The sputtering process in semiconductors is a well-established Physical Vapor Deposition (PVD) technique used to deposit thin films of materials onto substrates. This method involves generating plasma containing argon ions and electrons, which then collide with a target material, ejecting its atoms. These atoms travel through the plasma and deposit onto a substrate, forming a thin, high-purity film. Sputtering is crucial in semiconductor manufacturing for creating high-quality coatings, such as gold layers on circuit chips, due to its ability to produce films with extreme purity and precise thickness. The process is widely used in applications ranging from reflective coatings to advanced semiconductor devices.
Key Points Explained:
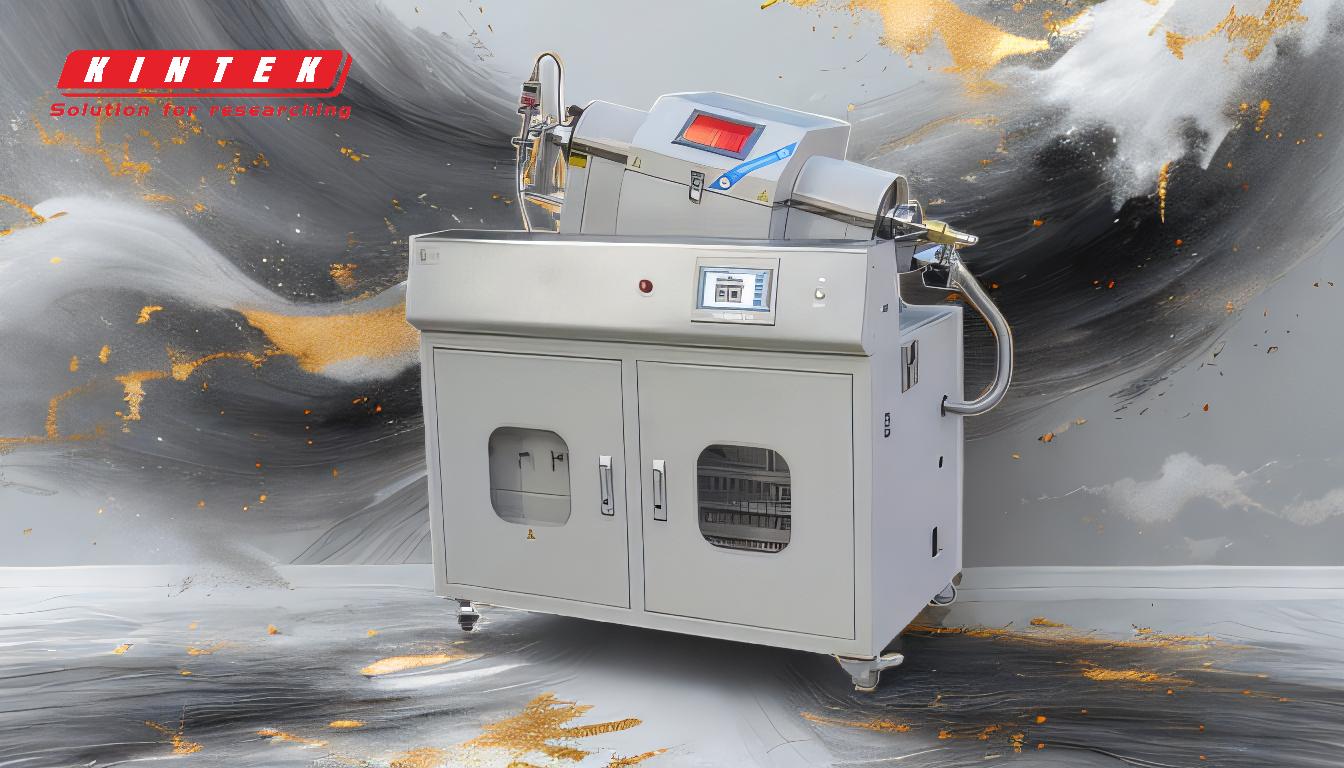
-
Definition and Historical Context of Sputtering:
- Sputtering is a PVD technique that has been in use since the early 1800s. It is a mature and reliable method for depositing thin films of materials onto various substrates.
- The process is essential in industries such as semiconductor manufacturing, where high-quality, pure coatings are required for components like circuit chips and boards.
-
Mechanism of Sputtering:
- The process begins with the generation of plasma, which contains argon ions and electrons. This plasma is created within a vacuum chamber.
- When a voltage is applied between the vacuum chamber and a target electrode made of the material to be deposited, the argon ions are accelerated toward the target.
- The collision of these high-energy ions with the target material causes atoms to be ejected from the target surface. These ejected atoms then travel through the plasma and deposit onto the substrate, forming a thin film.
-
Role of Plasma and Argon Ions:
- Plasma is a key component in the sputtering process, as it provides the high-energy ions necessary to eject atoms from the target material.
- Argon is commonly used as the inert gas in the plasma because it is chemically inert and does not react with the target material, ensuring the purity of the deposited film.
-
Applications in Semiconductor Manufacturing:
- Sputtering is widely used in the semiconductor industry to deposit thin films of materials such as gold, which has excellent electrical and thermal conductivity.
- The process allows for the deposition of extremely pure, single-atom-thick layers of gold, which are essential for the high-performance requirements of semiconductor components.
- Sputtering targets must be free of impurities to ensure the quality and functionality of the deposited films.
-
Advantages of Sputtering in Semiconductor Production:
- High Purity: The sputtering process can produce films with extreme purity, which is critical for semiconductor applications.
- Precision: Sputtering allows for precise control over the thickness and composition of the deposited films, making it ideal for creating thin, uniform layers.
- Versatility: The technique can be used to deposit a wide range of materials, including metals, alloys, and compounds, making it suitable for various semiconductor applications.
-
Process Parameters and Control:
- The sputtering process involves several key parameters, including the voltage applied, the pressure within the vacuum chamber, and the type of gas used.
- Controlling these parameters is essential to achieve the desired film properties, such as thickness, uniformity, and adhesion to the substrate.
-
Challenges and Considerations:
- Target Purity: The target material must be free of impurities to ensure the quality of the deposited film. Any contamination can negatively impact the performance of the semiconductor device.
- Uniformity: Achieving a uniform film thickness across the entire substrate can be challenging, especially for large or complex substrates.
- Cost: The sputtering process can be expensive due to the need for high-purity materials and specialized equipment.
In summary, the sputtering process is a critical technique in semiconductor manufacturing, enabling the deposition of high-purity, thin films with precise control over thickness and composition. Its ability to produce uniform, high-quality coatings makes it indispensable for the production of advanced semiconductor devices.
Summary Table:
Key Aspect | Details |
---|---|
Definition | A Physical Vapor Deposition (PVD) technique for thin film deposition. |
Mechanism | Plasma with argon ions ejects target atoms, depositing them on substrates. |
Applications | Used in semiconductor manufacturing for gold layers, reflective coatings. |
Advantages | High purity, precise thickness control, and material versatility. |
Challenges | Target purity, uniformity, and cost considerations. |
Discover how sputtering can enhance your semiconductor production—contact our experts today!