The sputtering method is a thin film deposition technique widely used in various industries, including semiconductors, optics, and coatings. It involves the ejection of atoms from a solid target material through bombardment by high-energy ions, typically from an inert gas like argon. These ejected atoms then deposit onto a substrate to form a thin film. The process occurs in a vacuum chamber to prevent contamination and ensure precise control over the deposition. Sputtering is valued for its ability to produce uniform, high-quality coatings, even on heat-sensitive materials, and its versatility in depositing a wide range of materials, including metals, alloys, and ceramics.
Key Points Explained:
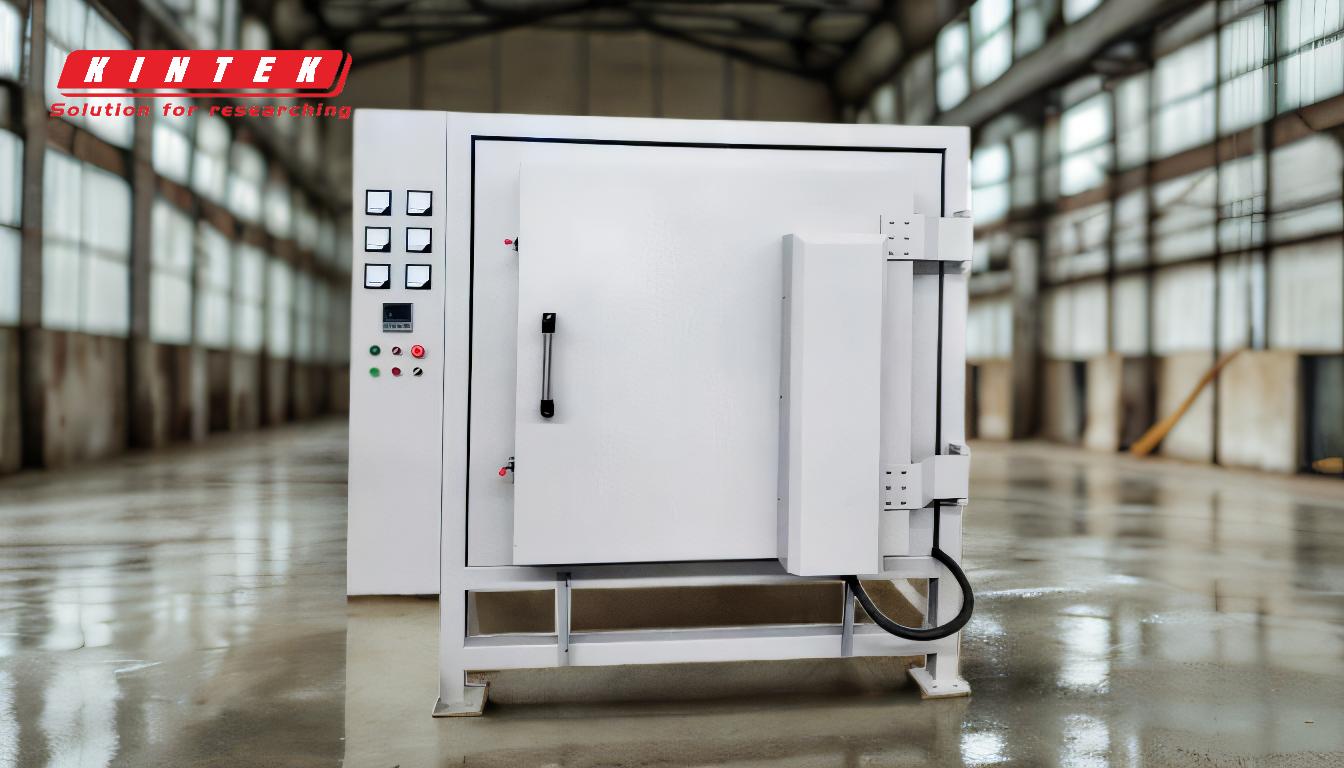
-
Basic Principle of Sputtering:
- Sputtering is a physical vapor deposition (PVD) technique where atoms are ejected from a solid target material due to bombardment by high-energy ions.
- The process involves a vacuum chamber, a target material (cathode), and a substrate where the ejected atoms deposit to form a thin film.
- A controlled gas, typically argon, is introduced into the chamber and ionized to create a plasma. The positively charged ions are accelerated toward the negatively charged target, causing atoms to be ejected.
-
Role of Plasma and Ion Bombardment:
- Plasma is generated by applying a high voltage (several hundred volts) between the target and the chamber walls.
- Inert gas atoms (e.g., argon) become ionized in the plasma, forming positively charged ions.
- These ions are accelerated toward the target, colliding with it and transferring momentum to the target atoms, which are then ejected.
-
Vacuum Environment:
- Sputtering occurs in a high-vacuum environment to minimize interactions with air or other unwanted gases.
- The vacuum ensures that the ejected atoms travel ballistically toward the substrate without scattering or contamination.
-
Deposition Process:
- Ejected atoms from the target form a vapor stream that deposits onto the substrate.
- The substrate is typically mounted opposite the target, and the deposition occurs layer by layer, forming a thin film.
- The process can be controlled to achieve precise thickness and uniformity.
-
Advantages of Sputtering:
- Versatility: Suitable for depositing a wide range of materials, including metals, alloys, ceramics, and compounds.
- Uniformity: Produces highly uniform coatings, even on complex geometries.
- Low Temperature: Ideal for heat-sensitive substrates like plastics, as the sputtered particles have low thermal energy.
- Adhesion: The high kinetic energy of the sputtered atoms ensures strong adhesion to the substrate.
-
Applications of Sputtering:
- Semiconductors: Used for depositing thin films in integrated circuits and microelectronics.
- Optics: Used for anti-reflective coatings, mirrors, and optical filters.
- Coatings: Applied in wear-resistant, decorative, and functional coatings.
- Solar Cells: Used in the production of thin-film photovoltaic devices.
-
Types of Sputtering:
- DC Sputtering: Uses direct current to generate plasma, suitable for conductive materials.
- RF Sputtering: Uses radio frequency for non-conductive materials.
- Magnetron Sputtering: Enhances sputtering efficiency using magnetic fields to confine electrons near the target.
- Reactive Sputtering: Involves reactive gases to form compound films (e.g., oxides, nitrides).
-
Momentum Transfer and Collision Cascade:
- The ejection of target atoms is driven by momentum transfer during ion bombardment.
- A collision cascade occurs when the energy from the incident ions is transferred to the target atoms, causing them to be dislodged.
-
Re-Sputtering:
- In some cases, deposited material may be re-sputtered due to further ion bombardment, which can help refine the film's properties.
-
Equipment and Setup:
- A typical sputtering system includes a vacuum chamber, target material, substrate holder, gas inlet, and power supply.
- The system is designed to maintain high vacuum, control gas flow, and apply the necessary voltage for plasma generation.
In summary, the sputtering method is a highly controlled and versatile thin film deposition technique that relies on ion bombardment to eject atoms from a target material and deposit them onto a substrate. Its ability to produce uniform, high-quality coatings on a variety of materials makes it indispensable in modern manufacturing and research.
Summary Table:
Aspect | Details |
---|---|
Principle | Ejection of atoms from a target via ion bombardment in a vacuum environment. |
Key Components | Vacuum chamber, target material, substrate, inert gas (e.g., argon). |
Advantages | Uniform coatings, low-temperature process, strong adhesion, versatility. |
Applications | Semiconductors, optics, coatings, solar cells. |
Types | DC, RF, Magnetron, Reactive Sputtering. |
Equipment | Vacuum chamber, power supply, gas inlet, substrate holder. |
Discover how sputtering can enhance your thin film processes—contact our experts today!