Short-path distillation is a specialized technique used to separate components of a mixture based on their boiling points, particularly useful for heat-sensitive materials. The setup involves a series of glassware components, including a boiling flask, condenser, and receiver flask, connected in a vacuum-tight assembly. The process relies on creating a vacuum to lower the boiling points of the components, allowing for efficient separation without thermal degradation. Key steps include preparing the material, assembling the glassware, applying vacuum and heat, and monitoring the distillation process to collect fractions. The setup is often used in laboratories and small-scale production for purifying compounds like essential oils, cannabinoids, and other high-value chemicals.
Key Points Explained:
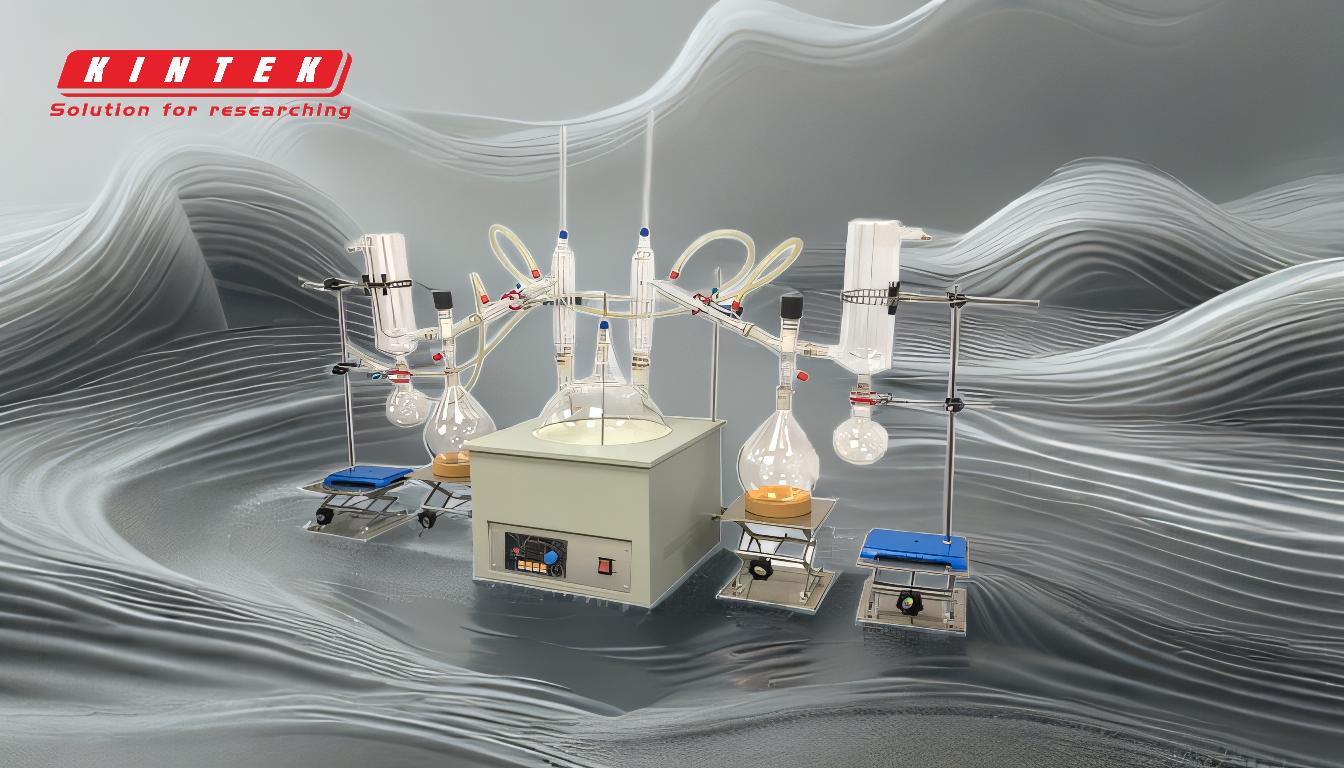
-
Components of a Short-Path Distillation Setup:
- Boiling Flask: Holds the material to be distilled and is heated to evaporate the components.
- Condenser: Cools the vaporized components, causing them to condense back into liquid form.
- Receiver Flask: Collects the condensed fractions.
- Vacuum Pump: Creates a vacuum to lower the boiling points of the components, enabling separation at lower temperatures.
- Heating Mantle: Provides controlled heat to the boiling flask.
- Cold Trap: Prevents volatile components from reaching the vacuum pump by condensing them.
-
Preparation of Material:
- Winterization and Decarbing: Pre-treatment steps to remove impurities and activate certain compounds, especially in cannabis or plant extracts.
- Loading the Boiling Flask: The prepared material is placed in the boiling flask, ensuring it is free of particulates that could clog the system.
-
Assembly and Setup:
- Greasing Joints: All glassware joints are greased to ensure a vacuum-tight seal, preventing leaks that could disrupt the vacuum.
- Orienting the Receiver Cow: The receiving flask is positioned correctly to collect the fractions as they condense.
- Connecting the Vacuum Pump: The vacuum pump is connected to the system, and the vacuum is established before heating begins.
-
Operation Steps:
- Applying Heat and Vacuum: The heating mantle is set to an initial temperature (45-60°C), and the vacuum is gradually increased to prevent over-boiling.
- Monitoring the Process: The liquid level in the boiling flask is monitored, and material is added as needed. The temperature and vacuum are adjusted to optimize separation.
- Collecting Fractions: Different fractions are collected in the receiver flask based on their boiling points.
-
Cooling and Shutdown:
- Cooling Down: After distillation, the system is allowed to cool before turning off the vacuum pump.
- Cleaning: The glassware is cleaned to remove any residue, ensuring the system is ready for the next use.
-
Advanced Considerations:
- Continuous Mode Systems: More complex setups, like KINTEK’s Wiped-Film Molecular Still (WFMS), allow for continuous distillation, improving efficiency for large-scale operations.
- Temperature Control: Precise control of heating and cooling is critical to prevent thermal degradation of sensitive compounds.
- Vacuum Management: Maintaining a stable vacuum is essential for consistent separation and to avoid bumping or over-boiling.
By following these steps and considerations, a short-path distillation setup can effectively separate and purify complex mixtures, making it a valuable tool in both laboratory and industrial settings.
Summary Table:
Component | Function |
---|---|
Boiling Flask | Holds and heats the material to evaporate components. |
Condenser | Cools vaporized components, causing them to condense back into liquid form. |
Receiver Flask | Collects the condensed fractions. |
Vacuum Pump | Creates a vacuum to lower boiling points for efficient separation. |
Heating Mantle | Provides controlled heat to the boiling flask. |
Cold Trap | Prevents volatile components from reaching the vacuum pump. |
Ready to optimize your distillation process? Contact us today for expert guidance and solutions!