The ball mill experiment is a fundamental procedure used in material science and engineering to grind and blend materials for use in mineral dressing processes, paints, pyrotechnics, ceramics, and selective laser sintering. The experiment involves loading the ball mill with the material to be ground and the grinding media (balls), setting the desired operational parameters such as rotation speed and duration, and then running the mill. After the grinding process, the material is collected and analyzed to determine the effectiveness of the grinding process. This procedure is crucial for optimizing the grinding process and achieving the desired material properties.
Key Points Explained:
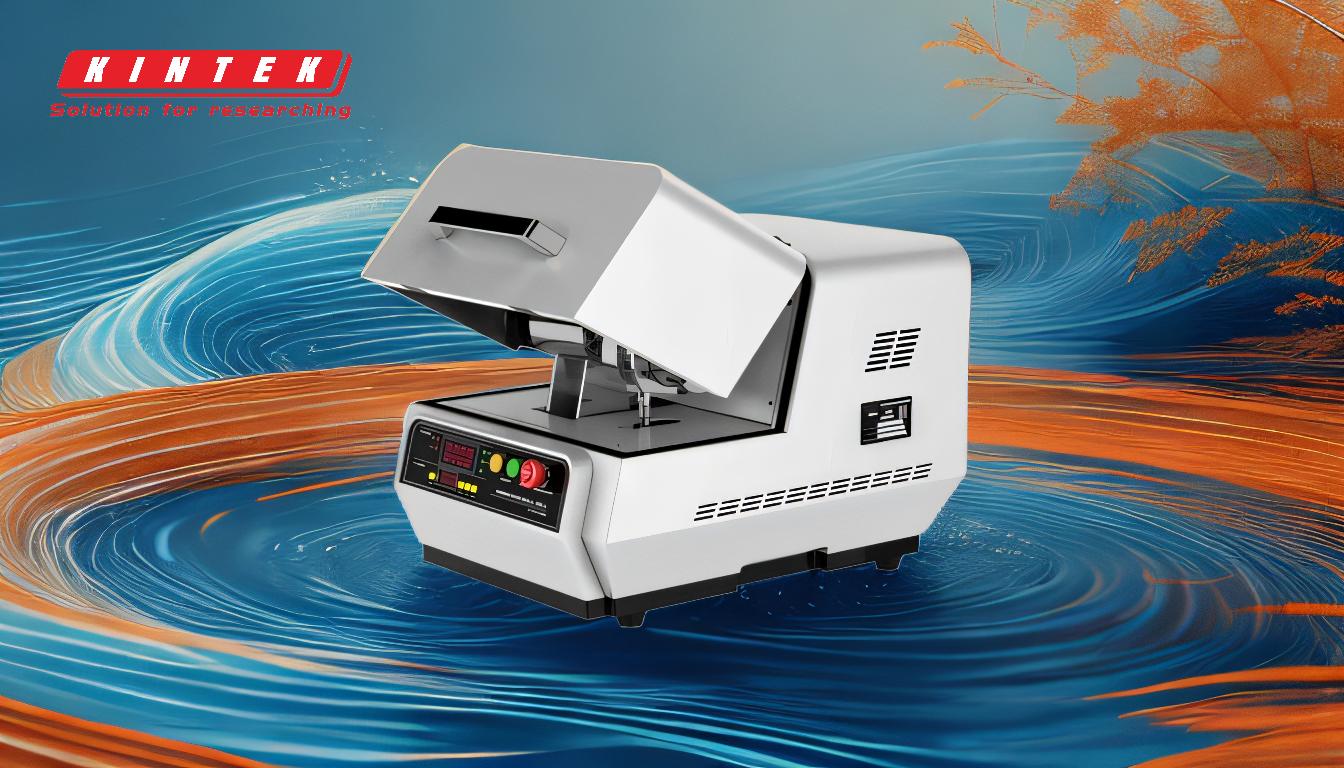
-
Preparation of the Ball Mill:
- Material Loading: The first step in the ball mill experiment is to load the material to be ground into the mill. This material can range from ores and minerals to ceramics and chemicals.
- Grinding Media Selection: The type and size of the grinding media (balls) are selected based on the material properties and the desired fineness of the ground product. Common materials for grinding balls include steel, ceramic, and flint.
-
Setting Operational Parameters:
- Rotation Speed: The rotation speed of the ball mill is a critical parameter that affects the grinding efficiency. It is typically set as a percentage of the critical speed, which is the speed at which the grinding media begin to centrifuge.
- Duration: The duration of the grinding process is determined based on the material properties and the desired particle size distribution. Longer grinding times generally result in finer particles but can also lead to increased wear on the mill and grinding media.
-
Running the Ball Mill:
- Starting the Mill: Once the material and grinding media are loaded and the operational parameters are set, the ball mill is started. The mill rotates, causing the grinding media to cascade and impact the material, breaking it down into smaller particles.
- Monitoring the Process: During the grinding process, it is important to monitor the mill to ensure that it is operating within the desired parameters. This may involve checking the temperature, noise levels, and vibration of the mill.
-
Collection and Analysis of Ground Material:
- Material Collection: After the grinding process is complete, the ground material is collected from the mill. This may involve discharging the material through a grate or using a scoop to remove it manually.
- Particle Size Analysis: The collected material is then analyzed to determine the particle size distribution. This can be done using techniques such as sieving, laser diffraction, or sedimentation.
- Evaluation of Grinding Efficiency: The effectiveness of the grinding process is evaluated based on the particle size distribution and other material properties. This information is used to optimize the grinding process for future experiments.
-
Maintenance and Cleaning:
- Mill Cleaning: After the experiment, the ball mill should be thoroughly cleaned to remove any residual material. This is important to prevent contamination in future experiments.
- Inspection and Maintenance: Regular inspection and maintenance of the ball mill are essential to ensure its proper functioning. This may involve checking the condition of the grinding media, inspecting the mill lining for wear, and lubricating moving parts.
-
Safety Considerations:
- Personal Protective Equipment (PPE): Operators should wear appropriate PPE, such as gloves, safety glasses, and ear protection, to protect themselves from potential hazards during the experiment.
- Ventilation: Proper ventilation is important to prevent the buildup of dust and fumes, which can be harmful to health.
- Emergency Procedures: Operators should be familiar with emergency procedures, such as how to stop the mill quickly in case of an emergency.
By following this structured procedure, the ball mill experiment can be conducted safely and effectively, providing valuable insights into the grinding process and helping to optimize material properties for various applications.
Summary Table:
Step | Key Details |
---|---|
Preparation | Load material and select grinding media (steel, ceramic, or flint balls). |
Operational Parameters | Set rotation speed (% of critical speed) and grinding duration. |
Running the Mill | Monitor temperature, noise, and vibration during operation. |
Material Analysis | Collect ground material and analyze particle size distribution. |
Maintenance | Clean the mill and inspect grinding media and lining for wear. |
Safety | Use PPE, ensure proper ventilation, and follow emergency procedures. |
Ready to optimize your grinding process? Contact our experts today for tailored solutions!