A calciner is a specialized thermal processing equipment used primarily in industrial and metallurgical applications to heat materials at high temperatures below their melting points. Its main purpose is to remove volatile impurities, such as water, carbon dioxide, or sulfur dioxide, from metal ores or other substances. This process, known as calcination, is critical in industries like cement production, where limestone is calcinated to produce clinker, a key ingredient in concrete. Additionally, calciners are used for drying, oxidation, and chemical transformations, making them versatile tools in material processing. They operate in high-temperature environments, often in rotary kilns, and are essential for achieving desired material properties and purity.
Key Points Explained:
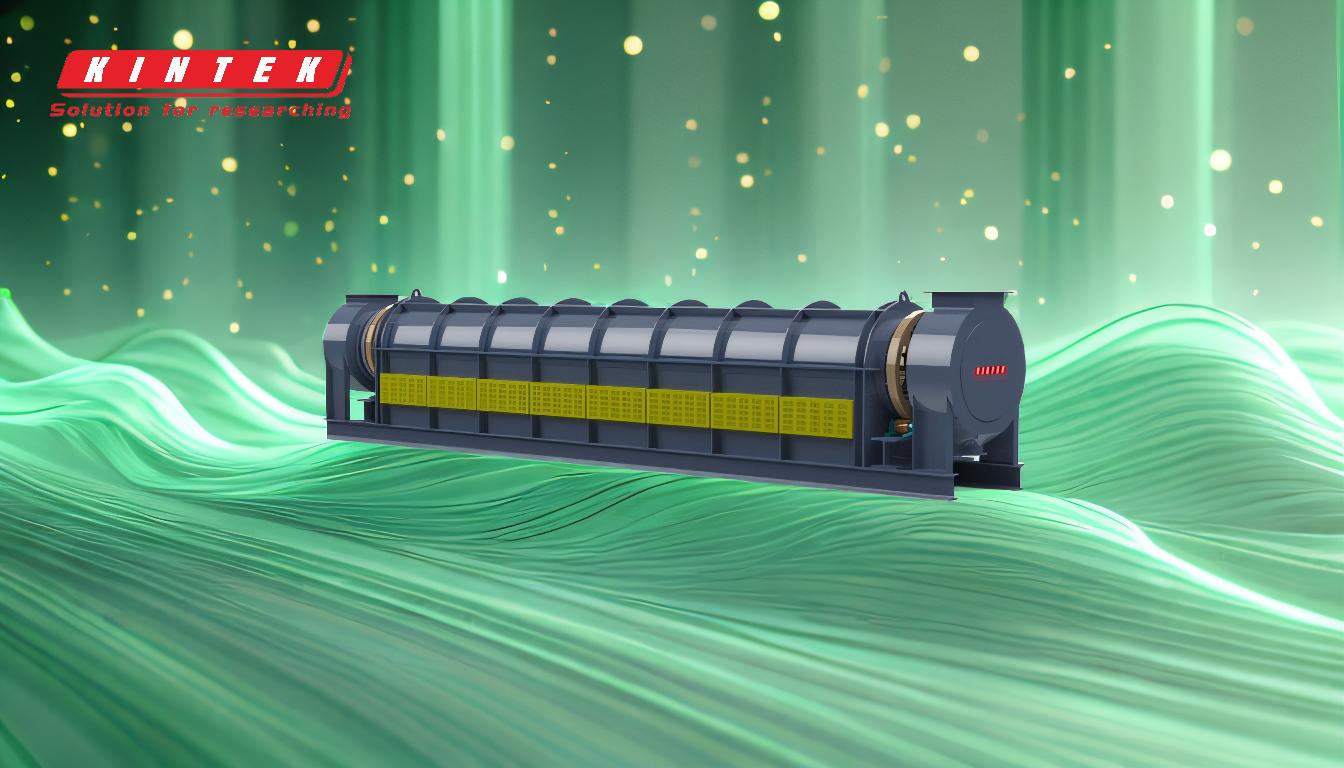
-
Definition and Purpose of Calcination:
- Calcination is a thermal process where materials are heated to high temperatures (below their melting points) in the presence of limited air or oxygen.
- The primary purpose is to remove volatile impurities, such as moisture, carbon dioxide, or sulfur dioxide, from metal ores or other substances.
- This process is crucial for purifying materials and preparing them for further industrial use.
-
Applications of Calciners:
- Removing Water: Calciners are used to drive off absorbed moisture from materials, ensuring dryness and stability.
- Eliminating Volatile Constituents: They remove volatile compounds like carbon dioxide or sulfur dioxide, which can interfere with material properties.
- Oxidation: Calciners can oxidize part or all of a substance, altering its chemical composition for specific applications.
- Cement Production: One of the most common uses is in the calcination of limestone to produce clinker, a key component in cement manufacturing.
-
Role in Industrial Processes:
- Calciners are integral to pyrometallurgical processes, where high temperatures are used to extract and purify metals from ores.
- They are also used in chemical transformations, organic combustion, and thermal desorption, making them versatile in various industries.
-
Functionality in Rotary Kilns:
- Rotary kilns, often used as calciners, are designed to provide ultra-high temperature environments for continuous or batch processes.
- They function as heat exchangers, dryers, calcinators, and incinerators, making them suitable for a wide range of thermal processing tasks.
- In cement production, rotary kilns facilitate the calcination of limestone, initiating the chemical reactions needed to form clinker.
-
Importance in Clinker Production:
- In cement manufacturing, the calciner is where preheated raw meal and fuel mix within a hot air stream to start the calcination reaction.
- This reaction is the first step in producing clinker, which is then ground to make cement.
-
Versatility and Adaptability:
- Calciners are adaptable to various materials and processes, including drying, sintering, reduction roasting, and incineration.
- Their ability to operate at high temperatures and handle different materials makes them indispensable in industries like metallurgy, chemical processing, and construction.
By understanding these key points, equipment and consumable purchasers can better evaluate the role of calciners in their specific industrial applications and make informed decisions about their use and maintenance.
Summary Table:
Key Aspect | Description |
---|---|
Definition | A thermal process to remove volatile impurities at high temperatures. |
Primary Purpose | Purify materials by eliminating water, CO₂, or SO₂. |
Applications | Drying, oxidation, chemical transformations, and cement production. |
Role in Industry | Essential in pyrometallurgy, cement manufacturing, and chemical processing. |
Functionality in Rotary Kilns | High-temperature environments for continuous or batch processes. |
Versatility | Adaptable for drying, sintering, reduction roasting, and incineration. |
Ready to optimize your material processing with a calciner? Contact our experts today to learn more!