The sputter coating process is a sophisticated technique used to deposit thin films of material onto a substrate. It involves creating a plasma by electrically charging a sputtering cathode, which ejects material from a target surface. This ejected material is then directed onto a substrate, forming a strong atomic-level bond. The process is widely used in applications such as Scanning Electron Microscopy (SEM) to enhance surface conductivity and reduce charging effects. Below, the key steps and principles of the sputter coating process are explained in detail.
Key Points Explained:
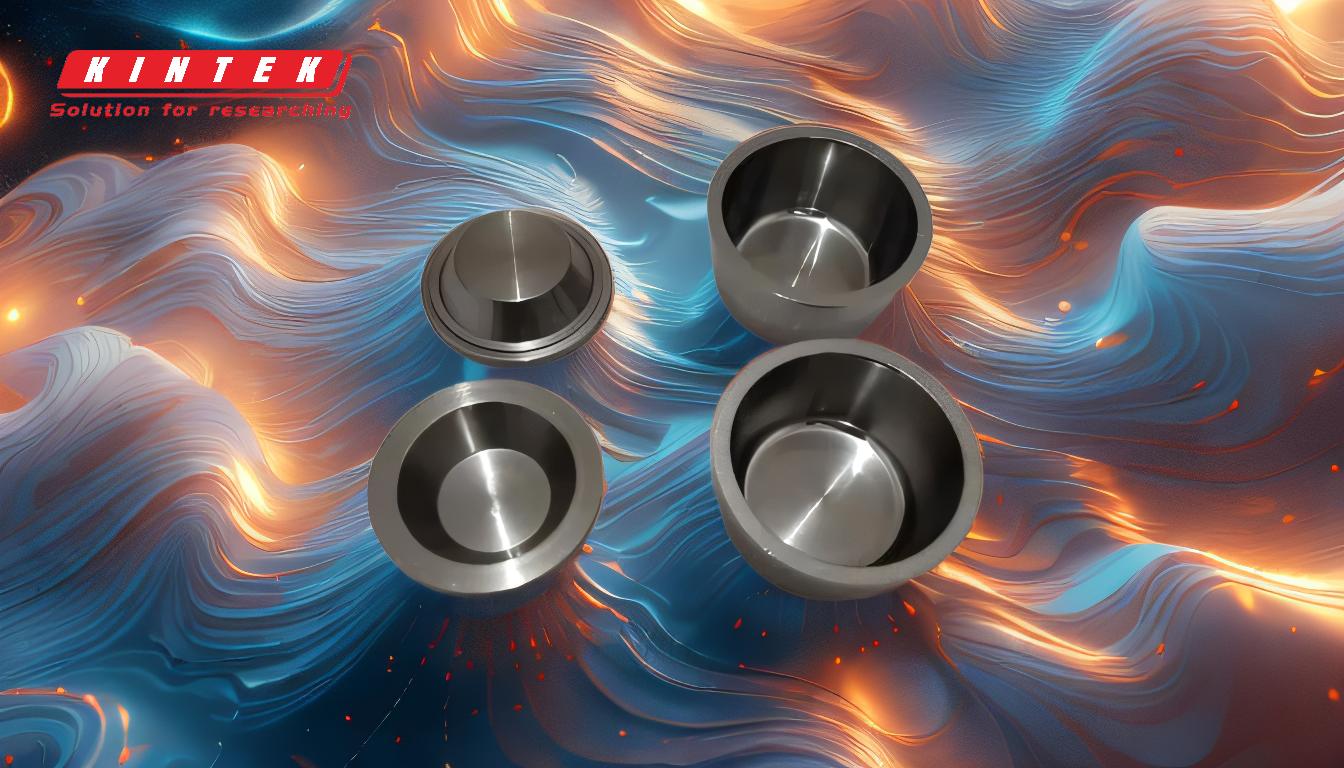
-
Formation of Plasma
- The process begins by electrically charging a sputtering cathode, which generates a plasma. This plasma consists of gas atoms (typically argon), free electrons, and positively charged ions.
- The plasma is concentrated and stabilized using magnetic fields, ensuring efficient and uniform sputtering of the target material.
-
Sputtering of Target Material
- The target material, often gold or another conductive material, is bonded or clamped to the cathode.
- High-energy ions from the plasma bombard the target surface, causing atoms to be ejected in a process called "sputtering."
- Magnets are used to ensure stable and uniform erosion of the target material, which is critical for consistent coating quality.
-
Transport of Sputtered Atoms
- The sputtered atoms are transported through a region of reduced pressure (vacuum) toward the substrate.
- This omni-directional deposition ensures that the sputtered atoms evenly coat the substrate's surface.
-
Deposition and Bonding
- The high-energy sputtered atoms impact the substrate, forming a strong atomic-level bond.
- This results in a thin, uniform film that adheres well to the substrate, enhancing its properties such as conductivity and durability.
-
Applications and Benefits
- Sputter coating is widely used in SEM to improve secondary electron emission and reduce charging effects.
- It also minimizes thermal damage to the substrate, making it suitable for delicate samples.
-
Key Components of a Sputter Coater
- Vacuum Chamber: Maintains a low-pressure environment to facilitate the sputtering process.
- Target Material: The material to be deposited, often gold, platinum, or other conductive metals.
- Cooling Systems: Manage the heat generated during the process to prevent damage to the equipment and substrate.
-
Nanotechnology Integration
- The process involves transforming solid materials into microscopic particles, which are then deposited as a thin film.
- This integration of nanotechnology ensures precise control over the coating's thickness and uniformity.
By understanding these key points, one can appreciate the precision and complexity of the sputter coating process. It is a vital technique in materials science and microscopy, offering significant advantages in surface modification and analysis.
Summary Table:
Step | Description |
---|---|
Formation of Plasma | Electrically charged cathode generates plasma (argon gas, ions, electrons). |
Sputtering of Target | High-energy ions bombard target material, ejecting atoms for deposition. |
Transport of Atoms | Sputtered atoms move through a vacuum, ensuring uniform coating on the substrate. |
Deposition and Bonding | Atoms form strong atomic bonds, creating a thin, durable film on the substrate. |
Applications | Enhances SEM imaging, reduces charging effects, and minimizes thermal damage. |
Key Components | Vacuum chamber, target material (e.g., gold), and cooling systems. |
Nanotechnology Integration | Transforms materials into microscopic particles for precise, uniform coatings. |
Discover how sputter coating can improve your applications—contact our experts today!