Thermal regeneration of activated carbon is a process that restores the adsorption capacity of spent activated carbon by removing the adsorbed impurities through high-temperature treatment. This method involves heating the carbon to temperatures typically between 600°C and 900°C in the presence of a controlled atmosphere (often steam or inert gas), which decomposes or volatilizes the adsorbed contaminants. The regenerated carbon can then be reused, making the process both cost-effective and environmentally sustainable. This approach is widely used in industries where activated carbon is employed for purification, such as water treatment, air filtration, and chemical processing.
Key Points Explained:
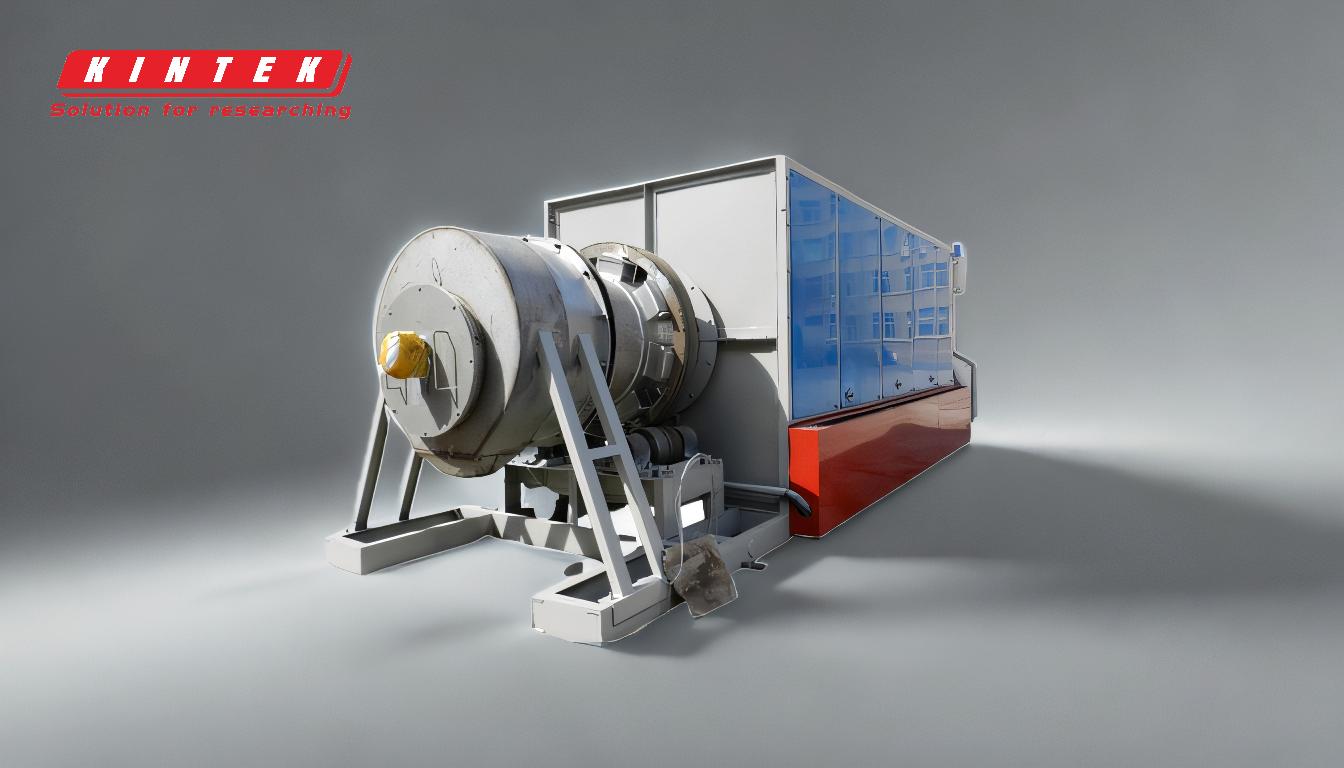
-
Definition and Purpose of Thermal Regeneration:
- Thermal regeneration is a process designed to restore the adsorption capacity of activated carbon that has become saturated with contaminants.
- The primary goal is to remove the adsorbed impurities, allowing the carbon to be reused, which reduces waste and operational costs.
-
How Thermal Regeneration Works:
- The process involves heating the spent activated carbon to high temperatures (typically 600°C to 900°C) in a controlled environment.
- The heat causes the adsorbed contaminants to decompose, oxidize, or volatilize, effectively cleaning the carbon surface.
- The regenerated carbon retains its porous structure, enabling it to adsorb impurities again.
-
Key Steps in the Thermal Regeneration Process:
- Drying: The spent carbon is first dried to remove moisture, which is essential to prevent steam explosions during the high-temperature phase.
- Pyrolysis: The carbon is heated in an oxygen-free or low-oxygen environment to break down organic contaminants into smaller molecules.
- Activation: Steam or carbon dioxide is introduced to burn off residual carbon deposits and restore the carbon's porosity.
- Cooling: The regenerated carbon is cooled before being reused or stored.
-
Advantages of Thermal Regeneration:
- Cost-Effectiveness: Reusing activated carbon reduces the need for frequent replacements, lowering operational costs.
- Environmental Benefits: Regeneration minimizes waste and reduces the environmental impact associated with disposing of spent carbon.
- Efficiency: Properly regenerated carbon can perform nearly as well as virgin carbon, maintaining high adsorption capacity.
-
Applications of Thermally Regenerated Activated Carbon:
- Water Treatment: Used in municipal and industrial water purification systems to remove organic contaminants, chlorine, and odors.
- Air Filtration: Employed in air purification systems to capture volatile organic compounds (VOCs) and other airborne pollutants.
- Chemical Processing: Utilized in the recovery of solvents and the purification of chemicals.
-
Challenges and Considerations:
- Energy Consumption: The high temperatures required for regeneration make the process energy-intensive.
- Carbon Loss: Repeated regeneration cycles can lead to a gradual loss of carbon mass and adsorption capacity.
- Contaminant Type: Not all adsorbed contaminants can be effectively removed through thermal regeneration; some may require alternative methods.
-
Comparison with Other Regeneration Methods:
- Chemical Regeneration: Involves using solvents or chemicals to desorb contaminants. While effective for certain applications, it may not be suitable for all types of contaminants and can generate chemical waste.
- Biological Regeneration: Uses microorganisms to degrade adsorbed organic contaminants. This method is less energy-intensive but slower and less effective for non-biodegradable pollutants.
In summary, thermal regeneration is a widely used and effective method for restoring the adsorption capacity of activated carbon. It offers significant economic and environmental benefits, though it requires careful management of energy use and carbon loss. Understanding the process and its applications can help equipment and consumable purchasers make informed decisions about carbon management strategies.
Summary Table:
Key Aspect | Details |
---|---|
Temperature Range | 600°C to 900°C |
Process Steps | Drying, Pyrolysis, Activation, Cooling |
Advantages | Cost-effective, environmentally sustainable, high efficiency |
Applications | Water treatment, air filtration, chemical processing |
Challenges | Energy-intensive, carbon loss, limited effectiveness for certain contaminants |
Comparison with Other Methods | Chemical regeneration (chemical waste), biological regeneration (slower) |
Discover how thermal regeneration can optimize your carbon management—contact our experts today!