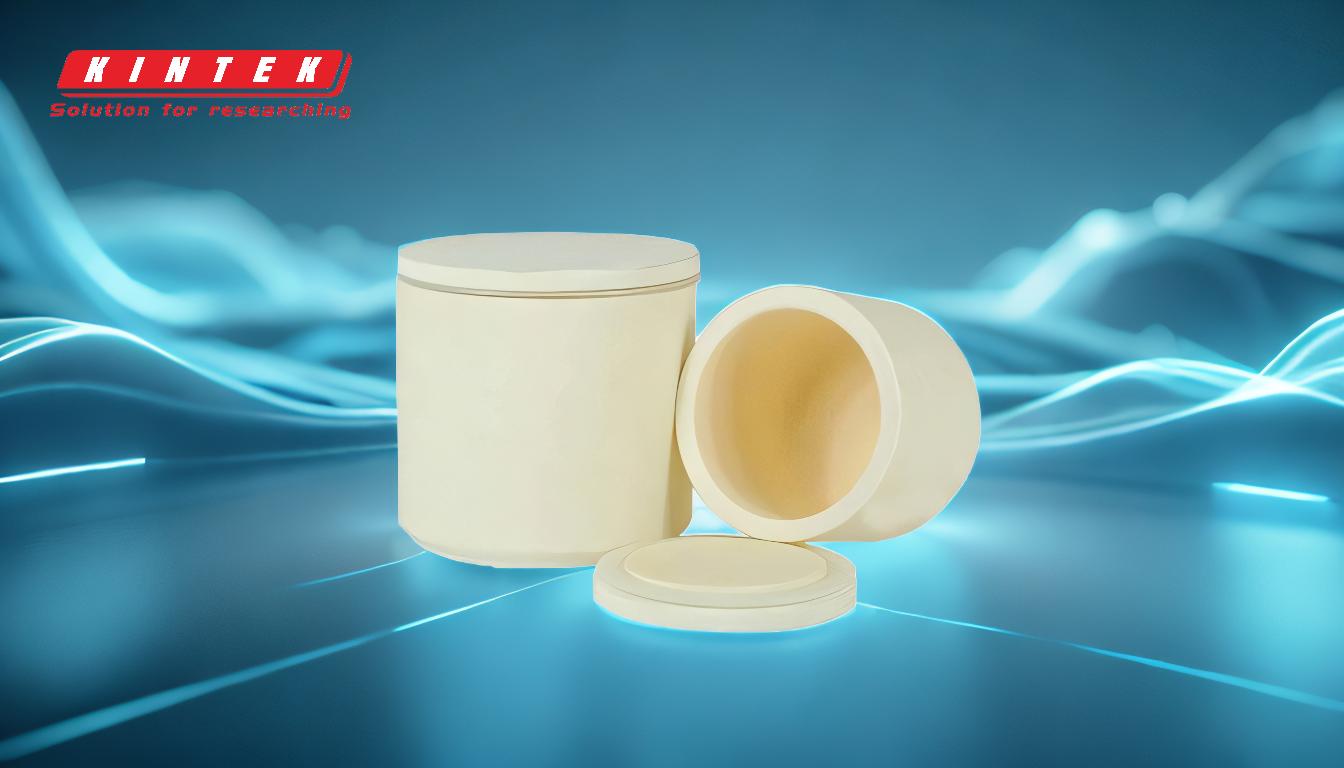
-
Mechanism of Size Reduction:
- Impact: Grinding balls collide with the material, delivering kinetic energy that fractures the particles into smaller sizes.
- Extrusion: The material is compressed between the balls and the mill's inner walls, leading to further size reduction.
- Friction: The rolling and sliding motion of the balls against the material generates shear forces, which help in breaking down the particles.
-
Role of Grinding Balls:
- The grinding balls are critical components that apply mechanical forces to the material. Their size, density, and quantity influence the efficiency of the size reduction process.
- Larger balls are more effective for coarse grinding, while smaller balls are better suited for fine grinding.
-
Operational Parameters:
- Mill Speed: The rotational speed of the mill affects the motion of the grinding balls. Optimal speed ensures that the balls cascade and impact the material effectively.
- Filling Ratio: The proportion of the mill volume occupied by grinding balls and material impacts the grinding efficiency. An appropriate filling ratio ensures sufficient contact between the balls and the material.
-
Material Properties:
- The hardness, brittleness, and size of the material being processed influence the size reduction process. Harder materials may require longer grinding times or higher energy input.
-
Process Control:
- The desired particle size is achieved by controlling the duration of grinding and the operational parameters of the mill. Once the target size is reached, the process is stopped to prevent over-grinding.
-
Applications:
- Ball mills are widely used in industries such as mining, ceramics, and pharmaceuticals for grinding and blending materials to achieve fine particle sizes.
By understanding these key points, a purchaser can make informed decisions about selecting the appropriate ball mill and grinding parameters for their specific application.
Summary Table:
Key Aspect | Details |
---|---|
Mechanism of Size Reduction | Impact, extrusion, and friction break materials into smaller particles. |
Role of Grinding Balls | Size, density, and quantity affect grinding efficiency. |
Operational Parameters | Mill speed and filling ratio optimize grinding performance. |
Material Properties | Hardness and brittleness influence grinding time and energy requirements. |
Process Control | Control grinding duration and parameters to achieve desired particle size. |
Applications | Used in mining, ceramics, and pharmaceuticals for fine particle production. |
Discover how a ball mill can optimize your material processing—contact our experts today!