The pyrolysis reactor process involves the thermochemical decomposition of materials, such as biomass, plastics, or tires, in the absence of oxygen. This process breaks down the material into smaller molecules, producing gases (syngas), liquids (bio-oil), and solids (bio-char). The reactor operates as a closed system, relying on an external heat supply and thermodynamic principles. Depending on the reactor type, such as fixed-bed or fluidized-bed, the process may involve distinct zones for drying, pyrolysis, and gasification, with specific temperature and oxygen conditions. The process is energy-intensive but effective for waste reduction and generating valuable byproducts.
Key Points Explained:
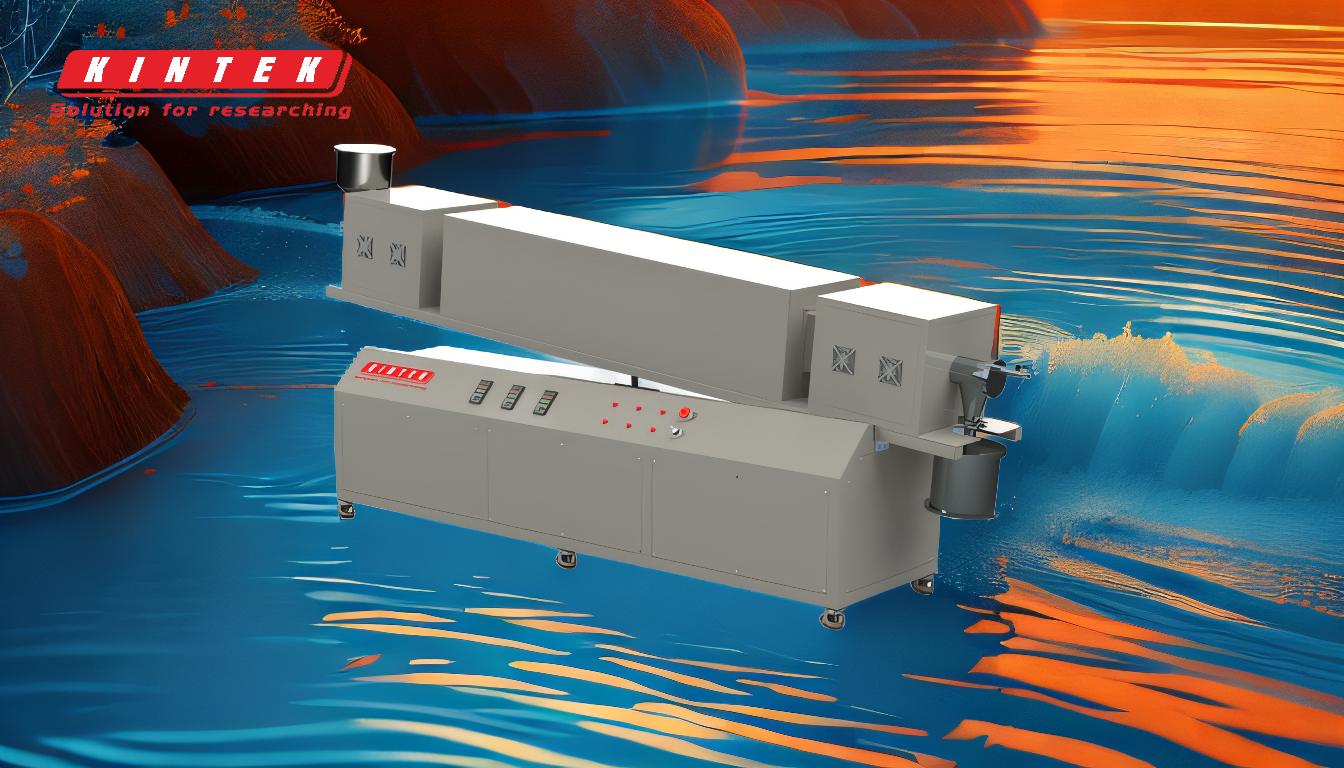
-
Thermochemical Decomposition:
- Pyrolysis involves heating materials above their decomposition temperature in the absence of oxygen.
- This breaks chemical bonds, resulting in smaller molecules or residues with larger molecular mass.
- The process can produce gases (syngas), liquids (bio-oil), and solids (bio-char), depending on the material and process conditions.
-
Reactor Types:
-
Fixed-Bed Reactor:
- A simple-design vessel where the substrate is introduced at the bottom.
- Heat is applied from the walls, transferring energy to the substrate at a consistent rate.
- Thermal decomposition occurs as heat diffuses inward, breaking down the material.
-
Fluidized-Bed Reactor:
- Separates waste flows into two zones with different oxygen concentrations.
- The "bed section" involves a sand mass where drying, pyrolysis, and gasification occur under low oxygen conditions.
- The "free section" includes a secondary addition of air for further burning, with a gas retention period of at least 2 seconds at 825°C or higher.
-
Fixed-Bed Reactor:
-
Process Steps:
-
Pre-Treatment:
- The material, such as plastic waste, is pre-treated to remove impurities and ground to the required size.
-
Loading and Heating:
- The material is loaded into the pyrolysis chamber, often with a catalyst.
- It is heated to a temperature between 200-900°C, causing it to melt and vaporize.
-
Condensation and Refinement:
- Vapors are condensed into liquid oil, which is further refined for use as fuel.
-
Pre-Treatment:
-
Operating Conditions:
- The process requires specific temperature and oxygen conditions to avoid side reactions like combustion or hydrolysis.
- It can be conducted in a vacuum or inert atmosphere to improve the recovery of byproducts.
- The reactor operates as a closed system, relying on an external heat supply and thermodynamic principles.
-
Applications and Benefits:
- Pyrolysis is used to convert biomass, plastics, and tires into useful products, reducing waste and generating valuable outputs.
- It is energy-intensive but effective for waste reduction and resource recovery.
-
Challenges:
- The process is energy-intensive and requires precise control of temperature and oxygen levels.
- It may involve side reactions if not conducted under optimal conditions, affecting the quality and yield of byproducts.
By understanding these key points, a purchaser can evaluate the suitability of pyrolysis reactors for specific applications, considering factors like material type, desired outputs, and operational requirements.
Summary Table:
Aspect | Details |
---|---|
Process | Thermochemical decomposition of materials in the absence of oxygen. |
Outputs | Syngas, bio-oil, and bio-char. |
Reactor Types | Fixed-bed and fluidized-bed reactors. |
Key Steps | Pre-treatment, loading and heating, condensation and refinement. |
Operating Conditions | Specific temperature (200-900°C) and oxygen conditions, often in a vacuum or inert atmosphere. |
Applications | Converts biomass, plastics, and tires into valuable byproducts. |
Challenges | Energy-intensive, requires precise control of temperature and oxygen levels. |
Discover how pyrolysis reactors can transform waste into valuable resources—contact us today for expert guidance!