The screw extrusion process is a widely used method in manufacturing, particularly for processing plastics and other materials. It involves using a screw mechanism within a cylindrical barrel to continuously push material through a die, shaping it into a desired profile. This process is highly efficient, allowing for high production rates and precise control over the final product's dimensions and properties. Below, we will explore the key aspects of the screw extrusion process, including its working principles, components, and applications.
Key Points Explained:
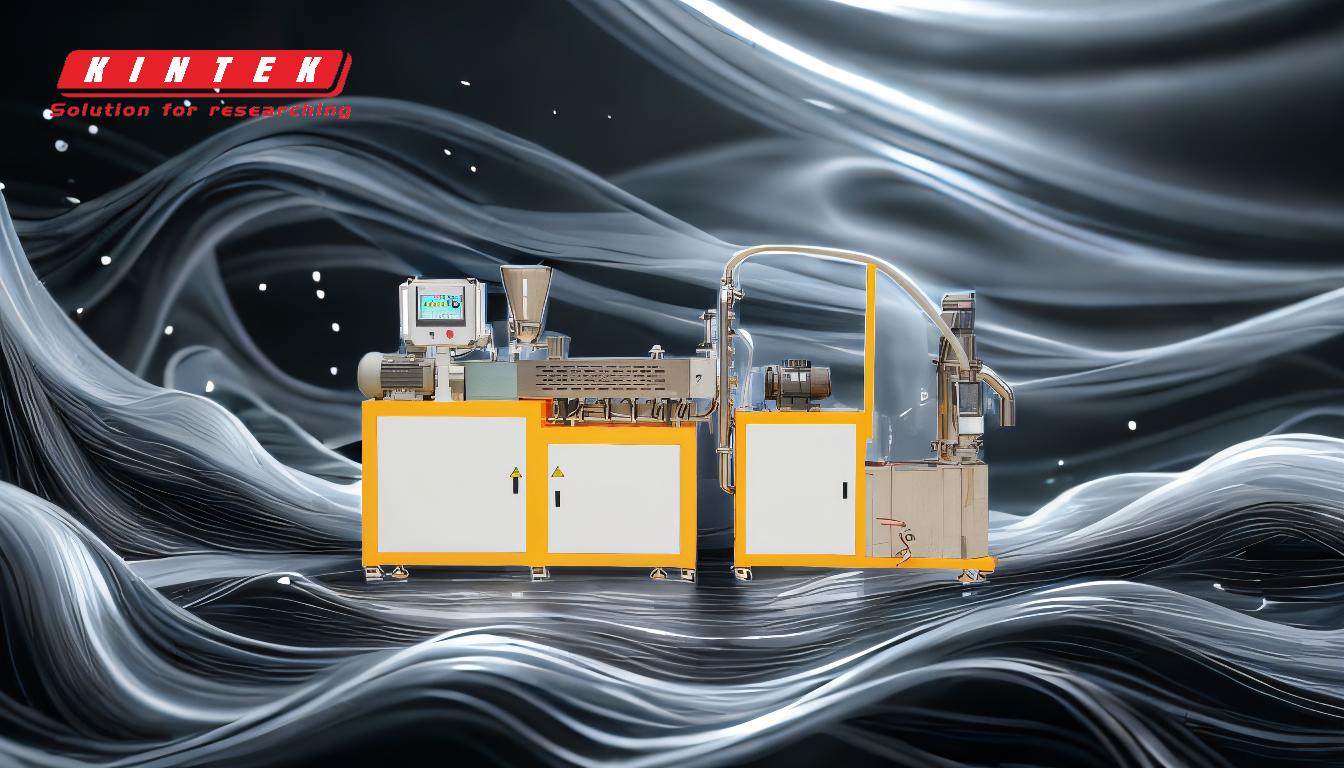
-
Definition and Overview of Screw Extrusion:
- Screw extrusion is a continuous manufacturing process where a screw rotates within a barrel to push material through a die, forming it into a specific shape.
- It is commonly used in the plastics industry but can also be applied to other materials like food, rubber, and metals.
- The process is highly versatile, allowing for the production of a wide range of products, including pipes, sheets, films, and profiles.
-
Components of a Screw Extruder:
- Screw: The central component that rotates to transport, melt, and compress the material. The screw's design (e.g., single or twin) and geometry (e.g., pitch, depth) significantly influence the process.
- Barrel: A cylindrical housing that contains the screw and provides the necessary heat and pressure for material processing.
- Die: A shaping tool located at the end of the barrel that determines the final product's cross-sectional profile.
- Heaters and Cooling Systems: Used to control the temperature of the material as it moves through the barrel.
- Drive System: Powers the rotation of the screw, typically controlled by a motor and gearbox.
-
Single Screw Extrusion:
- Single screw extrusion uses one screw within a cylindrical barrel to continuously push material through a die.
- The production rate is typically measured in mass per hour (e.g., lb/hour or kg/hour) and is controlled by the screw speed.
- This method is widely used for its simplicity, reliability, and cost-effectiveness in producing uniform products.
-
Stages of the Extrusion Process:
- Feeding: Raw material (often in pellet or powder form) is fed into the extruder through a hopper.
- Plasticization: The material is heated and melted as it moves along the screw, transitioning from a solid to a viscous state.
- Compression: The screw compresses the molten material, ensuring uniformity and removing air pockets.
- Shaping: The material is forced through the die, taking on the desired shape.
- Cooling and Solidification: The extruded product is cooled (often using water or air) to solidify its shape.
- Cutting or Coiling: The final product is cut to length or coiled for further processing.
-
Advantages of Screw Extrusion:
- High Production Rates: Continuous operation allows for large volumes of material to be processed quickly.
- Versatility: Can be used with a wide range of materials and to produce various shapes and sizes.
- Precision: The process offers excellent control over product dimensions and properties.
- Cost-Effectiveness: Efficient use of materials and energy, with minimal waste.
-
Applications of Screw Extrusion:
- Plastics: Used to produce pipes, sheets, films, and profiles for industries like construction, packaging, and automotive.
- Food Processing: Extrusion is used to create snacks, cereals, and pet food.
- Rubber and Elastomers: Used for tire treads, seals, and gaskets.
- Metals: Extrusion is employed in the production of aluminum and other metal profiles.
-
Considerations for Equipment Purchasers:
- Material Compatibility: Ensure the extruder is suitable for the specific material being processed.
- Production Capacity: Choose a machine with the appropriate screw size and speed for the desired output.
- Energy Efficiency: Look for systems with advanced heating and cooling controls to minimize energy consumption.
- Maintenance and Durability: Consider the ease of maintenance and the robustness of the equipment for long-term use.
By understanding these key points, equipment and consumable purchasers can make informed decisions about selecting and utilizing screw extrusion systems for their specific needs.
Summary Table:
Aspect | Details |
---|---|
Definition | Continuous process using a screw to push material through a die for shaping. |
Key Components | Screw, barrel, die, heaters, cooling systems, drive system. |
Advantages | High production rates, versatility, precision, cost-effectiveness. |
Applications | Plastics, food processing, rubber, metals. |
Considerations | Material compatibility, production capacity, energy efficiency, durability. |
Ready to optimize your manufacturing process? Contact us today to learn more about screw extrusion solutions!