A calciner is a specialized thermal processing equipment designed to facilitate high-temperature chemical reactions, primarily calcination, which involves heating materials to drive off volatile components, remove moisture, or induce chemical transformations. It plays a critical role in industries such as cement production, where it initiates the calcination reaction to convert raw materials like limestone into clinker. Beyond cement, calciners are used in metallurgy, chemical processing, and environmental applications to remove impurities, oxidize substances, or prepare materials for further processing. By providing precise temperature control and efficient heat transfer, calciners enable the transformation of raw materials into usable products, making them indispensable in industrial manufacturing.
Key Points Explained:
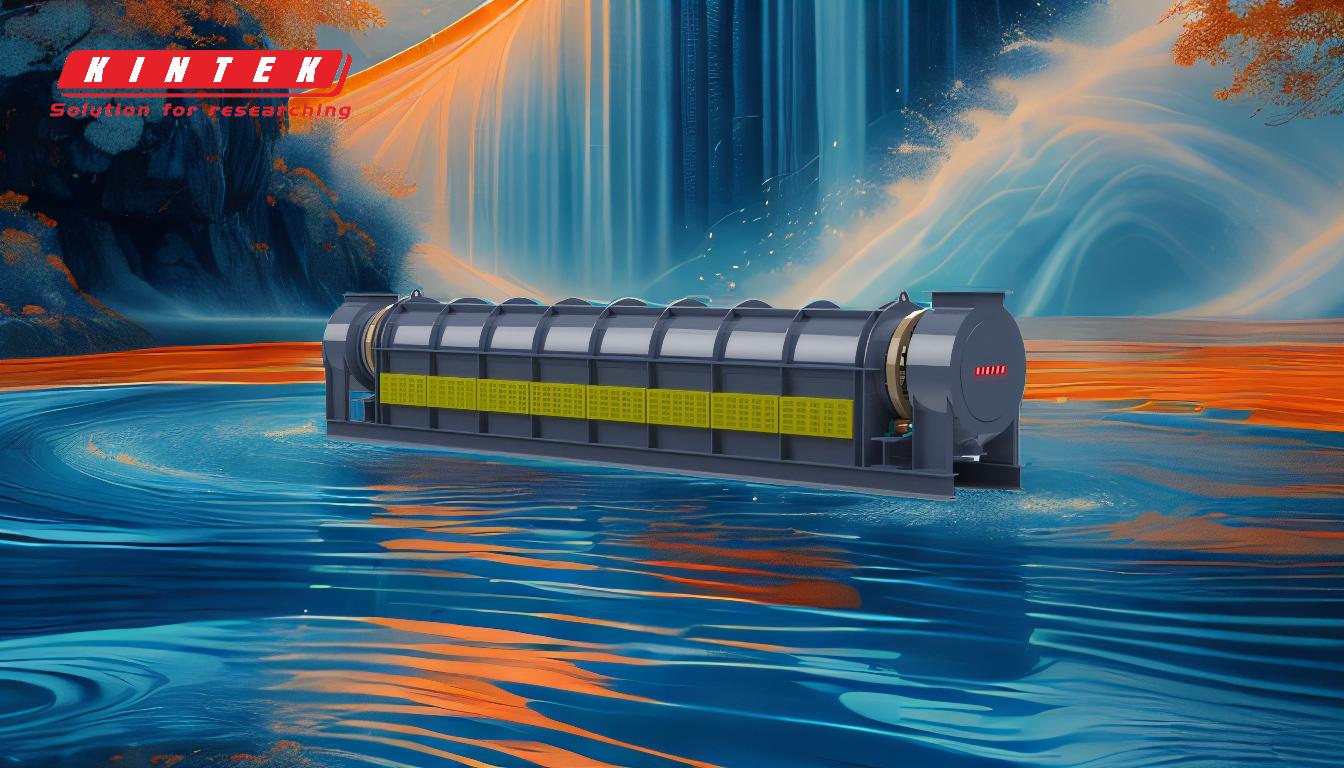
-
Primary Purpose of a Calciner:
- The main purpose of a calciner is to facilitate the calcination reaction, a high-temperature process that removes volatile components, moisture, or impurities from raw materials. This process is essential in industries like cement production, where limestone is calcined to produce clinker, the precursor to cement.
-
Key Functions of a Calciner:
- Removal of Moisture: Calciners are used to drive off absorbed moisture from materials, ensuring they are dry and ready for further processing.
- Elimination of Volatile Constituents: They remove volatile components such as carbon dioxide (CO₂) or sulfur dioxide (SO₂), which are often byproducts of chemical reactions.
- Oxidation and Chemical Transformation: Calciners can oxidize part or all of a substance, leading to desired chemical changes or the preparation of materials for subsequent steps in manufacturing.
-
Applications in Cement Production:
- In the cement industry, the calciner is a critical component of the clinker production process. It preheats raw meal and mixes it with fuel in a hot air stream to initiate the calcination of limestone, which is the first step in forming clinker.
- The calcination reaction in cement production involves heating limestone (CaCO₃) to around 900°C, causing it to decompose into lime (CaO) and CO₂.
-
Role in Metallurgy and Chemical Processing:
- In metallurgy, calciners are used to remove volatile impurities from metal ores. This process, known as calcination, involves heating the ore in the presence of limited air or oxygen to temperatures below its melting point.
- Calciners are also employed in chemical processing to prepare materials for further reactions, such as the production of alumina from bauxite or the decomposition of gypsum.
-
Versatility in High-Temperature Applications:
- Calciners are versatile and can perform multiple thermal processing functions, including drying, sintering, thermal desorption, and incineration. This makes them suitable for a wide range of industries beyond cement and metallurgy.
- For example, calciners are used in environmental applications to treat hazardous waste or in the production of advanced materials like ceramics.
-
Design and Operation of Calciners:
- Calciners are often designed as rotary kilns, which provide a continuous or batch process for high-temperature applications. Rotary kilns act as heat exchangers, ensuring efficient heat transfer and uniform heating of materials.
- The design of a calciner allows for precise temperature control, which is crucial for achieving the desired chemical reactions and material transformations.
-
Industrial Significance:
- Calciners are indispensable in industrial manufacturing due to their ability to transform raw materials into usable products. They enable the production of essential materials like cement, metals, and chemicals, contributing to infrastructure development and industrial growth.
- The efficiency and reliability of calciners make them a cornerstone of modern industrial processes, ensuring consistent quality and performance in the materials they produce.
By understanding the purpose and functions of a calciner, equipment and consumable purchasers can make informed decisions about selecting the right calcination equipment for their specific industrial needs.
Summary Table:
Key Aspect | Details |
---|---|
Primary Purpose | Facilitates calcination reactions to remove moisture, volatiles, or impurities. |
Key Functions | - Removes moisture - Eliminates volatile components - Oxidizes substances |
Applications | Cement production, metallurgy, chemical processing, environmental treatment. |
Design | Often rotary kilns for efficient heat transfer and precise temperature control. |
Industrial Significance | Transforms raw materials into usable products, enabling industrial growth. |
Need the right calciner for your industrial needs? Contact our experts today for tailored solutions!