The temperature of a carbon regeneration kiln typically ranges from 100°C to 800°C, depending on the stage of the process. In the initial heating phase, the temperature is raised from 100°C to 750°C within the first 1300mm of the tube. In the final 1000mm, known as the soak zone, the temperature can reach up to 800°C. This high temperature is crucial for the gasification of pyrolytic residue through a controlled chemical reaction with water vapor, effectively regenerating the carbon.
Key Points Explained:
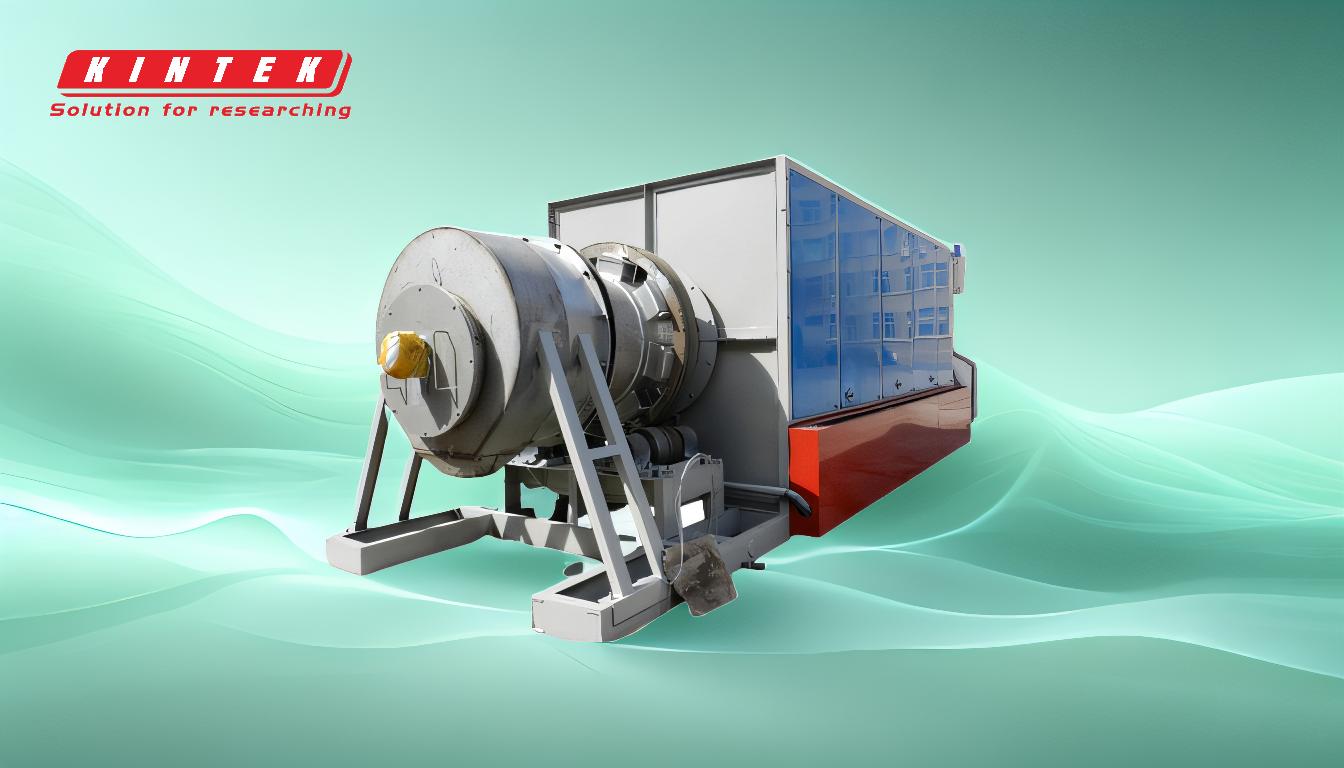
-
Temperature Range in the Initial Heating Phase:
- 100°C to 750°C: The temperature is gradually increased from 100°C to 750°C within the first 1300mm of the kiln tube. This phase is critical for preheating the carbon and preparing it for the subsequent high-temperature treatment.
-
Temperature in the Soak Zone:
- Up to 800°C: In the final 1000mm of the kiln tube, the temperature can reach up to 800°C. This section is known as the soak zone, where the carbon undergoes a controlled chemical reaction with water vapor. The high temperature is essential for the gasification of pyrolytic residue, which is a key step in the regeneration process.
-
Purpose of High Temperature:
- Gasification of Pyrolytic Residue: The elevated temperature in the soak zone facilitates the gasification of pyrolytic residue. This process involves a controlled chemical reaction with water vapor, which helps in breaking down the residue and regenerating the carbon. The high temperature ensures that the reaction occurs efficiently and effectively.
-
Controlled Chemical Reaction:
- Interaction with Water Vapor: The controlled chemical reaction with water vapor at high temperatures is a critical aspect of the carbon regeneration process. This reaction helps in the removal of impurities and the regeneration of the carbon, making it ready for reuse.
-
Kiln Design and Temperature Zones:
- Zoned Heating: The kiln is designed with specific temperature zones to ensure that the carbon is heated gradually and then subjected to the high temperatures needed for gasification. The initial heating phase and the soak zone are carefully controlled to optimize the regeneration process.
-
Importance of Temperature Control:
- Precision in Heating: Precise control of the temperature is vital for the successful regeneration of carbon. The gradual increase in temperature and the maintenance of high temperatures in the soak zone are necessary to achieve the desired chemical reactions and ensure the quality of the regenerated carbon.
In summary, the temperature of a carbon regeneration kiln is carefully controlled and varies depending on the stage of the process. The initial heating phase raises the temperature from 100°C to 750°C, while the soak zone can reach up to 800°C. These high temperatures are essential for the gasification of pyrolytic residue and the effective regeneration of carbon.
Summary Table:
Stage | Temperature Range | Purpose |
---|---|---|
Initial Heating Phase | 100°C to 750°C | Preheats carbon and prepares it for high-temperature treatment. |
Soak Zone (Final 1000mm) | Up to 800°C | Facilitates gasification of pyrolytic residue through controlled reactions. |
Need a carbon regeneration kiln tailored to your process? Contact us today for expert guidance!