The electron beam in an electron beam system is primarily generated by heating a tungsten filament within the electron gun. This process, known as thermionic emission, occurs when a high voltage (up to 10 kV) is applied to the filament, causing it to emit electrons. These electrons form the electron beam, which is then focused and directed through a vacuum chamber to interact with the evaporant material. The vacuum environment ensures the unimpeded propagation of the electron beam. Other methods, such as field-electron emission or anodic-arc techniques, can also generate electron beams, but thermionic emission using a tungsten filament is the most common approach.
Key Points Explained:
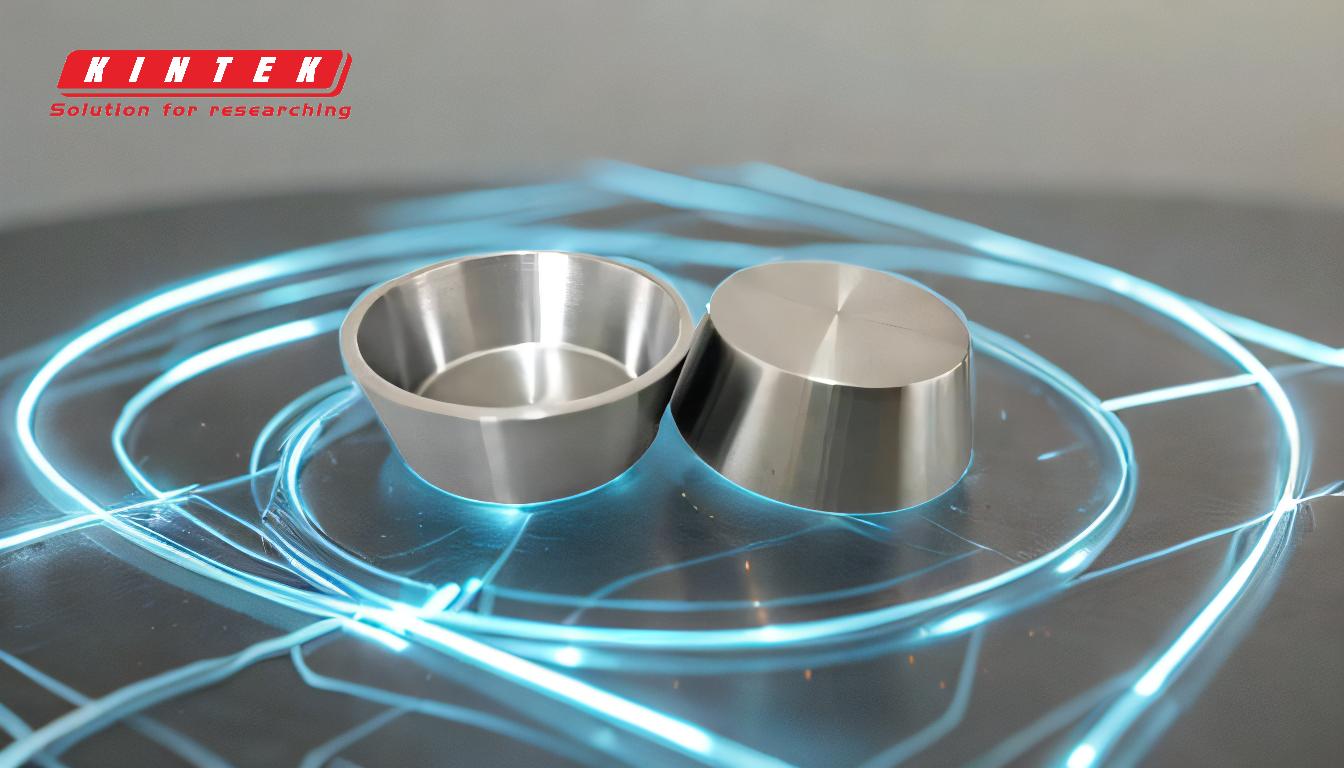
-
Electron Beam Generation via Thermionic Emission:
- The electron beam is generated by heating a tungsten filament in the electron gun.
- A high voltage (up to 10 kV) is applied to the filament, causing it to emit electrons through thermionic emission.
- This process is the most common method for generating electron beams in systems like electron beam evaporators.
-
Role of the Tungsten Filament:
- The filament, often shaped as a tungsten hairpin, acts as the cathode in the electron gun.
- Tungsten is used due to its high melting point and ability to withstand high temperatures without degrading.
- The filament's design ensures efficient electron emission and beam generation.
-
Vacuum Environment:
- Both the electron gun and the work chamber are evacuated to create a vacuum.
- The vacuum prevents interference from air molecules, ensuring the electron beam propagates unimpeded to the evaporant material.
-
Alternative Electron Beam Generation Methods:
- Besides thermionic emission, electron beams can also be generated through:
- Field-Electron Emission: Electrons are emitted due to a strong electric field.
- Anodic-Arc Methods: Electrons are generated via an arc discharge between electrodes.
- These methods are less common but may be used in specialized applications.
- Besides thermionic emission, electron beams can also be generated through:
-
Components of an Electron Beam System:
- Electron Gun: Contains the filament and generates the electron beam.
- Crucibles: Hold the evaporation materials that are heated by the electron beam to coat the substrate.
- Vacuum Chamber: Houses the substrate and crucibles, maintaining the vacuum environment necessary for electron beam propagation.
-
Applications and Importance:
- Electron beams are critical in processes like electron beam evaporation, where they heat materials to create thin films or coatings.
- The precise control of the electron beam allows for high-quality, uniform coatings on substrates.
By understanding these key points, equipment and consumable purchasers can make informed decisions about the components and systems required for their specific applications. The choice of filament material, vacuum system quality, and electron beam generation method all play crucial roles in the performance and efficiency of the system.
Summary Table:
Aspect | Details |
---|---|
Electron Beam Generation | Generated via thermionic emission by heating a tungsten filament. |
Tungsten Filament | Acts as the cathode; withstands high temperatures for efficient emission. |
Vacuum Environment | Ensures unimpeded electron beam propagation by eliminating air interference. |
Alternative Methods | Field-electron emission and anodic-arc techniques (less common). |
System Components | Electron gun, crucibles, and vacuum chamber. |
Applications | Used in electron beam evaporation for thin film coatings and more. |
Need help selecting the right electron beam system for your application? Contact our experts today!