The sputtering coating process is a precise and controlled method used to deposit thin films of materials onto substrates. It involves creating a vacuum environment, introducing inert gases, applying high voltage to ionize the gas, and using the resulting ions to eject atoms from a target material. These ejected atoms then deposit onto a substrate, forming a thin, uniform coating. The process is widely used in industries such as semiconductors, optics, and decorative coatings due to its ability to produce high-quality, durable films.
Key Points Explained:
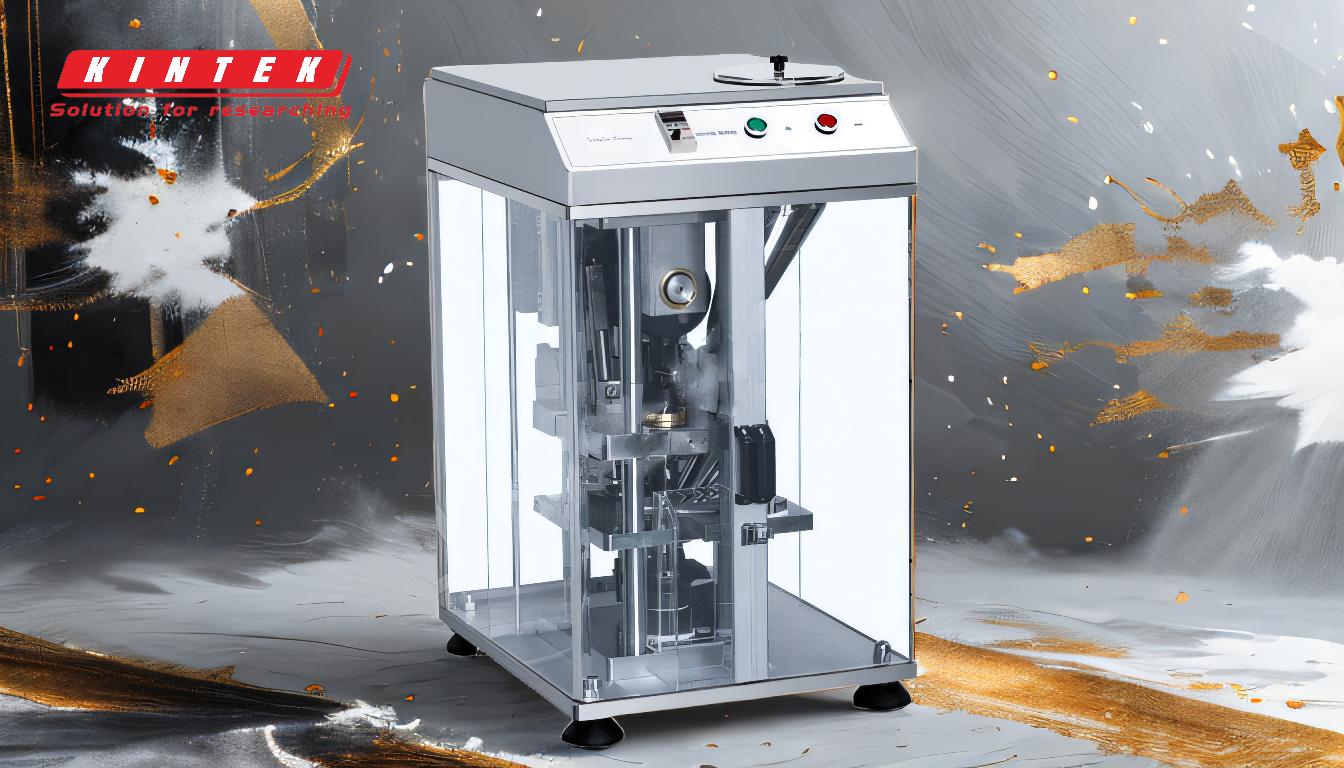
-
Vacuum Creation:
- The first step in the sputtering process is to create a vacuum within the reaction chamber. This involves dropping the internal pressure to around 1 Pa (or 10^-6 torr in some processes) to remove moisture and impurities. A clean, vacuum environment is crucial to prevent contamination and ensure the quality of the coating.
-
Introduction of Inert Gas:
- Once a vacuum is established, an inert gas such as argon or xenon is introduced into the chamber. This gas is chosen because it is chemically inert and does not react with the target material or the substrate. The gas creates a low-pressure atmosphere necessary for the ionization process.
-
Heating the Chamber:
- The chamber is then heated to temperatures ranging between 150°C to 750°C. Heating helps to improve the adhesion of the coating to the substrate and can also influence the microstructure of the deposited film.
-
Magnetic Field Creation:
- In some sputtering processes, particularly magnetron sputtering, tools are placed between the metallic target and an electromagnet to create a magnetic field. This magnetic field helps to trap electrons near the target surface, increasing the efficiency of the ionization process and enhancing the sputtering rate.
-
Ionization of Gas Atoms:
- A high voltage is applied to ionize the inert gas atoms. This voltage generates a glow discharge, which is a plasma of ionized gas. Free electrons collide with the gas atoms, knocking off electrons and creating positively charged ions.
-
Target Bombardment:
- The positively charged ions are accelerated towards the negatively charged target material due to the applied voltage. When these ions collide with the target, they knock out (sputter) atoms from the target material.
-
Deposition on Substrate:
- The sputtered atoms are ejected from the target and travel through the vacuum chamber. They eventually collide with and adhere to the substrate, forming a thin, uniform coating. The properties of the coating, such as its thickness, adhesion, and microstructure, can be controlled by adjusting parameters like the voltage, gas pressure, and temperature.
-
Condensation and Film Formation:
- The final step involves the condensation of the sputtered atoms on the substrate. As the atoms lose energy, they condense and form a solid film. This film can be as thin as a few nanometers, making sputtering an ideal process for applications requiring precise and thin coatings.
By carefully controlling each of these steps, the sputtering process can produce high-quality coatings with specific properties tailored to the needs of various applications. Whether it's for enhancing the durability of tools, improving the performance of electronic components, or creating decorative finishes, sputtering offers a versatile and effective solution.
Summary Table:
Step | Description |
---|---|
1. Vacuum Creation | Drop chamber pressure to ~1 Pa to remove impurities and moisture. |
2. Inert Gas Intro | Introduce inert gas (e.g., argon) to create a low-pressure atmosphere. |
3. Heating Chamber | Heat chamber to 150°C–750°C to improve coating adhesion and microstructure. |
4. Magnetic Field | Use electromagnets to trap electrons, enhancing ionization and sputtering rates. |
5. Gas Ionization | Apply high voltage to ionize gas atoms, creating a plasma of positively charged ions. |
6. Target Bombardment | Ions collide with the target, ejecting atoms (sputtering). |
7. Deposition | Sputtered atoms travel and adhere to the substrate, forming a thin, uniform film. |
8. Film Formation | Atoms condense on the substrate, creating a solid coating as thin as nanometers. |
Discover how sputtering coating can enhance your applications—contact our experts today for more information!