The sputtering process is a widely used thin-film deposition technique that involves ejecting atoms from a solid target material and depositing them onto a substrate to form a thin, uniform coating. The process occurs in a vacuum chamber where an inert gas, typically argon, is ionized to create a plasma. Positively charged ions from the plasma are accelerated toward a negatively charged target, causing atoms to be ejected from the target surface. These ejected atoms then travel through the vacuum and deposit onto the substrate, forming a thin film. The process is highly controllable and can produce coatings with excellent adhesion, uniformity, and purity, making it suitable for applications in electronics, optics, and industrial coatings.
Key Points Explained:
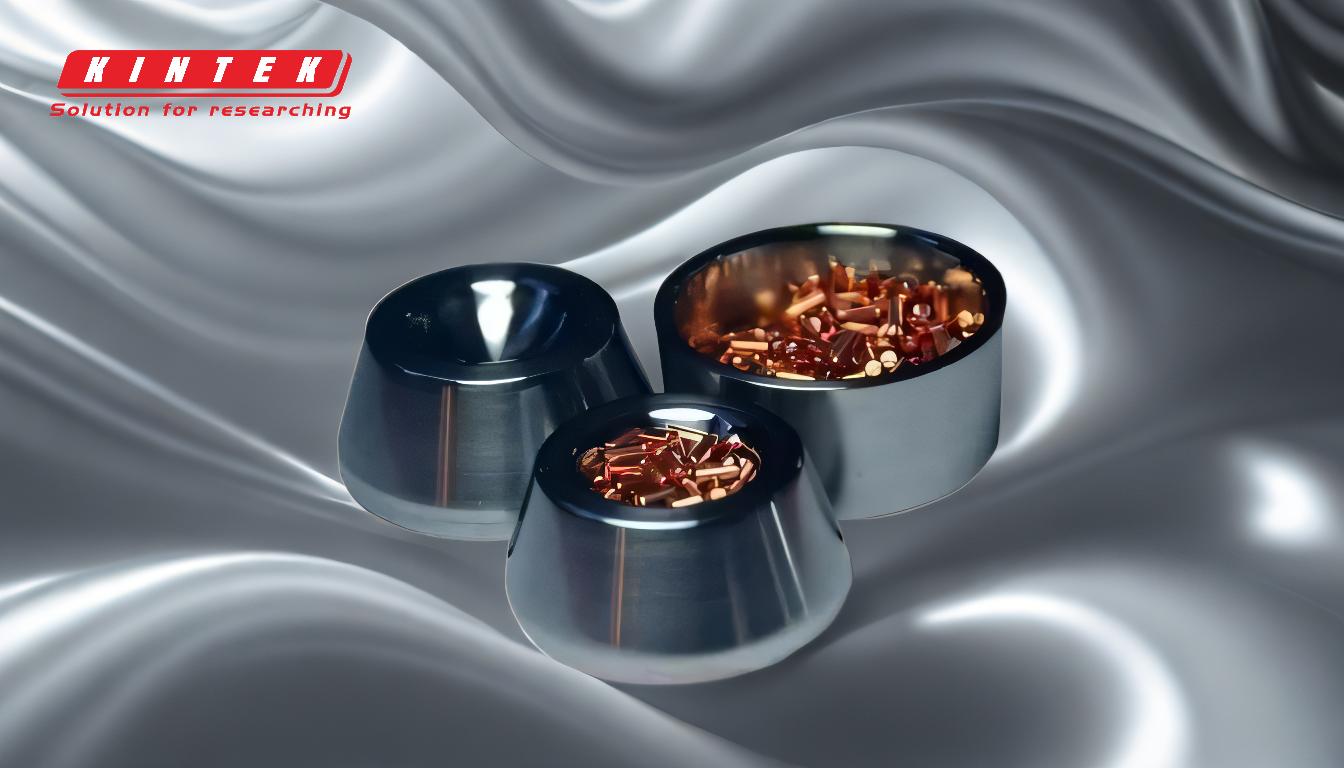
-
Vacuum Chamber Setup:
- The sputtering process begins by creating a vacuum inside the reaction chamber. The pressure is reduced to around 1 Pa (0.0000145 psi) to eliminate moisture and impurities that could interfere with the deposition process.
- A vacuum environment ensures that the sputtered atoms travel freely without colliding with air molecules, which could disrupt the uniformity of the thin film.
-
Introduction of Inert Gas:
- An inert gas, typically argon, is introduced into the chamber to create a low-pressure atmosphere. Argon is preferred because it is chemically inert and does not react with the target material or the substrate.
- The gas pressure is carefully controlled to optimize the ionization process and ensure efficient sputtering.
-
Plasma Generation:
- A high voltage (3-5 kV) is applied to ionize the argon gas, creating a plasma composed of positively charged argon ions (Ar+) and free electrons.
- The plasma is confined and directed using a magnetic field, which enhances the ionization efficiency and focuses the ions toward the target material.
-
Target Material Bombardment:
- The target material, which serves as the cathode, is negatively charged. This attracts the positively charged argon ions, which accelerate toward the target and collide with its surface.
- The energy from these collisions ejects atoms from the target material in a process known as sputtering.
-
Transport of Sputtered Atoms:
- The ejected atoms travel through the vacuum chamber and deposit onto the substrate. The low-pressure environment ensures that the atoms move in a straight line, resulting in a uniform and well-adhered thin film.
- The substrate is typically positioned opposite the target to maximize the deposition efficiency.
-
Film Formation:
- As the sputtered atoms reach the substrate, they condense and form a thin film. The thickness and properties of the film can be controlled by adjusting parameters such as the sputtering time, power, and gas pressure.
- The resulting film is highly uniform, with excellent adhesion and purity, making it suitable for a wide range of applications.
-
Temperature Control:
- The chamber may be heated to temperatures ranging from 150°C to 750°C (302°F to 1382°F), depending on the specific coating being applied. Heating can improve the film's adhesion and crystallinity.
- Temperature control is critical for achieving the desired film properties and ensuring compatibility with the substrate material.
-
Applications and Variations:
- Sputtering is used in various industries, including electronics (e.g., semiconductor manufacturing), optics (e.g., anti-reflective coatings), and industrial coatings (e.g., wear-resistant surfaces).
- Variations of the sputtering process, such as magnetron sputtering and reactive sputtering, are used to achieve specific film properties or deposit complex materials.
By following these steps, the sputtering process enables the precise deposition of thin films with tailored properties, making it a versatile and essential technique in modern manufacturing and material science.
Summary Table:
Key Step | Description |
---|---|
Vacuum Chamber Setup | Pressure reduced to ~1 Pa for a clean, collision-free environment. |
Inert Gas Introduction | Argon gas introduced to create a low-pressure atmosphere for ionization. |
Plasma Generation | High voltage ionizes argon, creating a plasma for sputtering. |
Target Bombardment | Positively charged argon ions collide with the target, ejecting atoms. |
Atom Transport | Ejected atoms travel through vacuum, depositing onto the substrate. |
Film Formation | Atoms condense into a thin, uniform film with excellent adhesion and purity. |
Temperature Control | Chamber heated (150°C–750°C) to optimize film adhesion and crystallinity. |
Applications | Used in electronics, optics, and industrial coatings for tailored thin films. |
Discover how the sputtering process can enhance your manufacturing—contact us today to learn more!